What is Single Pass Jetting™?
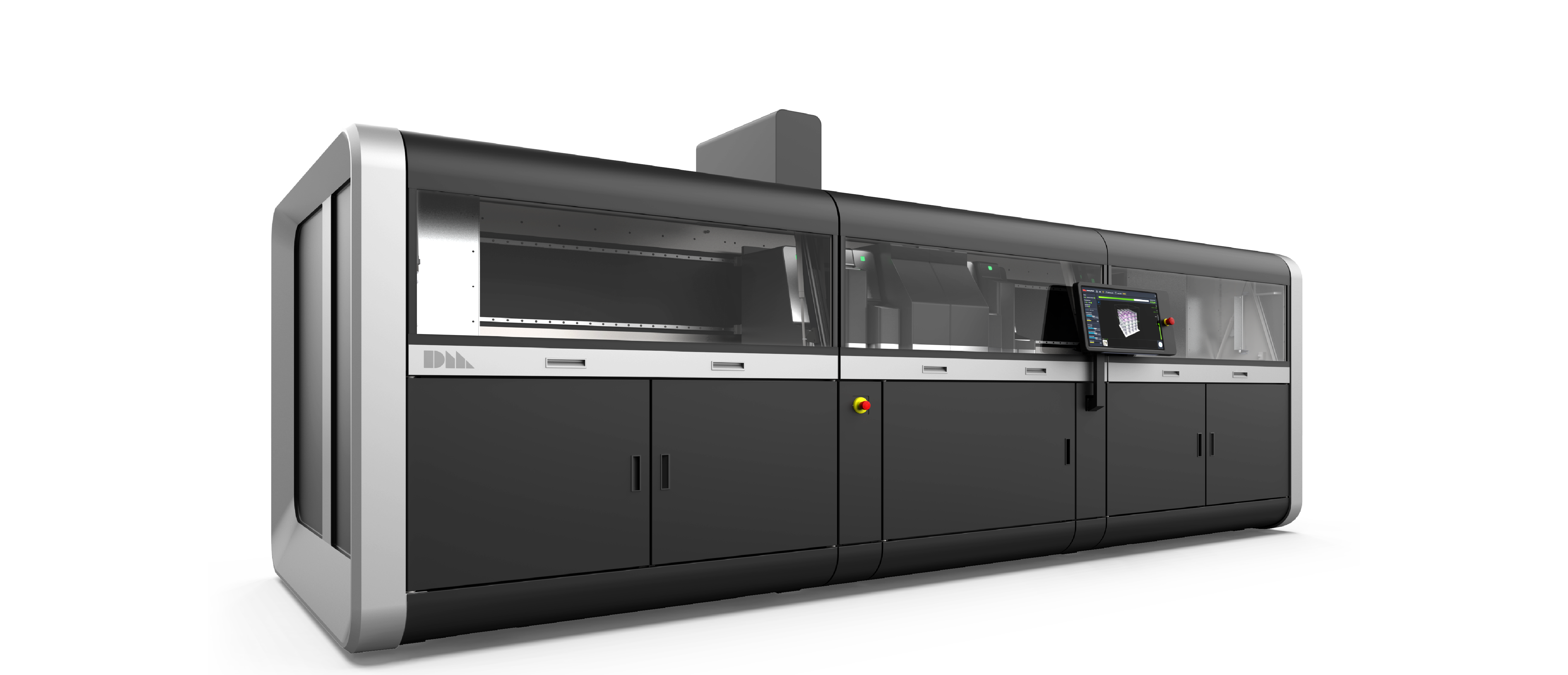
Designed to be the fastest way to additively manufacture metal parts, the Desktop Metal Production System derives its speed from a collection of technologies that together are called Single Pass Jetting™.
The Production System is, at its core, a binder jetting system. Invented in the late 1980s in the labs of MIT by Ely Sachs, one of Desktop Metal’s founders, binder jetting is a relatively straightforward process. All binder jet systems execute similar steps to create a three-dimensionally printed part.
The basics of Binder Jetting
1. First, fresh powder is deposited onto the print bed. There are several ways to perform this step. Some printers use what’s called “bed-to-bed” powder metering where the powder is supplied from a feed piston, and that powder is then pushed on top of the print bed. Alternatively, the powder can be metered from above and the metering device is translated across the bed to distribute the powder.
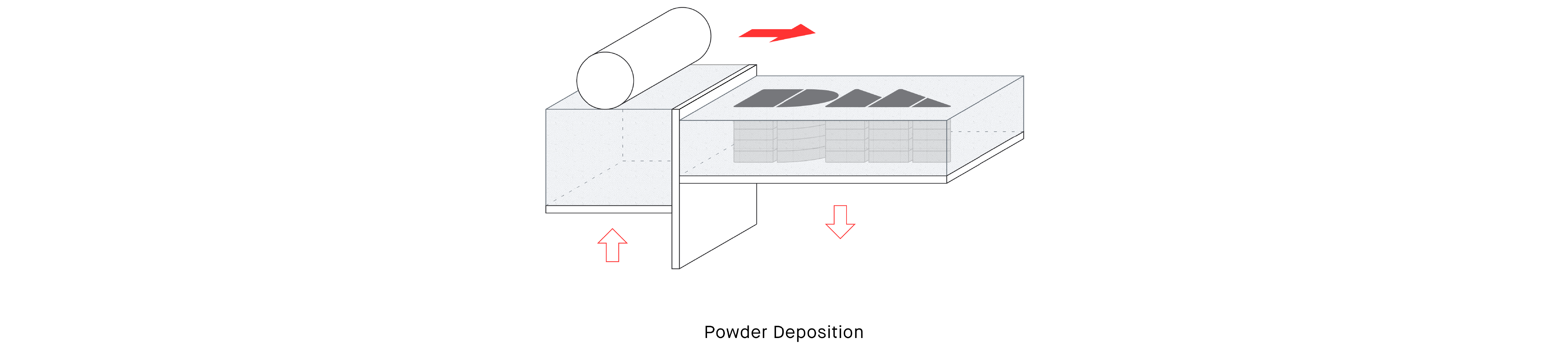
2. Next, the freshly deposited powder is spread uniformly across the bed and slightly compacted. Vibrating blades and counter-rotating rollers two examples of the typical ways this can be accomplished.
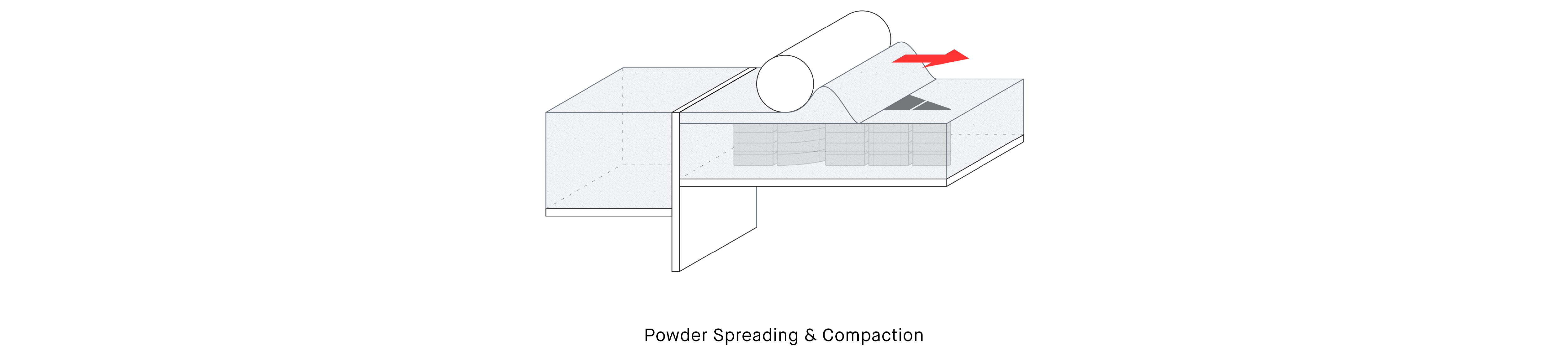
3. Now the powder bed is ready to receive the binder. The binder is typically patterned onto the bed using inkjet technology. One or more inkjet print heads make up an array of nozzles that can eject drops precisely where the binder is needed. That array is translated in at least one direction across the build box during this step. It’s crucial that every pixel be addressable. If the inkjet array is shorter than the build box OR if the print heads have a lower native resolution than the desired print resolution, it is necessary to translate the inkjet nozzle array in two dimensions to complete the printing (as illustrated below).
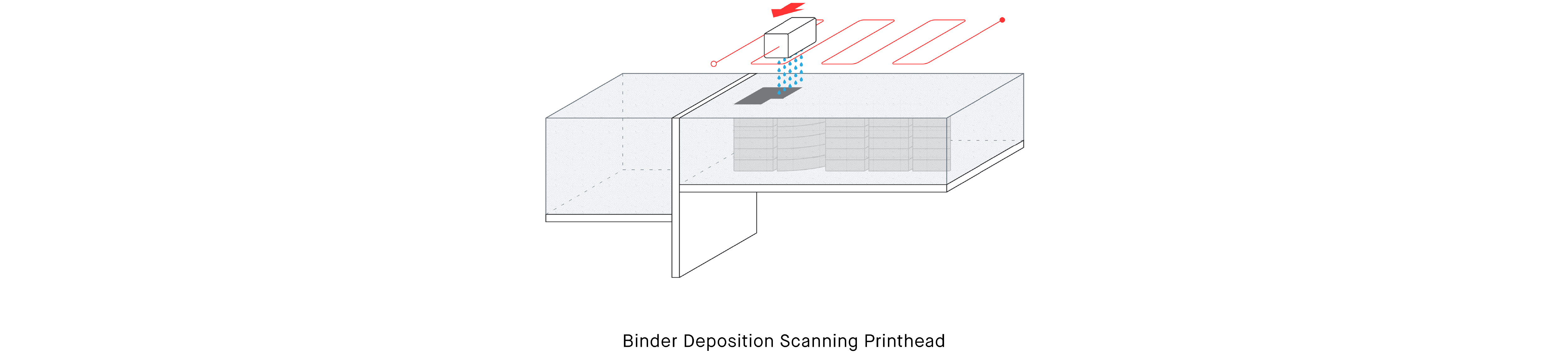
4. A final (and sometimes optional) step is to dry or post-treat the printed bed containing the wet binder.
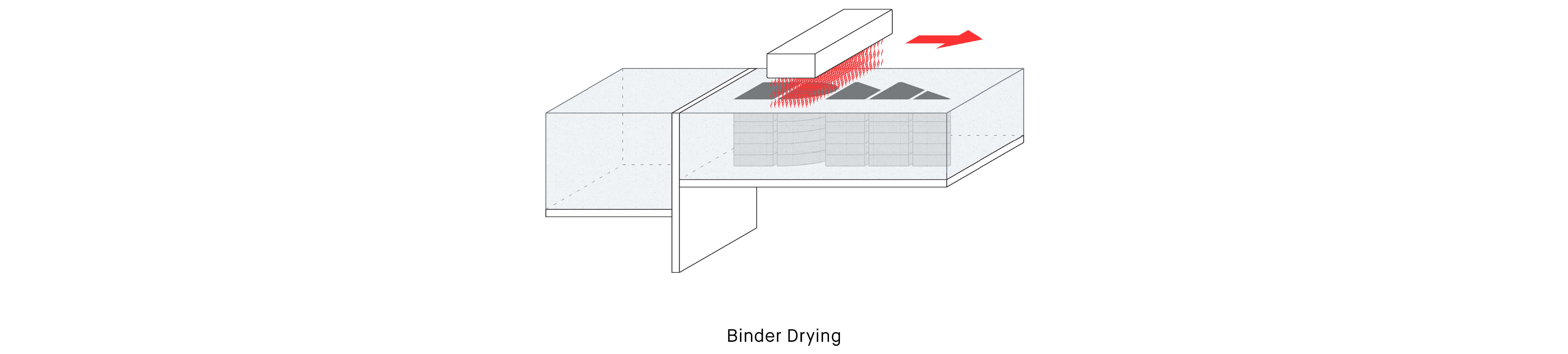
These steps are then repeated for the next layer, and the process repeats until the build is completed.
All binder jet systems employ process steps similar to these, though there are a great number of variations around these themes. When the steps are performed serially and through a separate motion of components, each step must be completed before the next can begin. This approach is typical for binder jetting, and as a result, it can take 20 seconds or more to complete each layer. While that may sound fast, a single build box can require thousands of layers to complete. And for very thin layers, the number of layers (and the time to complete the build box) increases proportionately.
Single Pass Jetting
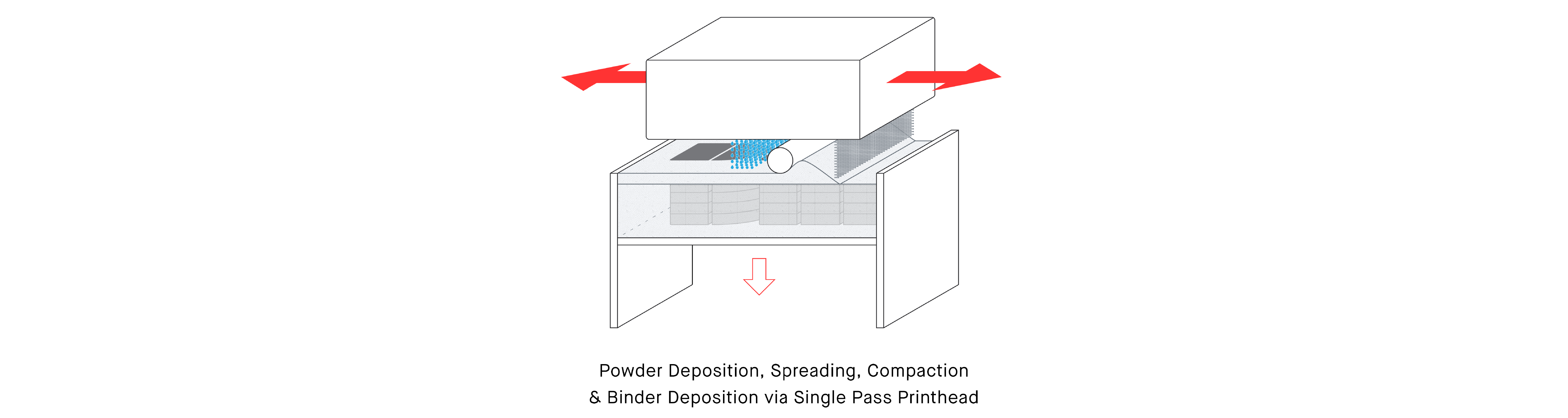
This is where Single Pass Jetting (SPJ)™ sets itself apart. SPJ takes all of those binder jetting process steps and combines them into a single, unified step. With a single pass of the integrated carriage, a full layer is completed. By performing these steps concurrently, each layer is completed in as little as 3 seconds, dramatically accelerating the printing process and delivering the unprecedented speeds of the Desktop Metal Production System.
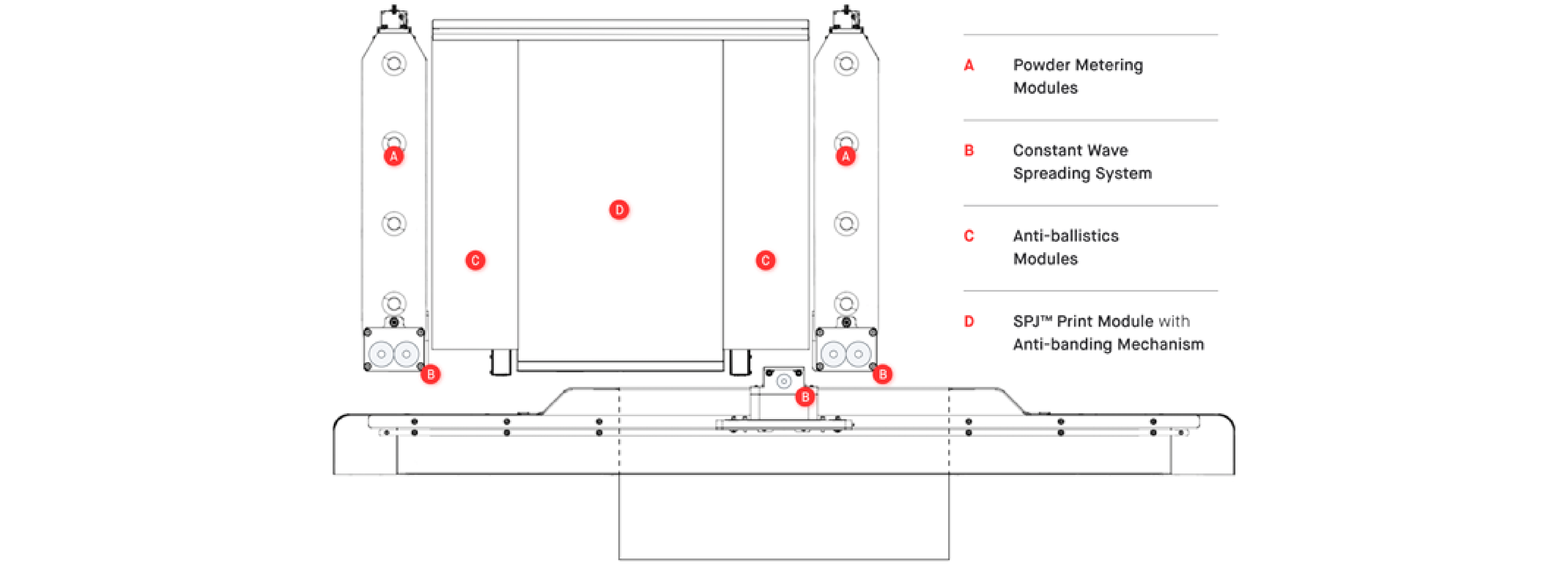
This schematic illustrates the various modules of the P-50 printer carriage. It is those modules that work in concert to produce a finished layer.
A. The process starts with powder dispensing. The Desktop Metal Production printer includes two hoppers to hold fresh powder. This powder is automatically conveyed to the hoppers through the Powder Process Unit (PPU).
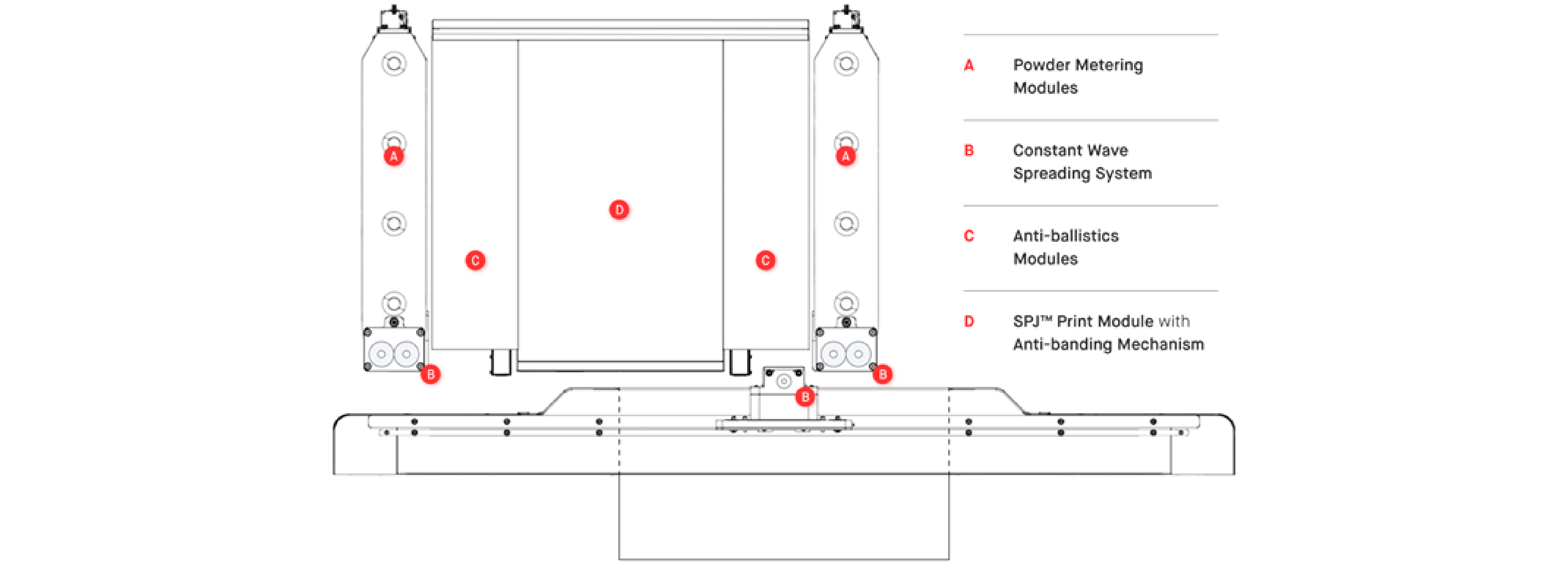
B. 1. The powder is controllably metered from the hoppers onto the bed through a precise gap between two counter-rotating rollers. Our SPJ™ Technology uses an approach called Constant Wave Spreading[SB1] to produce a consistent “wave” of powder in front of the compaction roller, resulting in consistent bed density (a key requirement to deliver tight geometrical tolerances and consistency).
2. The compaction roller works in coordination with the metering to spread and slightly compact the dispensed powder.
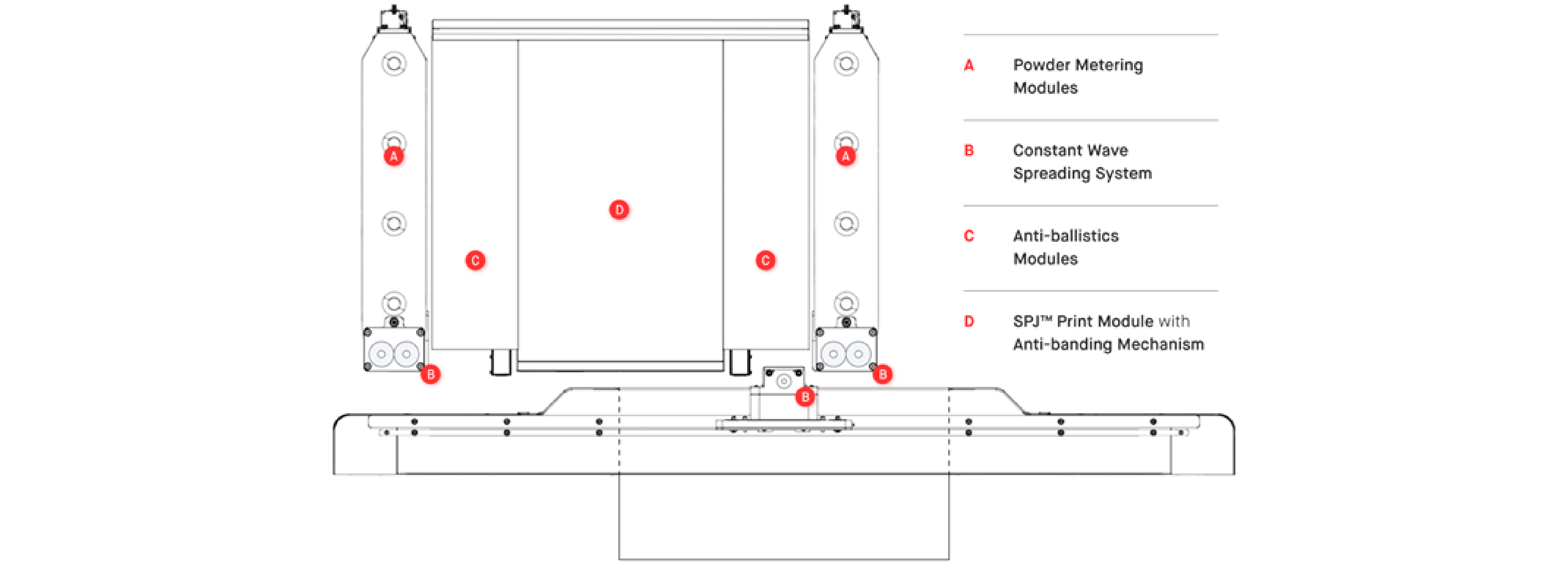
C. A technology unique to the Desktop Metal Production System, the anti-ballistics module [SB2] treats the freshly compacted powder bed to control particles during the printing process. Drops from the inkjet print heads are expelled at up to 8 meters per second. When they hit the powder bed, some of that kinetic energy is transferred to the particles within the bed. Left uncontrolled, the particles can fly back toward the inkjet print heads and, over time, clog the nozzles. Anti-ballistics technology eliminates this ejecta, greatly improving jetting reliability.
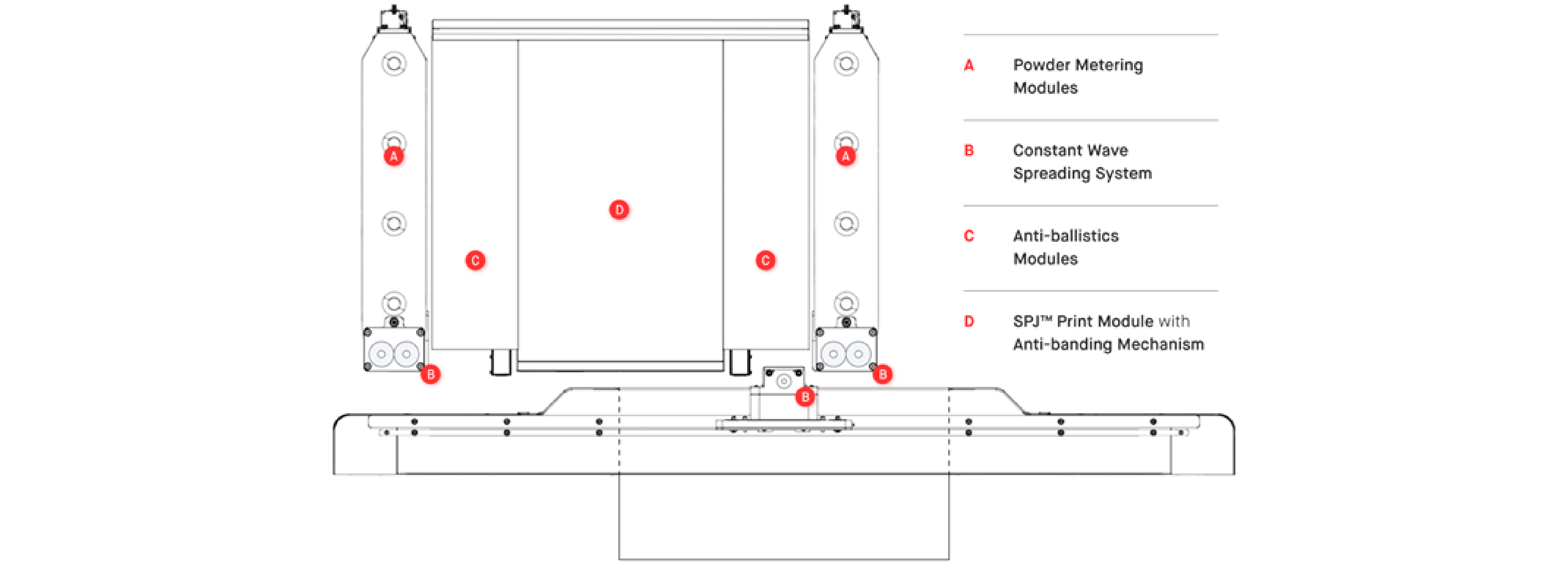
D. The printing module carries the inkjet print array [SB3], which is capable of addressing each 1200x1200dpi pixel location on the bed in a single pass. Desktop Metal intentionally chose the highest performing industrial inkjet print head in order to deliver high resolution and high throughput in a single pass. By addressing the powder bed through an array of nozzles, the Production System realizes a 100X speed improvement over vector-based methods like powder bed fusion. Additionally, the entire array employs anti-banding technology, meaning it can be shuttled between every layer. By moving the array slightly in the direction orthogonal to the schematic above, ensuring consistent binder coverage in the case of an occasional nozzle drop out.
Within seconds, this process produces a completed layer. The symmetrical design of the carriage means the same steps can be reproduced if the carriage traverses the bed in the opposite direction. That bidirectional printing capability ensures maximum productivity with no wasted motion. As soon as a layer is complete, the build platform drops according to the layer height and immediately begins printing the next layer.
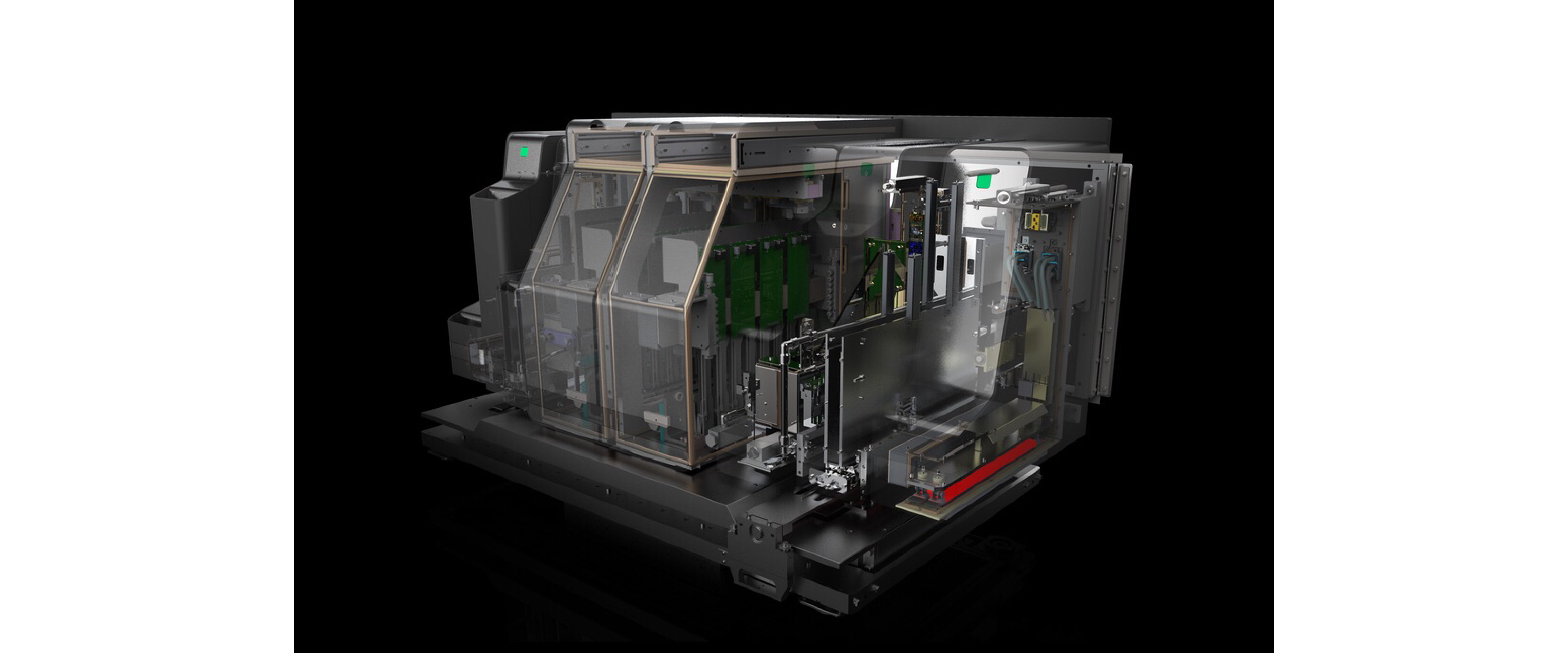
Another key aspect of all of the technologies comprising Single Pass Jetting is their scalability. Increasing the size of the build box in any dimension is possible with relatively simple changes to the modules. This means the technology can advance over time and grow with future opportunities.
In summary, binder jet represents a significant leap forward in productivity compared to conventional metal additive approaches. Using an array of nozzles to address the print bed, binder jet can be many times faster than vector-based approaches that are common in the market today. Desktop Metal’s Single Pass Jetting system pushes binder jetting technology forward, consolidating all the binder jet steps into a single carriage, eliminating all wasted motion and producing completed layers in just seconds. All of this combines to deliver productivity orders of magnitude faster than competitive methods while making no sacrifice on print resolution or part quality.