Built for ease-of-use, performance, and reliability. All-new vacuum furnace for combined debinding and sintering features breakthrough industrial performance at an affordable price.
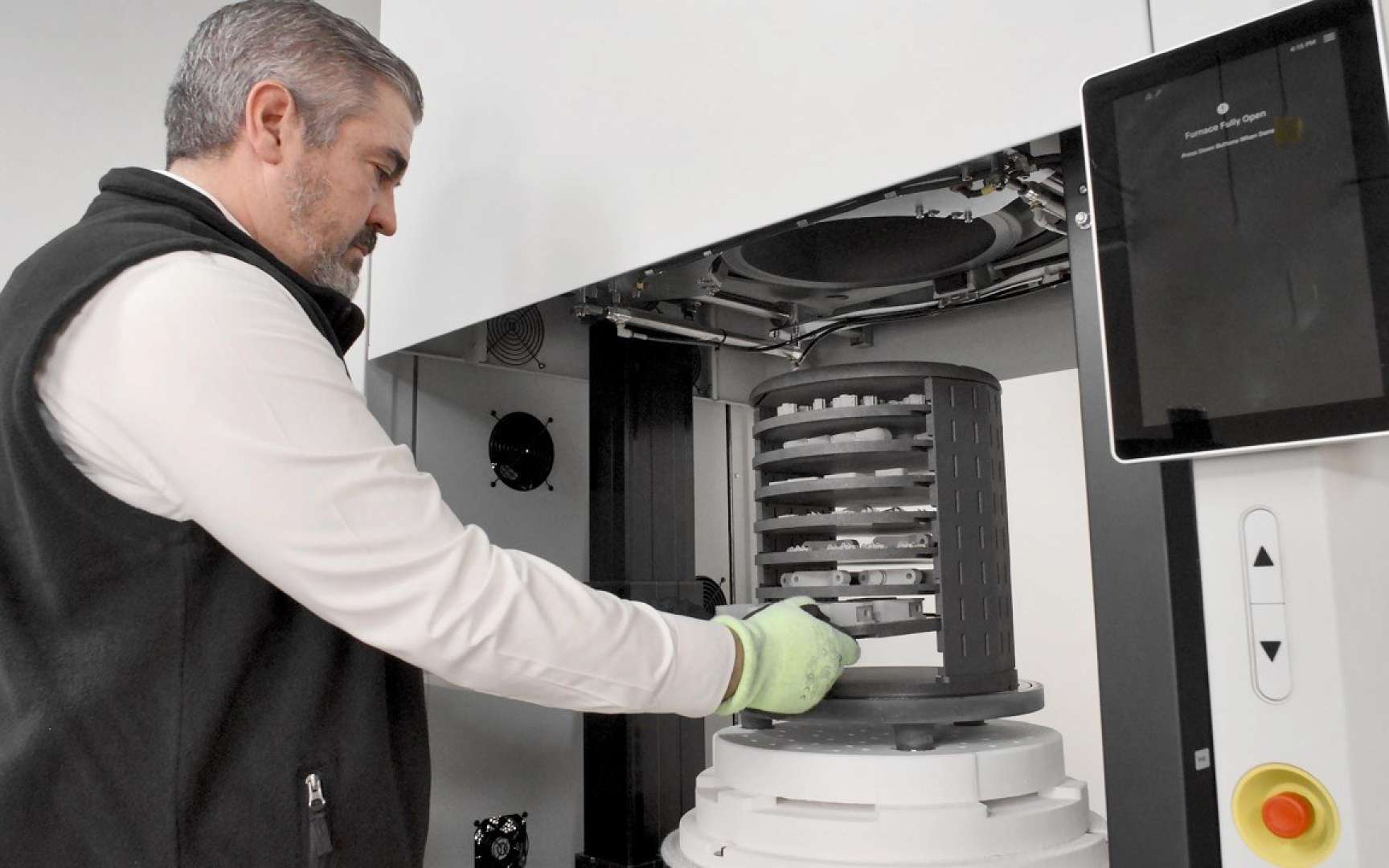
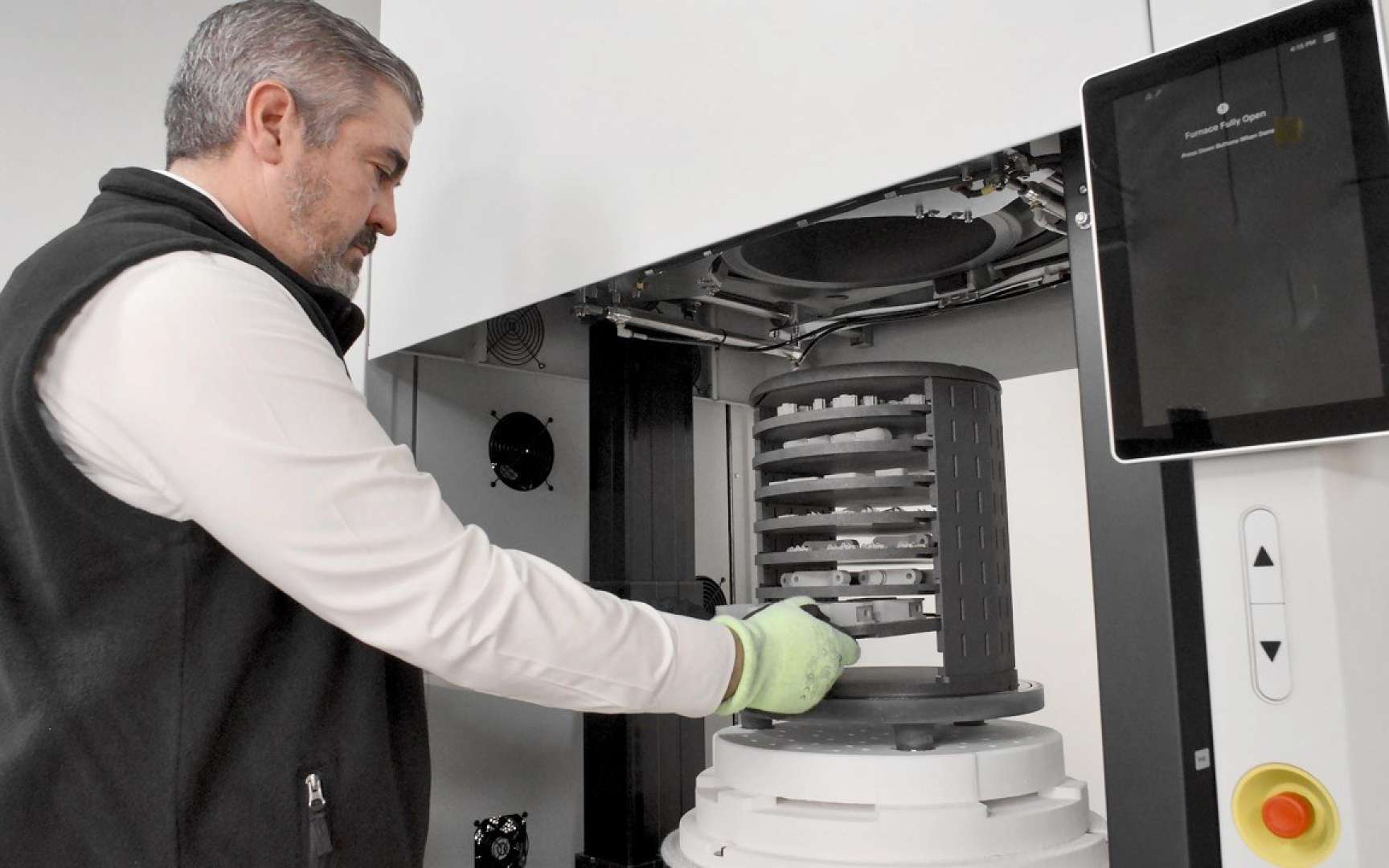
-
— 01
High Purity
-
— 02
High Efficiency
-
— 03
High Reliability
BREAKTHROUGH FURNACE FOR SIMPLIFIED SINTERING
Just as our popular Live Sinter™ simulation software predicts and corrects for sintering deformation, our new PureSinter™ Furnace — years in the making — is a breakthrough for cleaner, more efficient, and reliable sintering. Importantly, PureSinter is designed as a total industry solution — not just for sinter-based AM, but also for PM, MIM, and other sectors that could benefit from a compact, high-purity vacuum furnace.
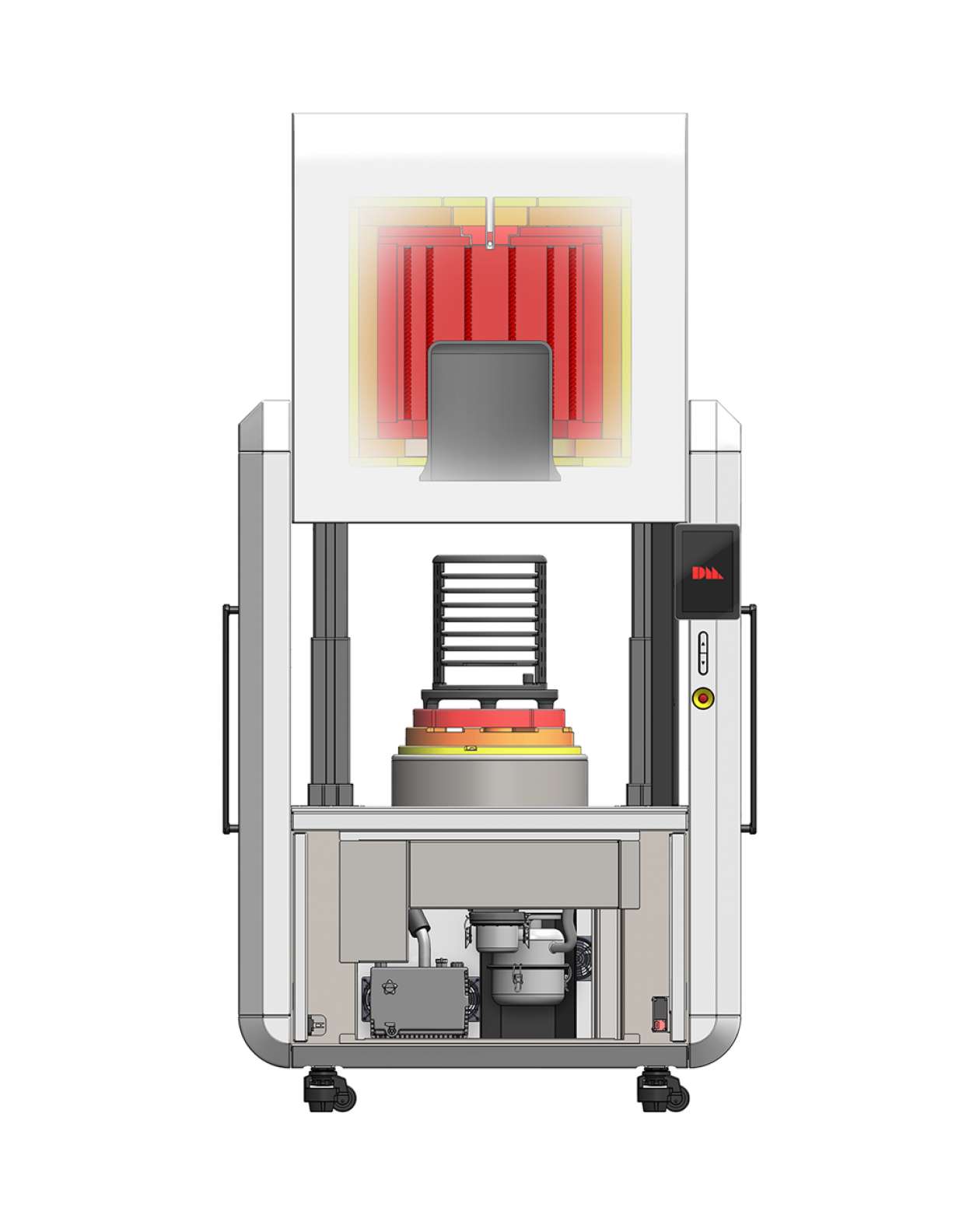
Built for ease of use, performance, and reliability
This affordable, state-of-the-art furnace features an all-new design that was rethought from the ground up with an innovative vacuum retort approach to deliver ultra-high levels of purity and solve the challenges of traditional vacuum furnaces. PureSinter delivers the highest quality sintered parts, on par or better than industrial furnaces with higher acquisition and operating costs. Even titanium can be easily sintered with a high degree of confidence without the complex preparations required with other furnaces. PureSinter is Ti-Tested™ with excellent results.
Innovative Vertical Design
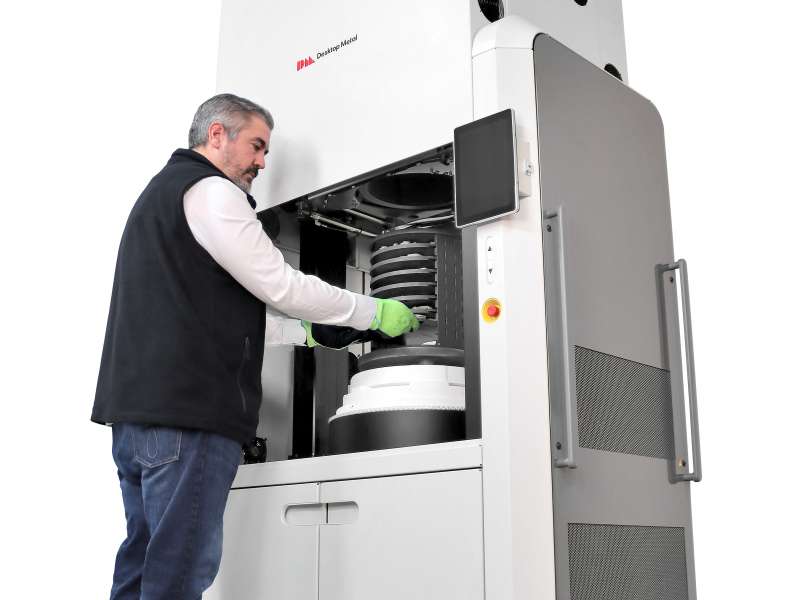
The first thing you’ll notice about PureSinter is the vertical design with a Thermal Hood that lifts up and down. The hood contains insulation, 12 standard resistive heating elements, and also supports a silicon carbide (SiC) Vacuum Retort dome. Load and unload parts when the hood is up and, when you’re ready to sinter, lower the hood, which seals the vacuum retort. With PureSinter, there are no doors (or internal boxes) to close and seal. All up-and-down operation is done with the touch of two-hand control buttons for safety.
Download BrochureModern User Experience
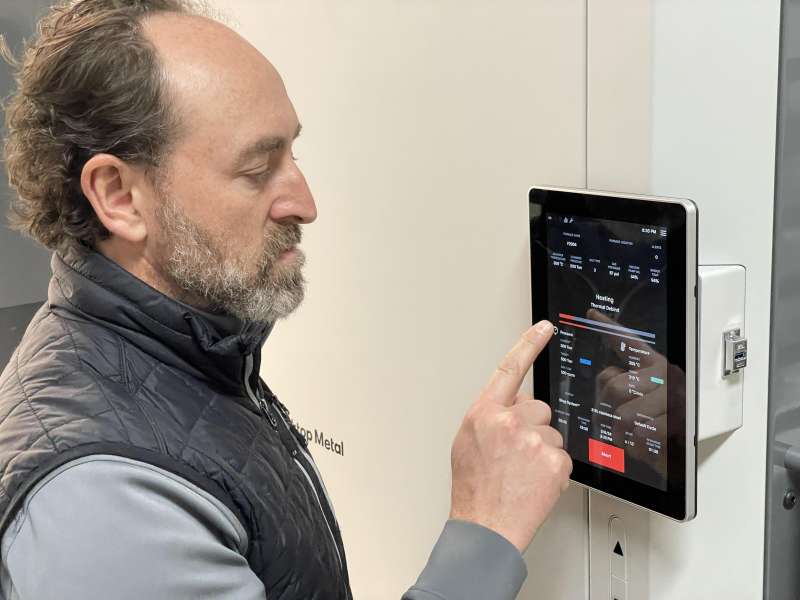
PureSinter offers a modern touchscreen to guide users through operation and maintenance and access pre-programmed furnace parameters for Desktop Metal materials and systems1, or program your own. The touchscreen, in combination with the machine’s Thermal Hood controls, also raises and lowers the hood. Once the hood is open, you’ll have unparalleled
visibility into your furnace from either the front or back, eliminating the confined feeling of most traditional furnaces. Behind the machine’s lower doors, you’ll find an easily accessible binder trap.
Simple Sintering Software
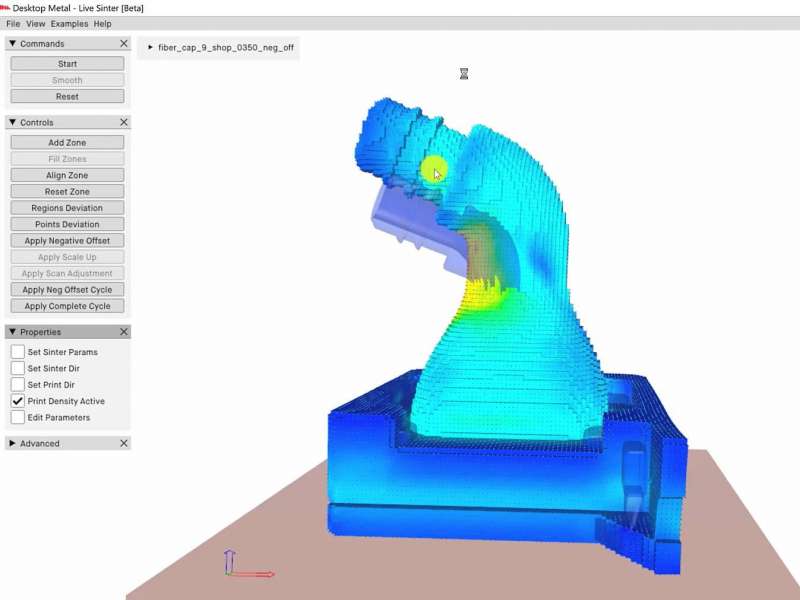
The Desktop Metal PureSinter Furnace comes standard with Live Sinter software² to produce design files for geometries that can be pressed, molded, or 3D printed and sintered to perfection. Our easy-to-use multiphysics simulation software predicts part behavior during sintering and automatically compensates for distortion and other effects. It also enables users to further refine results with easy scan-based adjustments, in addition to other helpful features.
Learn more about Live SinterHigh Effciency = Low Operating Costs
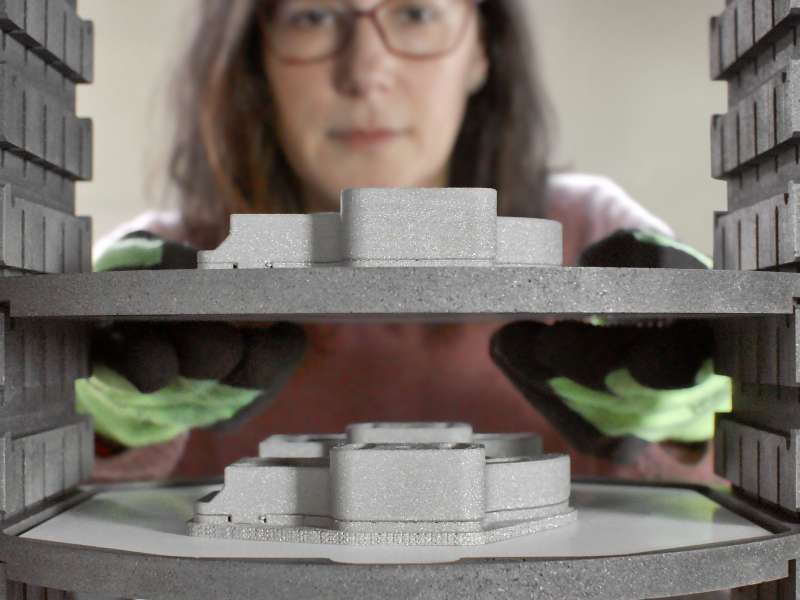
With a high-purity seal and an efficient cooling system, the energy requirements for the PureSinter furnace offer a dramatic improvement over other traditional furnaces that it competes with on performance. The electrical requirements are 200-220 V, 40A, 3ph, 50/60hZ or 380-415V, 20A, 3ph, 50/60hZ.
Download Brochure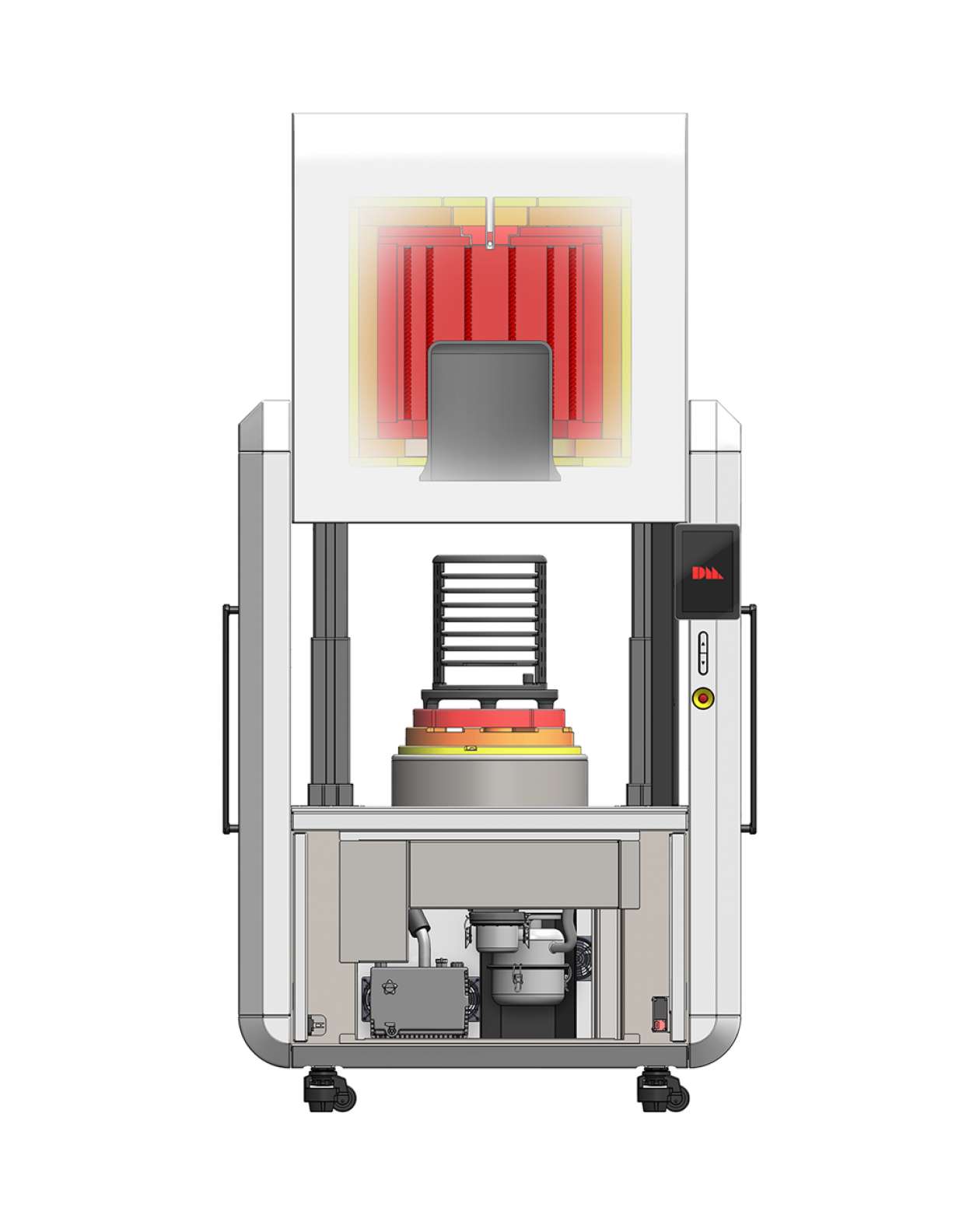
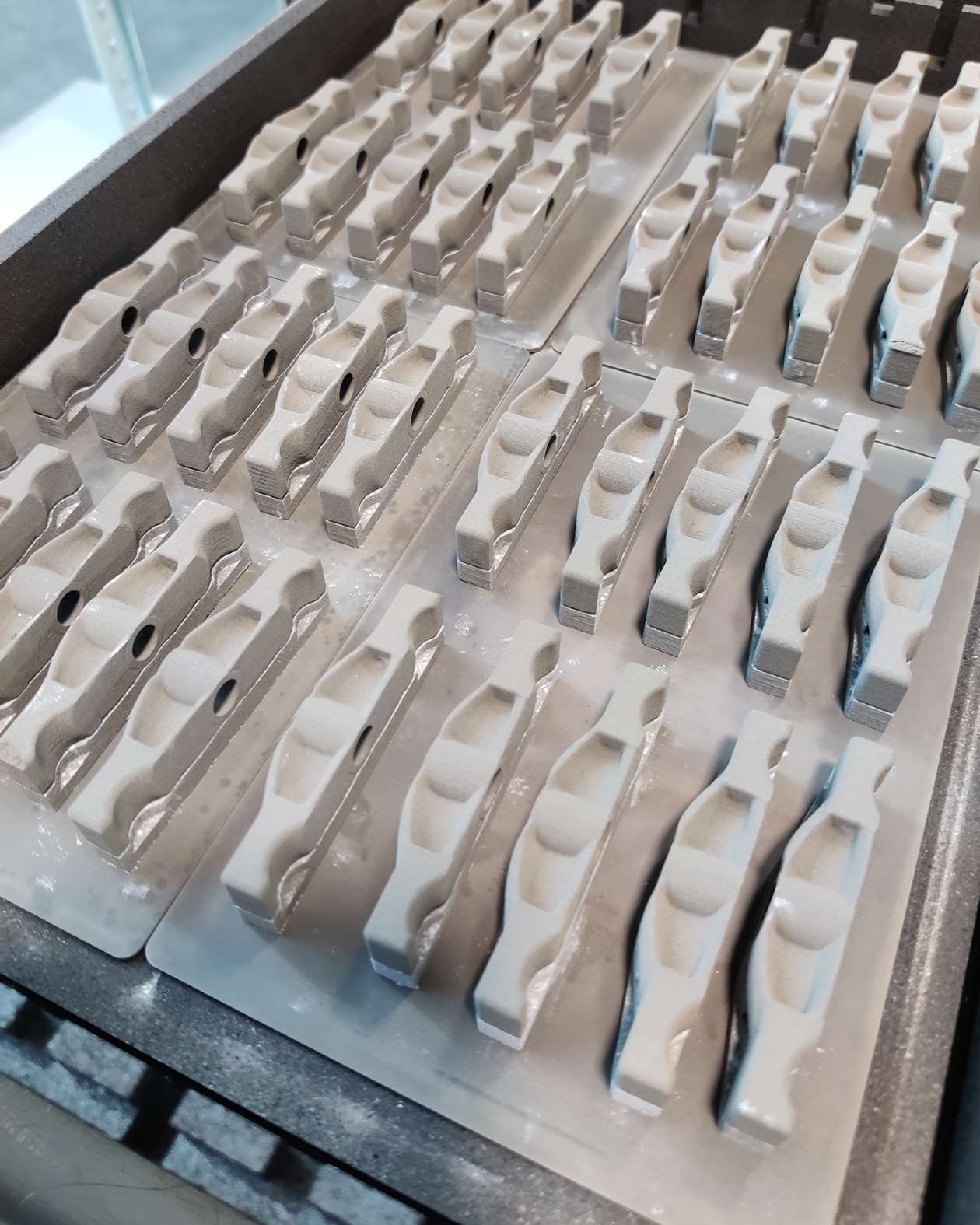
Validated Materials
PureSinter delivers a breakthrough for sintered powder metal applications with the ability to process a variety of metals and binders. This material flexibility makes the furnace a fit for a variety of industries.
TiTested™ for purity
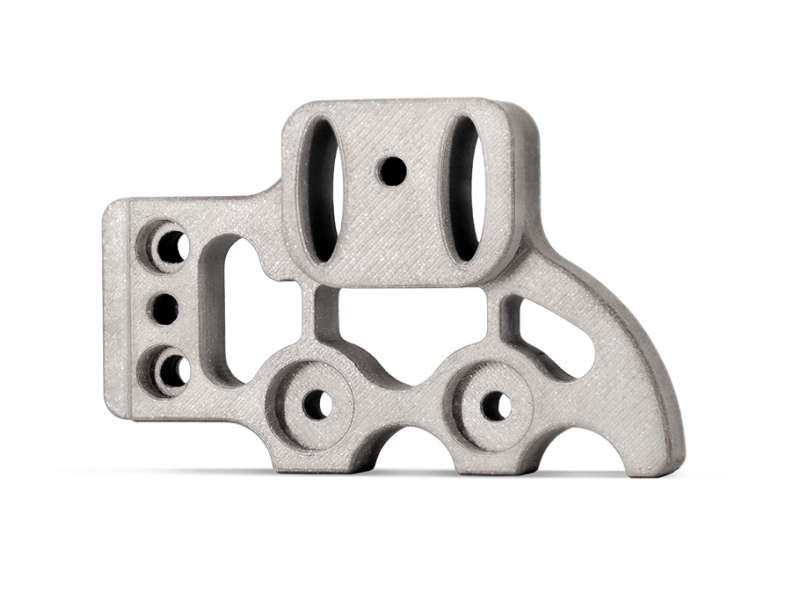
Reactive materials are challenging to sinter, traditionally requiring expensive vacuum pumps, gas purifiers, and burnout cycles. PureSinter has sintered titanium to 98% density with properties that meet or exceed ASTM F2885 standards for HIPed PM Ti6Al4V material while using a much smaller energy footprint than conventional sintering furnaces.
Additive and traditional parts
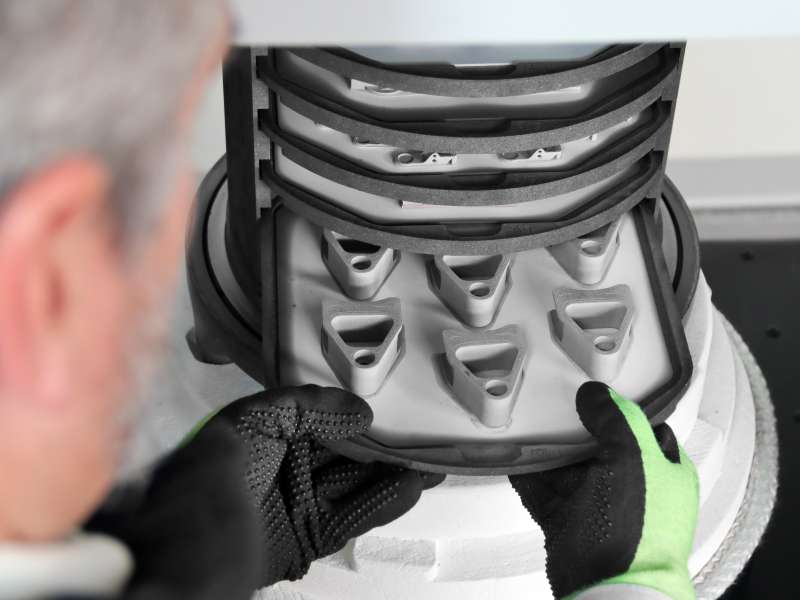
PureSinter is compatible with parts 3D printed with Bound Metal Deposition (BMD) or binder jet additive manufacturing (BJT) processes, as well as traditional Metal Injection Molding (MIM) or Press and Sinter (PM) manufacturing methods. The furnace comes pre-loaded with our most popular Desktop Metal materials, and will be added regularly via over-the-air updates. For new or custom profile creation, use the optional Sinter Cycle Generator with an easy-to-use interface for ramp rate, hold time, temperature, and cooling parameters.
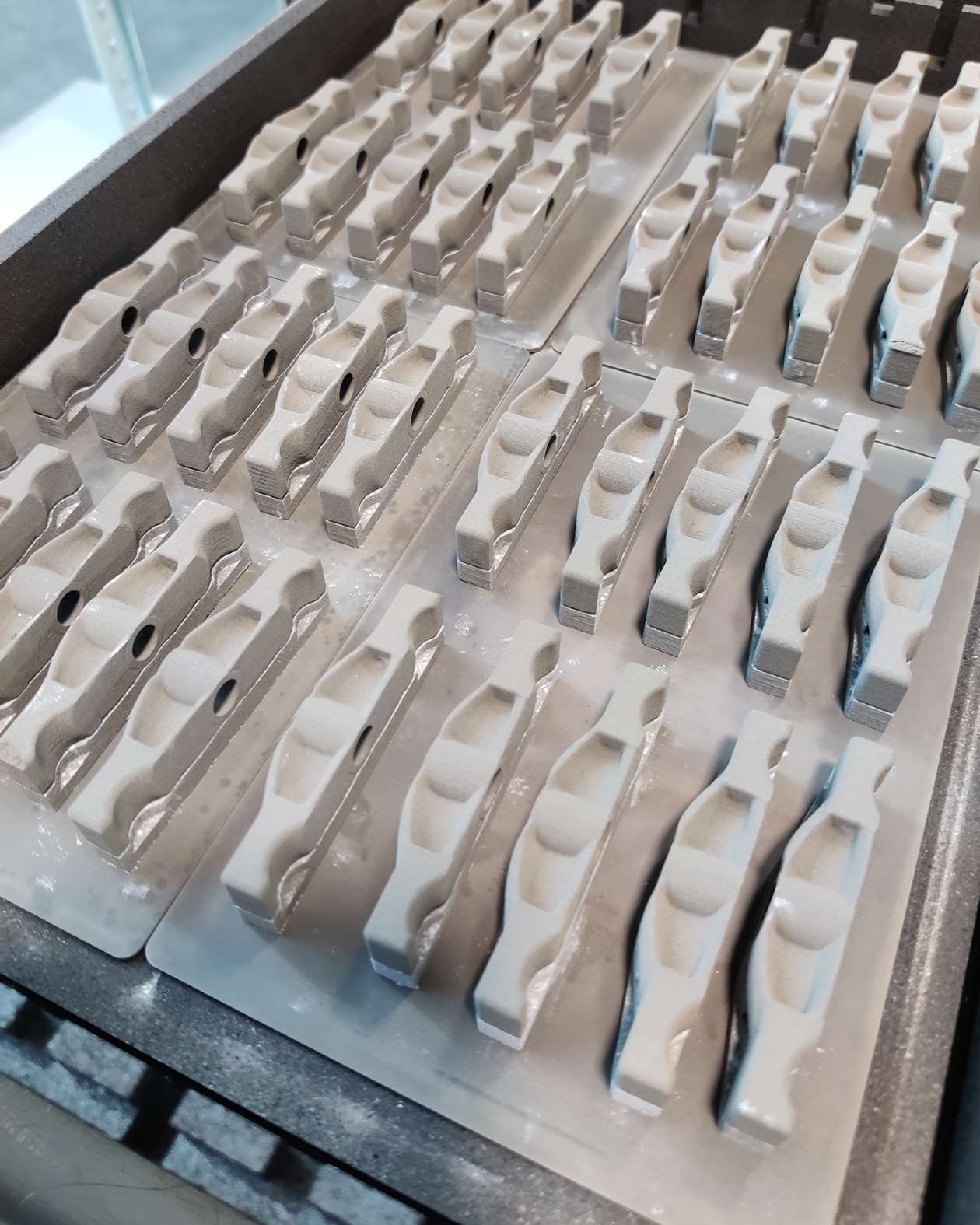
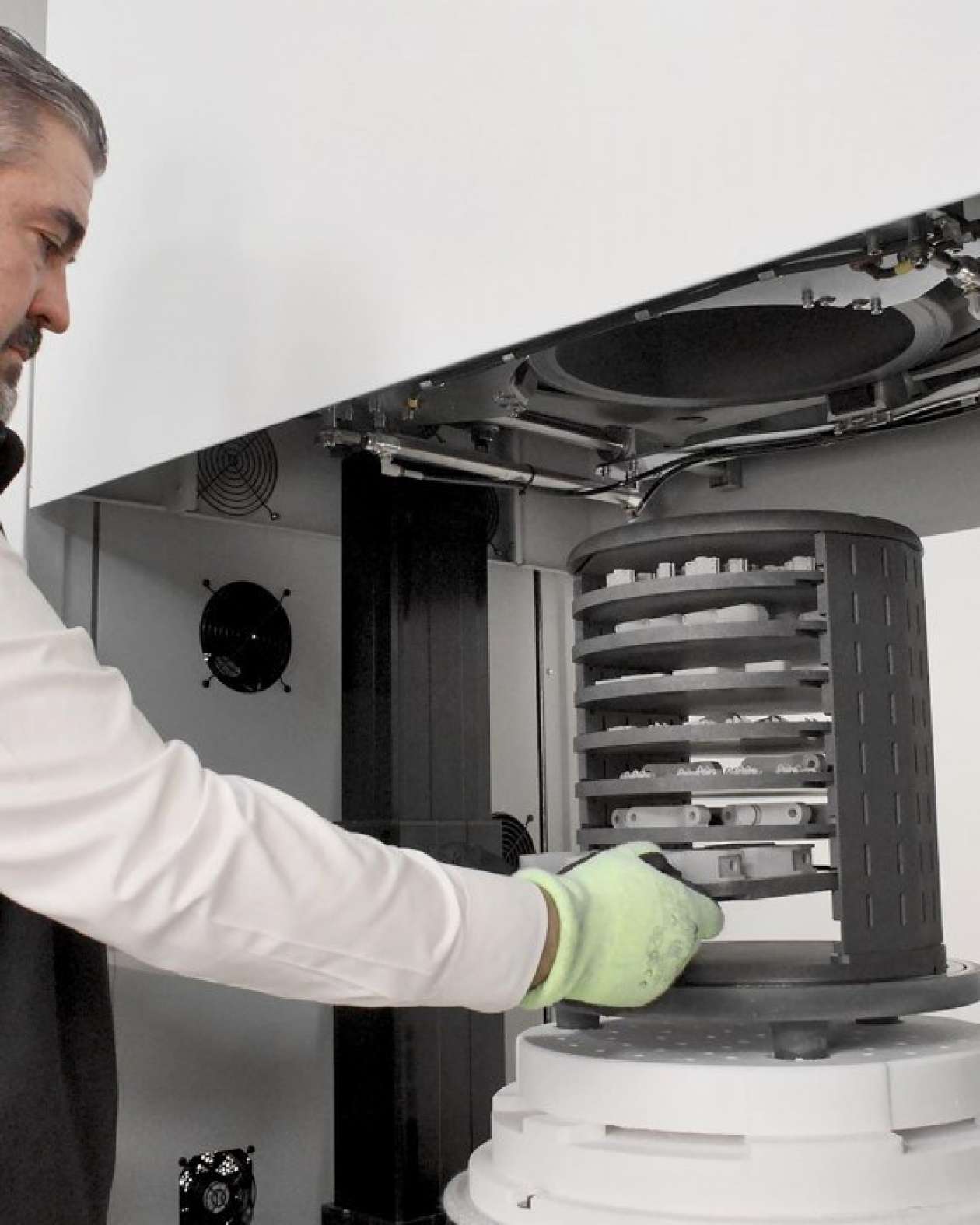
User-friendly Concept
The PureSinter furnace was designed for ease-of-use to make sintering successful for a variety of users and applications. Traditional industrial furnaces are expensive to acquire, operate, and maintain with a lack of efficiency that contributes to high throughput times and operational costs.
Developed with safety and maintenance in mind
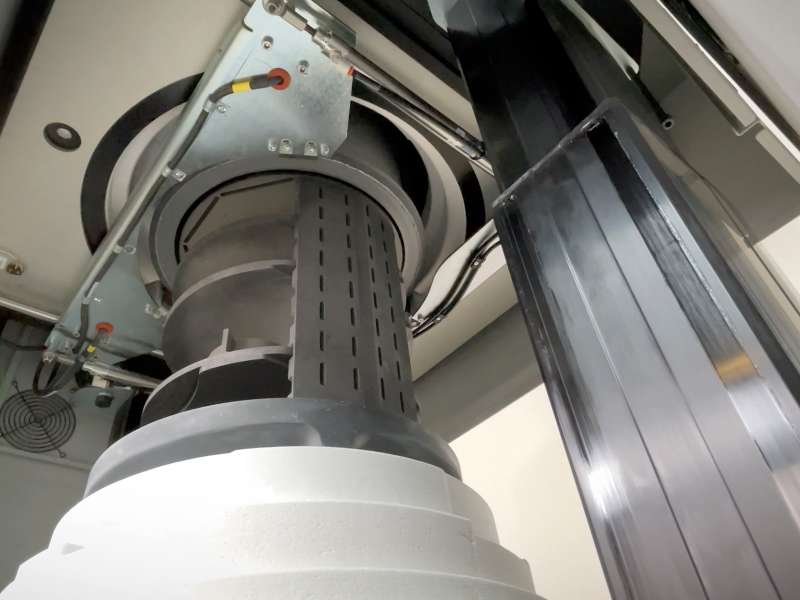
The innovative design of PureSinter delivers a clean, more predictable processing environment. We eliminated dozens of the joint and valve leak points of traditional furnaces and leak tested our high-purity seal. The high-efficiency design of PureSinter lowers operating costs and dramatically lowers energy usage. Utilizing rapid air cooling instead of the traditional water-cooled walls and recirculating blowers reduces facility requirements — while other industrial furnaces require more than 30 gallons-per-minute (GPM) of water, with PureSinter no incoming water line is required, nor is there any need for closed-loop spot coolers or chillers.
Graphite Shelving
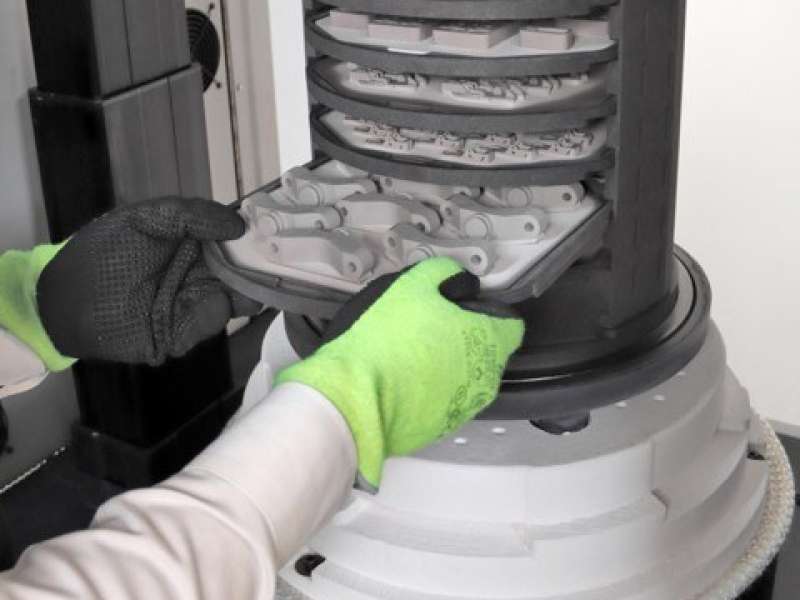
The “click into place” horizontal shelving system of PureSinter is made of high-purity graphite. With access from front and back, the shelving ensures optimum ergonomics.
Efficient Cooling
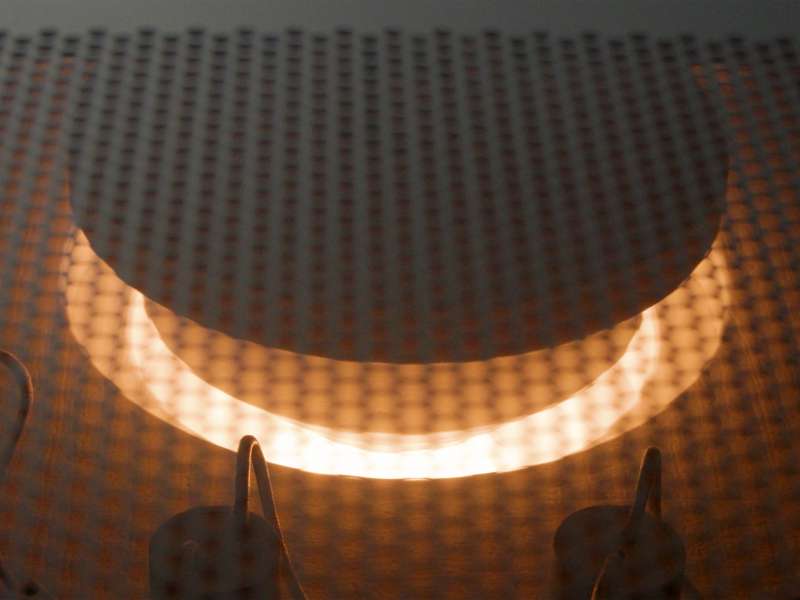
Active, rapid cooling of PureSinter is enabled in a closed-loop controlled cooling process utilizing energy-efficient fans and a pop-out vent in the insulation pack roof. The air flow paths have been optimized to maximize cooling rates and minimize thermal gradients. Because we’re cooling outside of the Vacuum Retort, the high-flow cooling gas is simply air and does not interact with the sintering run or the parts themselves. This also means that PureSinter does not require high inert gas flow and/or a recirculating blower that is required with many traditional furnaces.
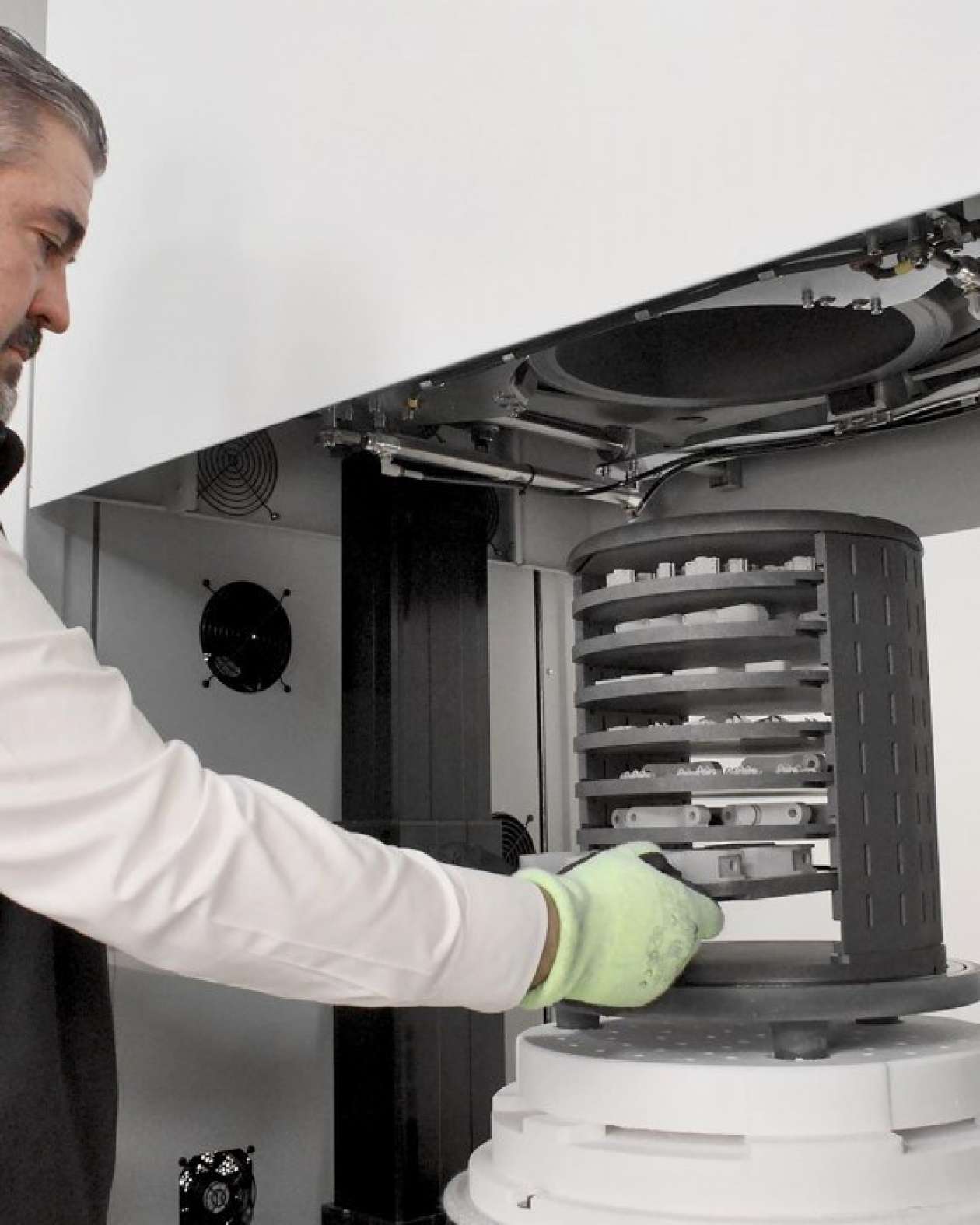
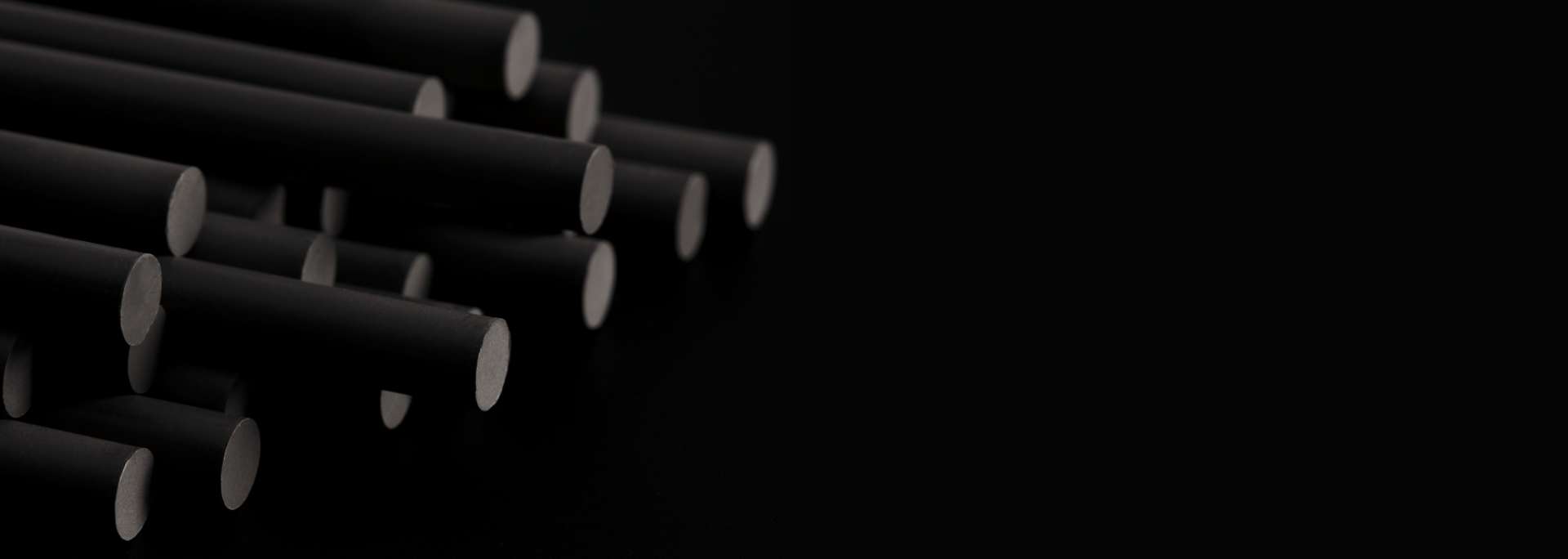
1 More information on pre-programmed parameters by material and machine is available in the brochure
2 Additional details to software trial may apply.