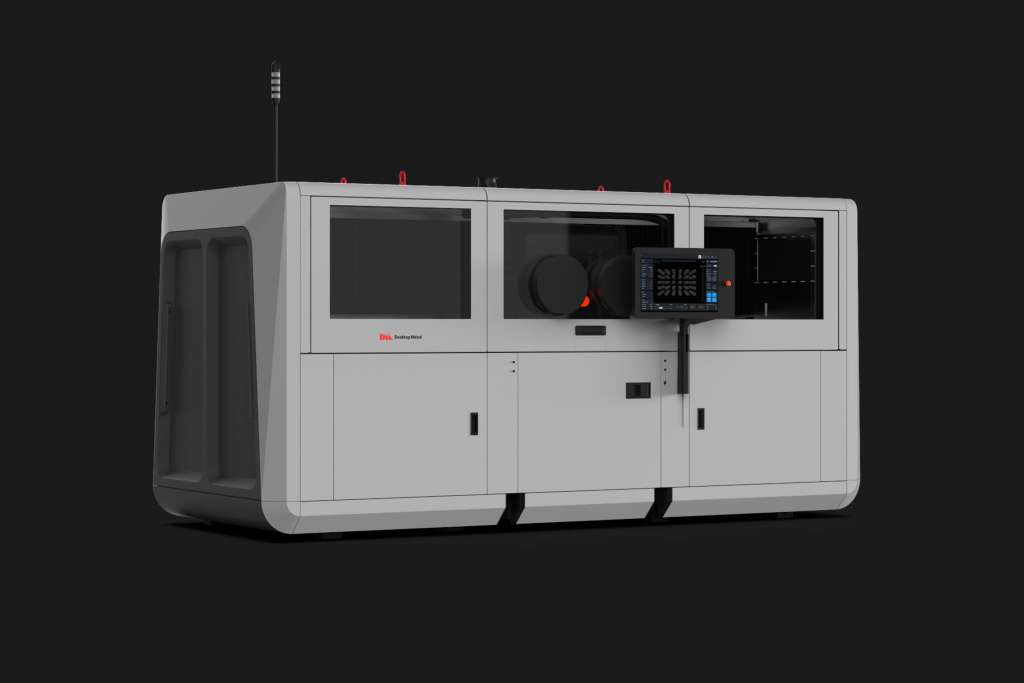
Videos
-
-
Introduction to the Production System P-50
As one of the most highly anticipated additive manufacturing systems ever introduced, the P-50 is the product of nearly $100 million in investment and a four-year development program overseen by Desktop Metal engineers and materials scientists.
-
Highlights from 2023 P-50 Open House Event
Watch highlights for our first P-50 Open House event where 50 guests from across the country came to learn more about the Desktop Metal Production System P-50, a landmark metal binder jet system offering ultra-fast metal printing and industry-leading low metal parts costs from a 3D printer.
-
TriTech Titanium Parts LLC discusses binder jetting Ti64 on Production System™ P-1
Binder jetting of Ti64 simplifies production of complex titanium parts, which can be challenging and expensive to fabricate using traditional manufacturing methods. Production System P-1 customers interested in working with titanium should consult their Desktop Metal sales representative on hardware and binder requirements.
-
-
-
Metal 3D Printed Parts from the Desktop Metal Studio System
What can you print with office-friendly Bound Metal Deposition from Desktop Metal? From food processing equipment to oil and gas components, the Studio System is helping manufacturers across industries revolutionize their products.
-
Studio System: An end-to-end solution for metal 3D printing
Designed as an end-to-end solution, the Studio System is the first to deliver office-friendly metal 3D printing.
-
Customer Story: Azoth uses office-friendly Studio System to deliver precision metal components
Azoth in Ann Arbor, Michigan, started their additive manufacturing journey with the Desktop Metal Studio System™. The company still uses the office-friendly Studio System today for one-off and short run volume production of metal components.
-
-
-
AmPd Labs Adopts Metal 3D Printing with Live Sinter™
The sintering process to densify binder jet 3D printed parts can cause shrinkage and distortion. Live Sinter advanced simulation software from Desktop Metal predicts and corrects errors when sintering this fork mechanism. Previously a 7-piece assembly, AmPd Labs consolidated the design to 3D print the gaming equipment component as one stainless steel part.
-
Live Suite™: Software package to seamlessly manage your 3D printers, accessories, and processes
Live Suite is a package of premium software applications with all-new functionality for users of our Additive Manufacturing 2.0 systems that integrates software across our Team DM brands into one easy-to-use cloud-based suite.
-
Live Monitor™: Access system status and statistics from any web browser, anyplace, anytime
Live Monitor™ provides real-time information about Desktop Metal 3D printers* and furnaces that is actionable, traceable, and helps to improve efficiency and print results.
-
-
-
Customer Story: 3D Energy Digitizes Inventories with the Desktop Metal X-Series
Binder jetting provided an opportunity to produce a labyrinth cage, a critical valve application, faster and more optimized than with traditional brazing methods. Metal 3D printing allows companies to operate more efficiently with digital inventory strategies.
-
Azoth Customer Story: Production-Qualified Binder Jet Metal 3D Printing
Azoth in Ann Arbor, Michigan, focuses on sinter-based additive manufacturing to enable mass production. The company uses the Desktop Metal Shop System for high volume binder jet 3D printing of end-use metal parts. Customers utilize its Take One Make One digital inventory and establish Production Part Approval Process for 3D printed metal parts.
-
DSB Technologies Drives Metal Binder Jetting into Production with Desktop Metal X-Series Lineup
DSB has adopted Desktop Metal’s complete X-Series metal binder jetting lineup at its Wisconsin headquarters, which processes more than eight million pounds of powder into parts annually with both traditional and additive technologies. DSB is now developing and delivering customer parts, scaling from development to serial production with the InnoventX, X25Pro, and X160Pro for a range of metals, including 316L and 17-4 PH stainless steels, 4140 low-alloy steel, and M2 tool steel.
-
-
-
Easy material changes with the Studio System
In this video, Matt Barbati walks through how to change materials in the Studio System metal 3D printer.
-
Hot-swappable media cartridges
In this video, Matt Barbati discusses the cartridge design and how it supports a seamless workflow for in-house metal 3D printing.
-
Separable Supports™ for easy post-processing
In this video, Dave Belanger explains the advanced, auto-generated support structures designed to simplify post-processing for metal 3D printed parts.
-