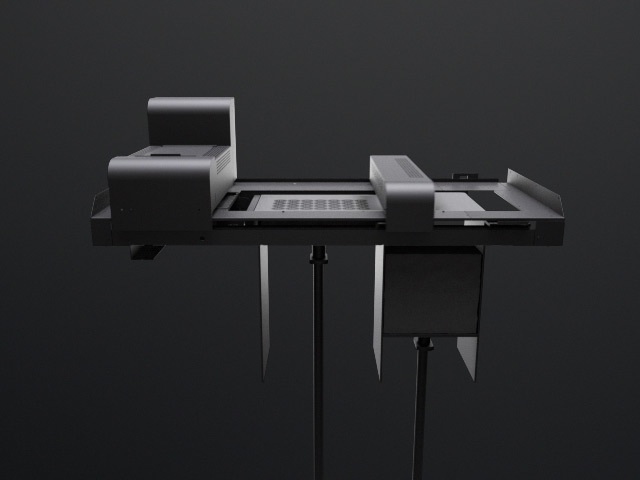
The Shop System: The Benefits of Binder Jetting
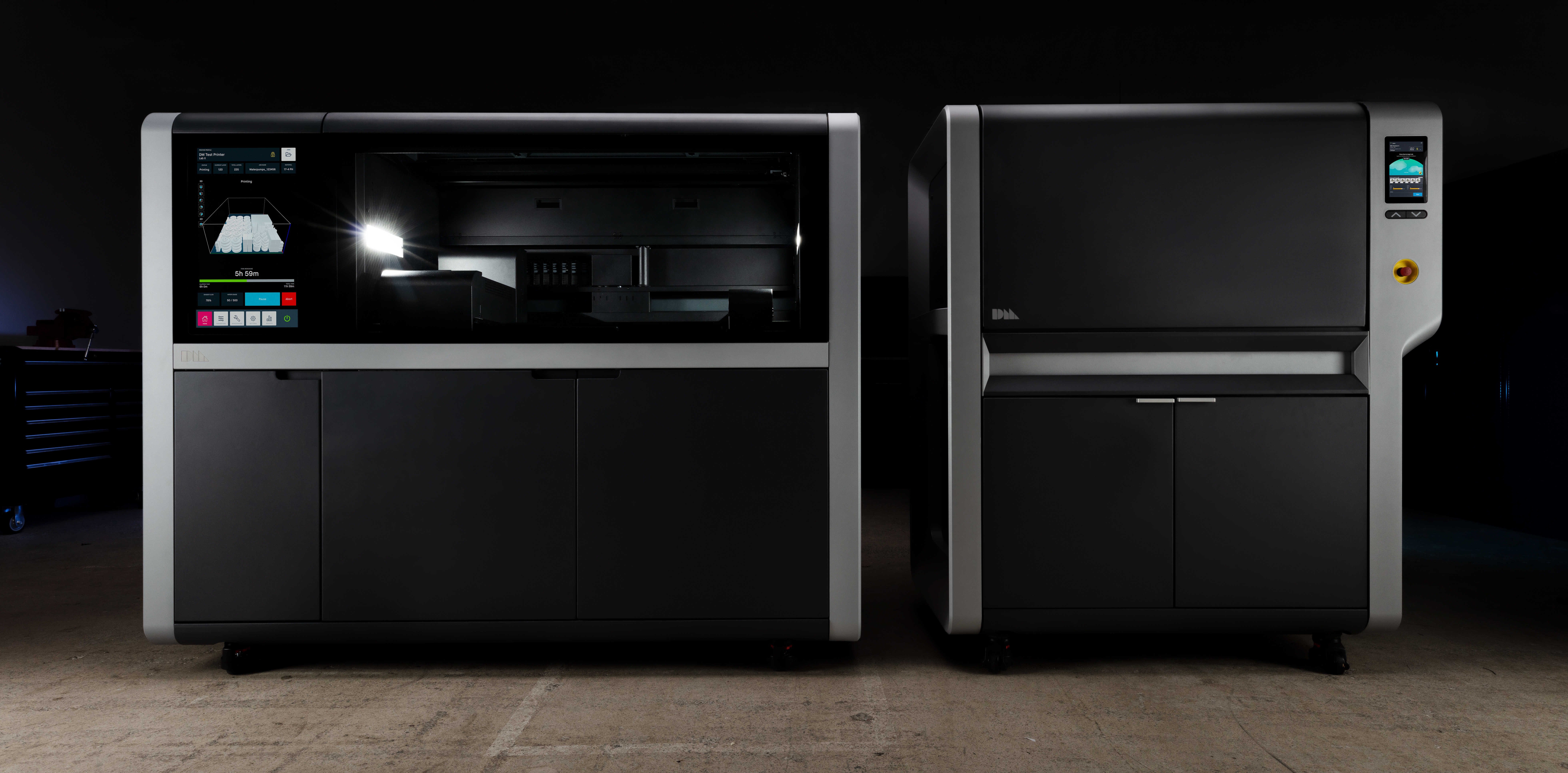
The world’s first metal binder jetting system designed for machine shops, the Shop System is capable of printing complex metal parts with the benefits that standards machine shops expect: unparalleled productivity with superior print quality while maintaining high levels of accessibility throughout the entire process.
The binder jetting technology at the heart of the Shop System offers a host of advantages for manufacturers, spanning both process and product innovations.
Process Innovations
Like other 3D printing methods, binder jetting requires no tooling, meaning parts can often be produced faster and more affordably than traditional manufacturing processes. But unlike legacy metal 3D printing technologies like DMLS, SLS, SLM, and EBM, Binder Jetting allows for these parts to be produced in high volumes. As soon as designs are finalized, printing can begin, and hundreds of parts can be printed overnight, as opposed to waiting weeks for the fabrication of hard tooling common with traditional manufacturing methods like MIM, casting, forging, extrusion, and high volume machining.
Since fabrication is not tied to a particular tool, binder jetting significantly simplifies the process of changing a design - simply update the CAD file and send the new designs to the printer. That ability to update designs as needed enables unprecedented design freedom and allows for the development of products with improved performance and specialized designs that can be customized to meet end-users’ exact needs.
This tooling-free manufacturing process leads to a very agile manufacturing environment, often resulting in reduced warehousing and inventory needs. Manufacturers simply print the parts quickly when they need them, and no longer need to store old tools indefinitely on the off chance they may be needed, but can instead create “digital warehouses” to store part files and call them up for printing when needed.
Process Innovation Example:
Cosmetic Ornament
The complex designs and organic shapes found in jewelry make it an excellent application for metal 3D printing as they are often difficult to produce via traditional manufacturing methods. Investment casting would require significant expenditure in tooling, and would lock designers into a single design early in the process. When different sizes are needed (rings, bracelets, etc) new tooling is required for each size, dramatically increasing part costs and logistical hurdles.
Metal 3D printing solves these challenges. The additive nature of printing allows for complex geometries to be produced efficiently and affordably in a variety of sizes. Printing does not require any tooling, allowing for different sizes and designs to be manufactured easily; simply modify your CAD model and start printing almost immediately.
Ornaments can bring cosmetic products to the next level, setting them apart with unique design features to signify brand and prestige. This ornament features a ball that is encapsulated in the center of the outer casing, a design that would be impossible to produce with traditional manufacturing techniques but which the Shop System can produce with ease. The Shop System allows for this part to be mass-produced thanks to the low cost per part and high throughput.
Product Innovations
To ensure parts can be produced efficiently and affordably, traditional manufacturing design often comes with restrictions intended to enable ease of manufacturing. Such restrictions are necessary to ensure part success, economics, and throughput for subtractive methods like machining and hard tooling-based manufacturing methods like MIM and casting.
A prime example of the restrictions traditional manufacturing faces is in machined parts. Though designers may want to add new features to parts, doing so translates into increased machining time, and often results in significant cost increases. Other traditional manufacturing methods - like MIM, casting or forging - face similar challenges; new features mean significant increases in tooling complexity and costs, and may even make parts impossible to produce. By restricting the features a part can utilize, manufacturers wind up with designs that, while easy to produce, often make sacrifices in part performance.
Unlike these traditional manufacturing processes, 3D printing is an additive process, building parts up layer by layer. This allows for the creation of many features - like organic shapes, undercuts, noncircular holes, consolidated assemblies, and lightweighting features like lattices - that otherwise aren’t possible or cannot be justified due to manufacturing difficulty and cost with traditional methods.
Those features can be seamlessly integrated into binder jet parts, and often reduce the cost of producing the components. Lightweighting features, for example, remove material, reducing the cost of printed components, but almost always increase the cost of a traditionally-manufactured part due to the increased number of cuts for machining or tool complexity for MIM and casting.
Product Innovation Part Example:
Sensor Holder
This part is used to hold sensors in place as they take constant measurements of a rotating component. Keeping the weight as low as possible was essential for this component to ensure it did not add any additional weight to the rotating motor. By printing on the Shop System, this part was able to be optimized with six thin flanges, significantly reducing both the mass and footprint when compared to a machined component. With printing, gyroid infill was incorporated through the entire part, further reducing the weight while maintaining stiffness and strength. The speed and low per-part cost of the Shop System allow for this optimized design to be produced affordably in volume for the end-use application.
Additive manufacturing also enables assembly consolidation, the combining of multiple parts into fewer, multi-functional assemblies. Traditionally, those assemblies have been created from relatively simple parts, which can be manufactured far more efficiently and affordably than a single, complex part. Those simple components are then combined with welding, screws, rivets, and other fasteners. As an additive process, binder jetting makes it easy to combine all the components of an assembly into a single printed part, which is often more affordable to produce than the separate components. These consolidated assemblies can greatly simplify logistics by reducing the number of parts in the BOM that need to be sourced, warehoused, assembled, etc
*Costing and Throughput for 16L Shop System without Setters
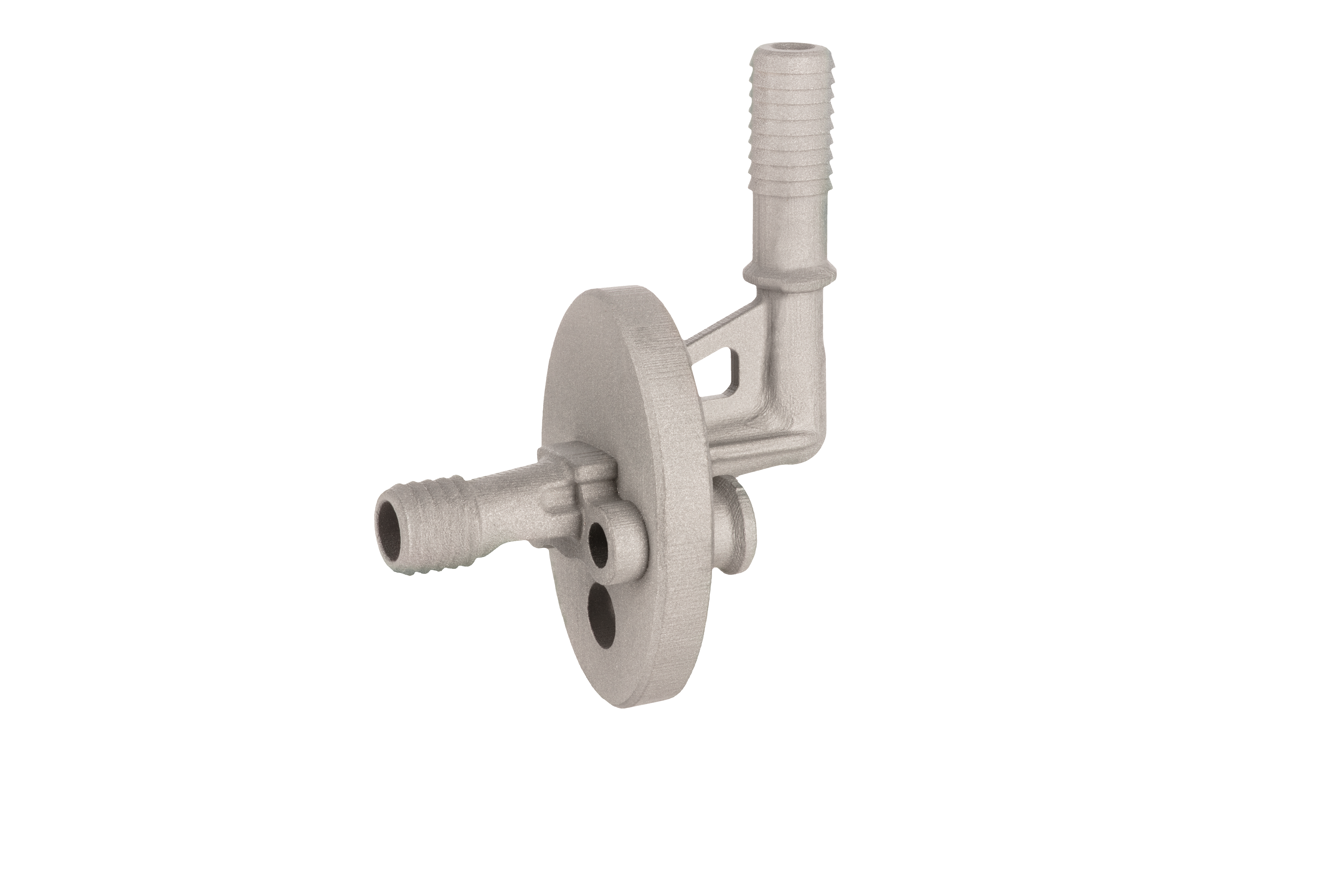
Product innovation example:
Connector
This fluid connector features complex geometry, including internal channels, that would require it to be produced as a multi-part assembly, rather than a single component.
Printing, however, made it easy to produce this component as a single part, and also resulted in higher performance than the traditionally-manufactured alternative, while simultaneously reducing part cost and manufacturing lead time.
A host of other features - like lattices, generative design, and internal channels - that would be impossible to create with traditional manufacturing methods can easily be 3D printed. Because it produces parts layer by layer, binder jetting makes it easy to incorporate those features into parts, bringing designs to the next level and increasing part performance (strength, stiffness, cooling rate, minimizing footprint,) lowering weight, and reducing part costs.
While it has been possible to incorporate those features into printed parts for some time via powder bed fusion, most applications were generally too expensive to justify printing in anything other than very low quantities. With the emergence of new binder jetting systems with new levels of ease of use and lower part costs like the Desktop Metal Shop System, it is now possible to produce these parts in higher volumes at lower part costs, greatly lowering the hurdle to justifying 3D-printed metal parts. For the first time, it is possible to go to mass market with metal 3D printed components.
Explore the Series
-
The Shop System: Breakthrough Performance
The second of a three-part series examining the benefits, performance and cost savings that come with the Shop System. -
The Shop System: Reduce Costs, Increase Revenue
The third of a three-part series examining the benefits, performance and cost savings that come with the Shop System.