We are Team DM. We exist to deliver Additive Manufacturing AM 2.0 technologies, materials, and applications that enable mass production.
Platforms
_Case Studies
Unique and Highly Customized Luxury Watch Components Thanks to Metal Binder Jetting
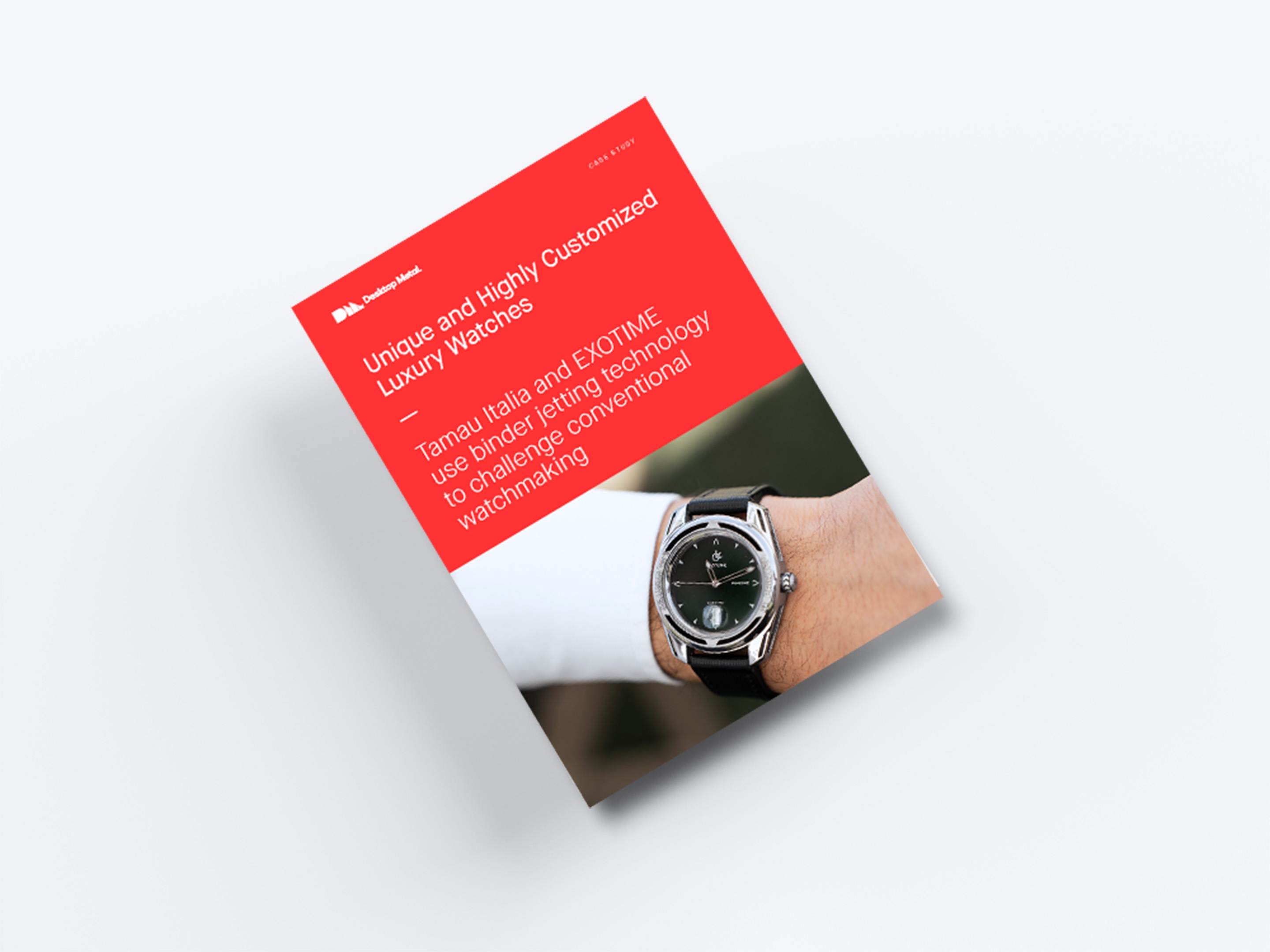