SPJ feature Spotlight: Real-time Print Inspection
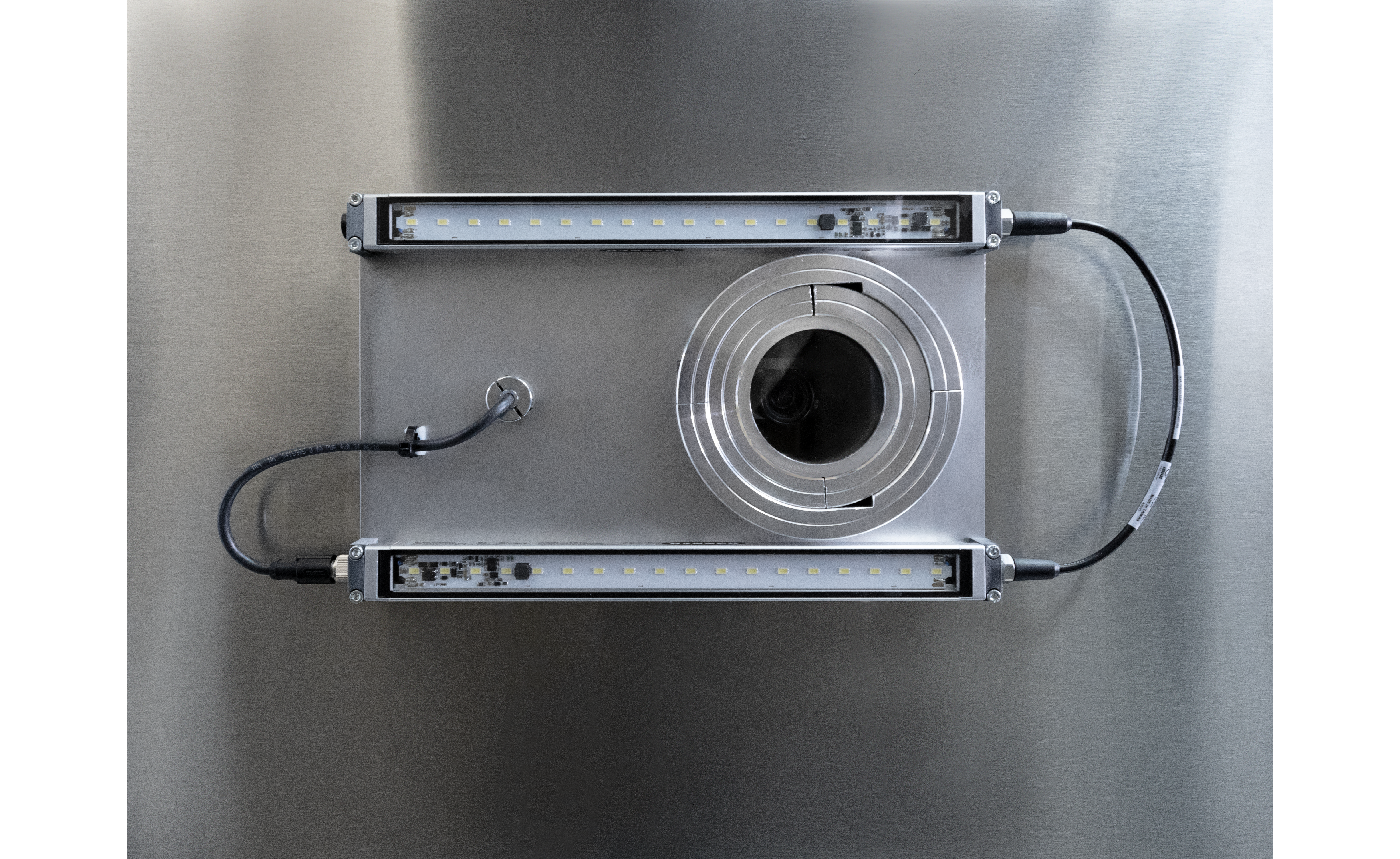
What is Real-time Print Inspection?
The real-time print inspection feature for the Desktop Metal Production System uses an industrial inspection camera, along with a variety of machine vision and machine learning techniques to identify potential print quality issues, defects, and process settings that can improve part quality, yield, or efficiency.
How it works
During each pass of the print head, the system uses a high-resolution industrial inspection camera to capture multiple images of the print bed under various lighting conditions. Those images are then processed in real-time. If any defects are identified, the system notifies the user.
Why it matters
Detecting and correcting potential problems early improves the chances that a part will survive the printing process without defects. In some cases, simply knowing a part may be defective can provide valuable information. By flagging a part as defective, users can begin reprinting the part immediately, saving a day or more of turnaround time, especially on low-volume prints.
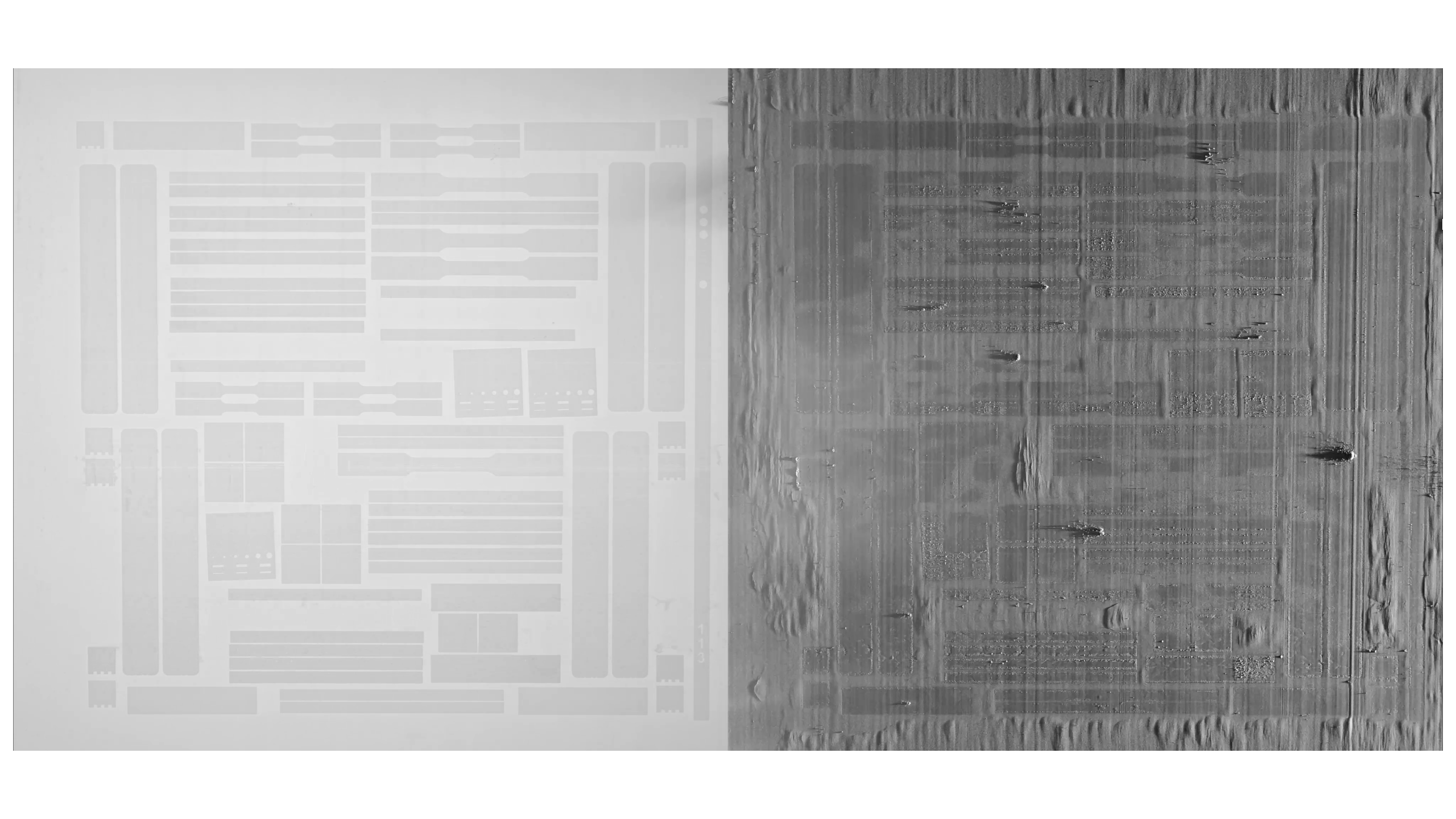
Result on process/parts
The print inspection system can influence part quality and identify issues that can improve the processes at various stages of the printing process.
During print
Real-time inspection identifies groups of misfiring jets and triggers a cleaning sequence as needed. Early identification of misfiring jets reduces the likelihood that part quality is affected. This also saves time and consumables by reducing the frequency of printer cleaning cycles.
Real-time inspection identifies defects that could be caused by suboptimal process parameters, and recommends process tweaks that may improve print bed quality. This gives a user more information, and allows for process improvement in real time, resulting in better overall quality in current and future prints.
Post-print
Within minutes of print completion, the system provides users a video for quick inspection of the print, as well as high resolution images of each layer if closer inspection is warranted. Both video and still images can be accessed via local network or USB.
To help identify trends over time, the system provides an overall summary of part and build health.
Depowdering
The system transfers model and defect information to the depowder station, allowing users to visualize the parts in the powderbed and flag any potentially defective parts. By knowing the location of potentially problematic parts, the user can more efficiently depowder printbeds and quickly inspect parts.
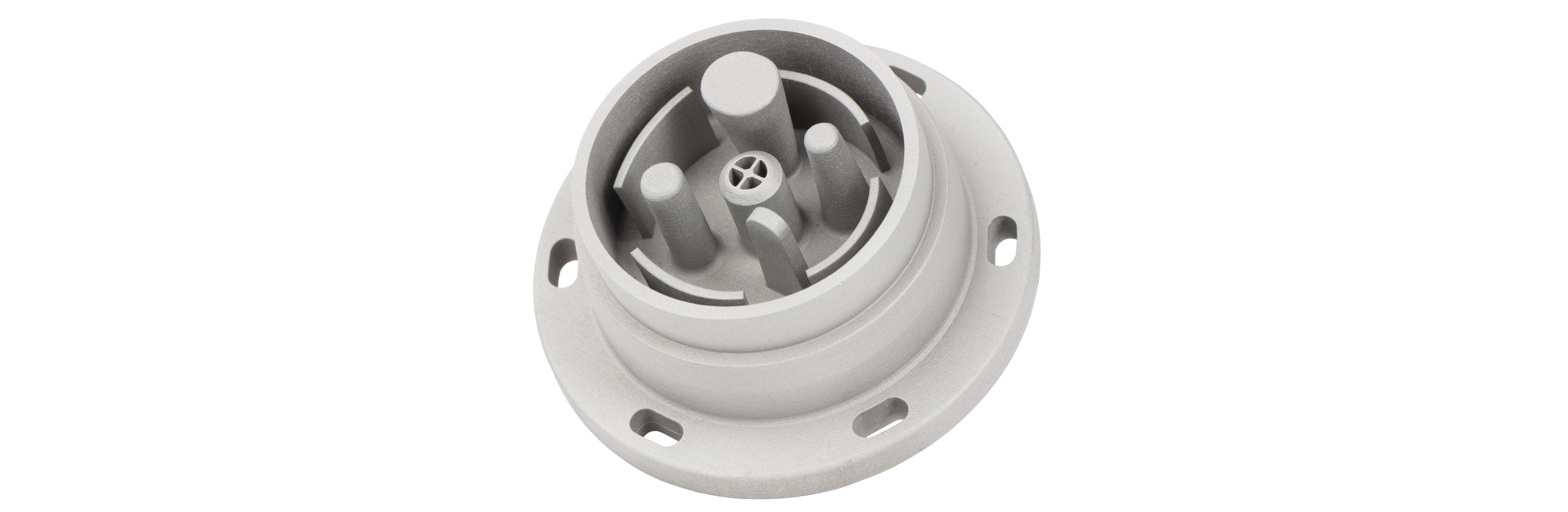