Metal 3D printing for service bureaus and machine shops
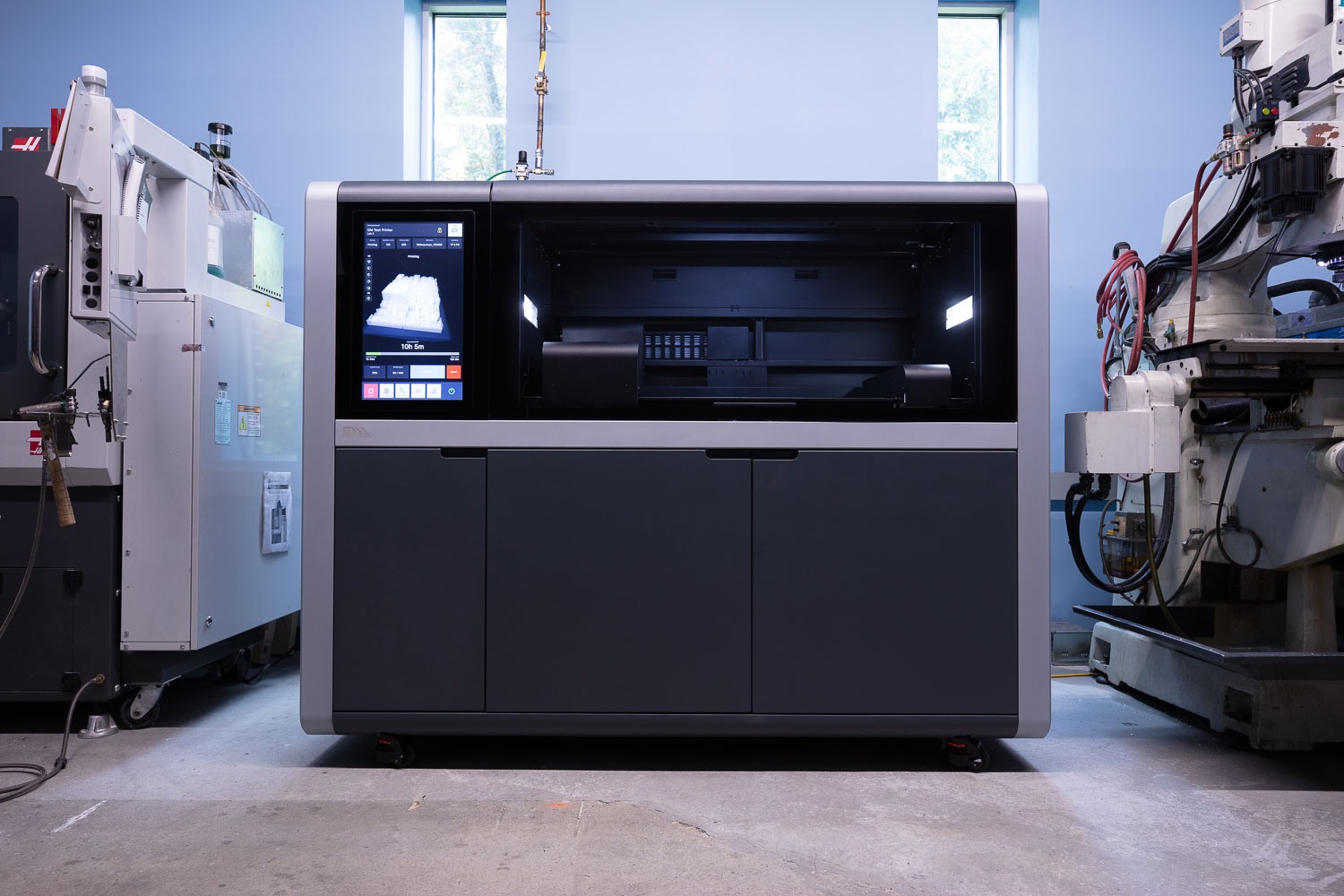
Service Bureaus
Encompassing everything from companies offering quick-turn prototyping to machine shops to injection molding firms, service bureaus play a key role in the manufacturing ecosystem. They produce a wide range of parts, including one-off functional prototypes and low- to mid-volume production runs.
The Challenge
Many customers rely on service bureaus to produce parts they can’t make internally because they may not have their equipment, capacity or time. To meet customer’s needs often means traditional manufacturing methods which require tooling, complex fixturing or multiple machining setups are often impractical due to long lead times and high cost.
Customers also turn to service bureaus as a way to explore new manufacturing technologies before making large-scale investments. Prior to rolling out new manufacturing methods, companies often look to service bureaus for benchmarking and prototyping, so having access to innovative technology can help them win bids, attract new customers and expand accounts.
In cases where custom tooling is needed, shops must produce those tools as quickly and affordably as possible to meet customers’s needs, then store and track those tools if replacement or additional parts might be needed in the future.
The Solution
Additive manufacturing allows service bureaus to extend the benefits of metal 3D printing - such as tooling-free production, assembly consolidation, and new levels of geometric freedom and part complexity - to their customers.
Using binder jetting, service bureaus can create parts directly from a digital CAD file without the need for tooling, allowing them to cost-effectively produce low volume batches of complex parts, simultaneously produce parts with different geometries without the need for multiple setups, and produce hundreds of highly-complex, near-net-shape parts every day without the constant oversight of a skilled machinist.
By lowering setup and part costs, metal 3D printing can change the part-cost equation for service bureaus, enabling them to win new business, including small or medium jobs that might previously have been “no bid” due to expensive mold tooling or CNC-setups. The systems also free up CNC capacity for other, more profitable jobs.
For those jobs where tooling is needed, 3D printing in-house can reduce both the lead time and cost to create workholding, jigs, and fixtures to make production workflows more efficient. And since printing is an additive process, increased tool complexity does not lead to increased cost. The end result is more efficient manufacturing and reduced warehousing costs as companies store tools as digital files rather than physical objects.
Bolt Replacement Grippers
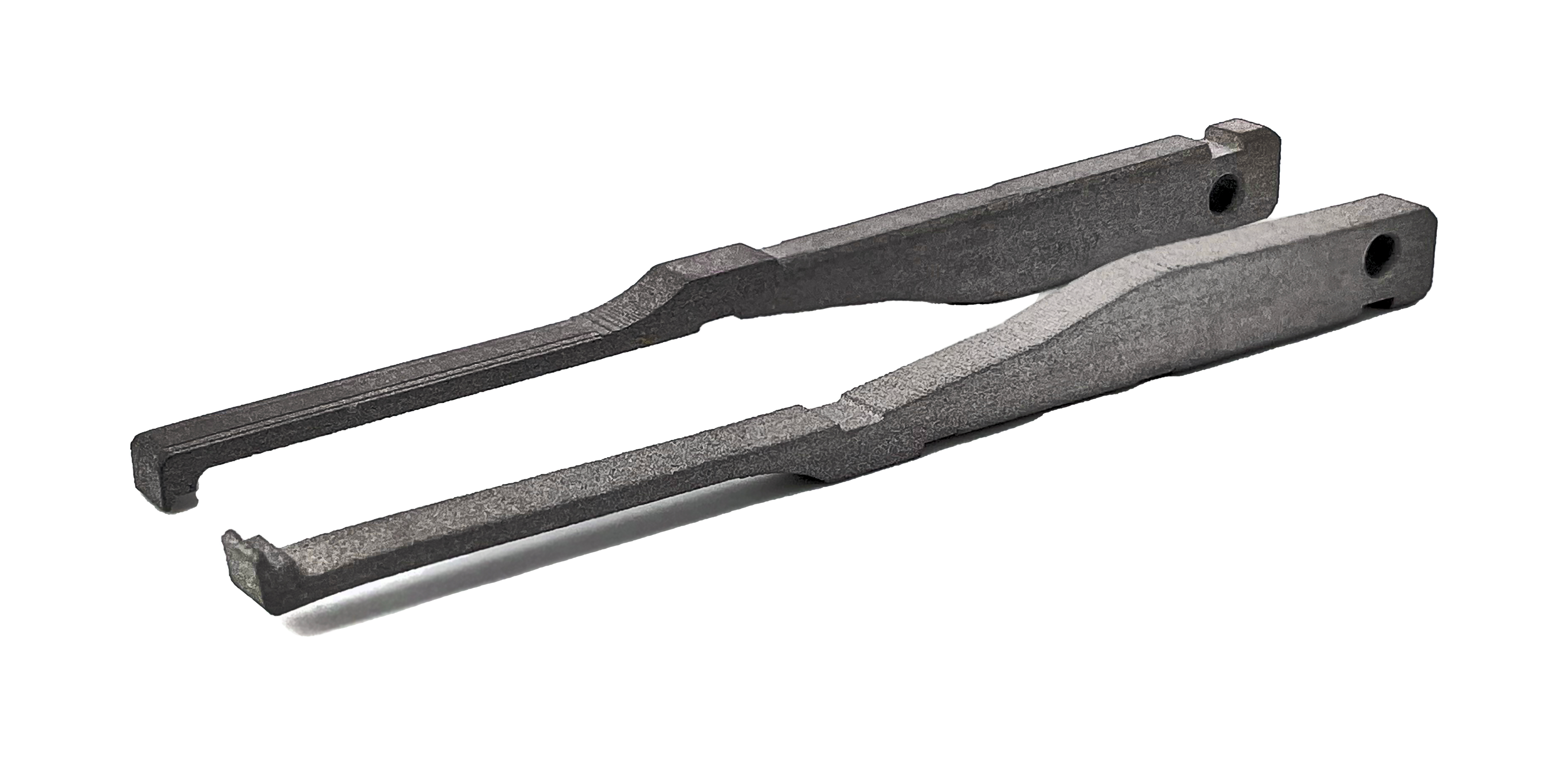
On-demand production with the binder jet 3D printing on the Shop System enables a Take One Make One (TOMO ®) digital inventory strategy at Azoth, a contract manufacturer in Ann Arbor, Michigan, that specializes in delivering precision metal components. With the capability to produce 1400 end-use parts per day, binder jetting is the more cost-effective production method for these grippers, delivering parts with a 10-day turnaround compared to an eight-week lead time.
The 17-4PH stainless steel components are heat treated to H900 to replace the traditionally machined tool steel parts. Watch the on-demand webinar to learn more about Azoth's Take One Make One (TOMO ®) digital inventory strategy.
Gaming Equipment Fork Mechanism
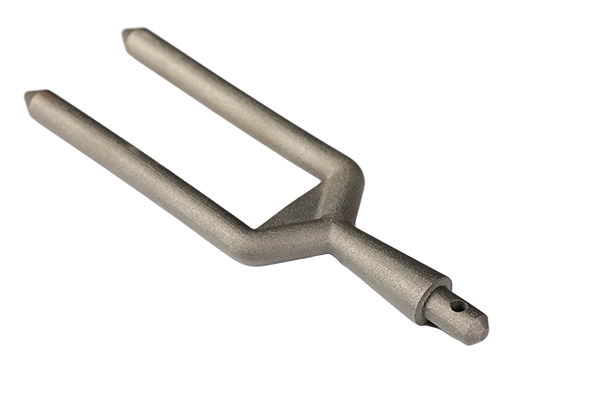
Traditionally a seven-piece assembly, each stamped or machined and screwed together, a customer of AmPd Labs in Houston, Texas was looking to capitalize on the benefits of consolidation for this fork mechanism. Combining components is one of the best ways to be cost effective with benefits including derisked supply chains, stocking fewer part skews, eliminating lost components, reducing assembly time, and improving performance by minimizing potential points of failure of an assembled product.
The consolidated assembly was binder jet 3D printed in 17-4 PH stainless steel on the Shop System as one piece. Eliminating the time and labor needed for an assembly process, as well as on-demand production eased supply chain logistics. Live Sinter™ software played a key role in the success of keeping the long, cylindrical part in tolerance with its sintering simulation and compensation analysis.
Bearing Housing
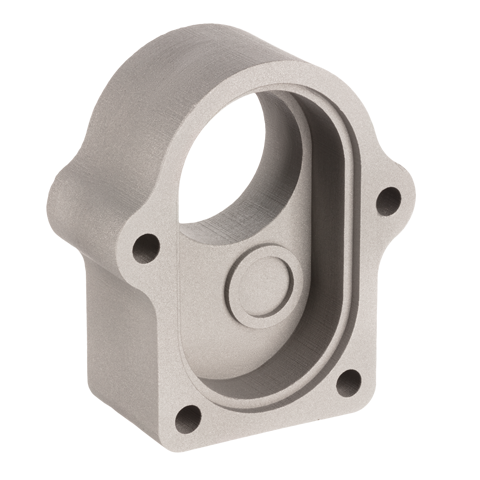
This housing is used to hold pressed-fit bearings in place in a machine. This part needed to be produced quickly out of steel. Using the Shop System, the required 100 housings were printed in just four days and were ready for assembly in less than a week, requiring almost no operator labor.
Printing this housing with binder jetting technology dramatically reduced the manufacturing lead time compared to traditional methods, allowing the service bureau customer to meet their tight deadline and avoid expensive custom tooling setups.
Bearing Inner Race
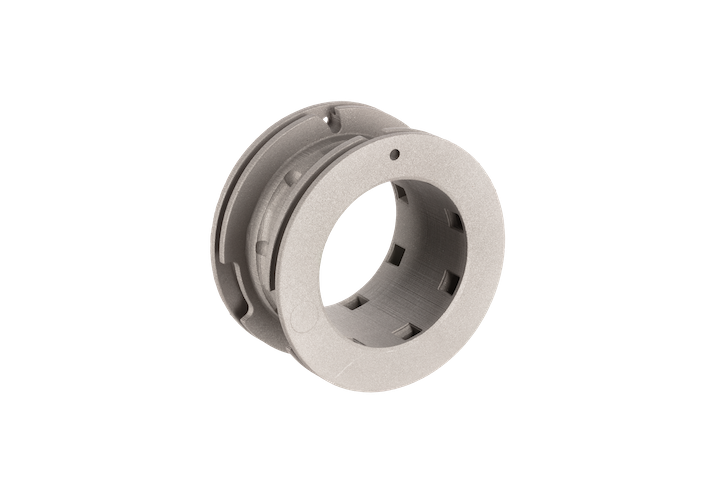
This is the inner race of a custom bearing. The part designer chose to use a service bureau to take advantage of a technology they don’t have in house - Binder Jetting, which can create parts with more complex features at no additional cost.
The internal square fixturing features in this part cannot be machined and would require a collapsible core to be metal injection molded, adding significant cost to the tooling. Similarly, the divots in the bearing race would require surfacing with a ball mill, an expensive and time-consuming machining process.
This part is easily printable on the Shop System, allowing for the production of an optimized design without increasing the part cost. And since no tooling is involved, the design can easily be updated for different sized bearings and printing can start in a few hours, as opposed to waiting days for new tooling.
Custom Bolt
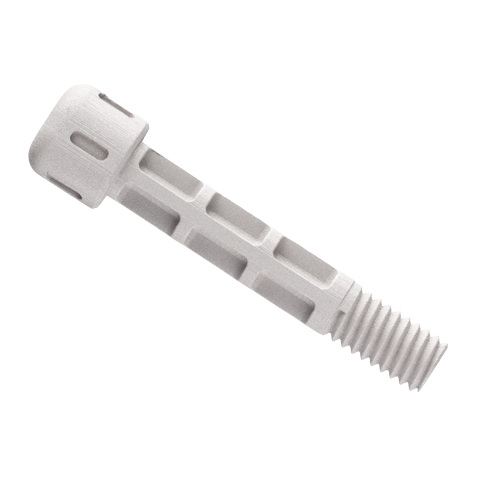
This custom-designed bolt was needed when no off-the-shelf fastener solution would work for a very specific application.
Due to the high cost of hard tooling, most bolts are manufactured in quantities of millions. In this case, however, only a few tens of thousands were needed. By printing on the Shop System™, this bolt can be produced with no tooling, and at dramatically reduced per-part cost. In addition, because no tooling is used, the designer can change the length, thread profile, pitch, and other characteristics of this bolt on demand, by simply altering parameters in the CAD file and starting a new print.