Metal 3D printing for heavy industry
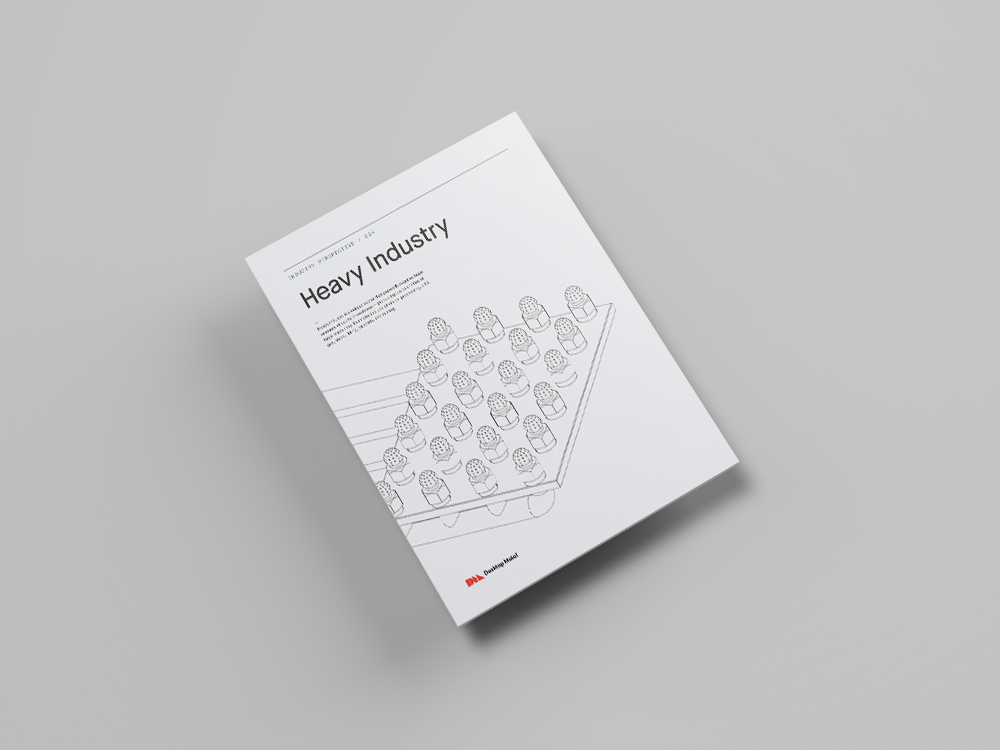
About Heavy Industry
Heavy industry is a unique sector that generally requires huge amounts of capital investment in producing low quantities of large machinery. Examples include chemical processing, oil & gas, shipbuilding, railroads, and mining.
The Challenge
Parts produced for heavy industry are typically manufactured in small numbers and are engineered-to-order for specific applications and customers, making mass production methods - like casting, forging, metal injection molding and others - impractical. Their low volumes also generally result in long lead times and high costs.
Because heavy industry machinery is large and capital intensive, it is expected to have a long service life. This means parts may need to be replaced years after they were first manufactured, forcing companies to track and maintain tooling so parts can be produced on an as-needed basis. The alternative would be to warehouse a large inventory of replacement parts, leading to a host of logistical challenges.
Since so many of the parts used in heavy industry are custom, their fabrication often requires customized fixturing and CNC programming, which add to already long lead times and high non-recurring engineering (NRE) costs. The same is true if a part were outsourced to a foundry for casting.
The Solution
When low numbers of highly-customized parts are needed, eliminating the need for tooling greatly simplifies production. Whether you need to print one or 100 parts, the per-part cost and lead time stay the same. Users simply upload designs to the printer and metal parts are ready to install in just days, streamlining the manufacturing process for a variety of different parts across a variety of part quantities.
Metal 3DP adds significant value when it comes to replacement parts. Rather than keeping a warehouse stocked with extensive tooling and part inventory for whenever a replacement is needed, heavy industry companies can simply create digital warehouses to store files that can be accessed when and where parts are needed. This dramatically reduces the costs and manufacturing lead time for replacement parts.
When tooling is required to fabricate parts via traditional methods, it leads to a significant increase in the part cost and lead time. For example, custom fixturing for CNC machining must be designed and fabricated by a highly-skilled, dedicated operator before the machining of the actual part can begin.
With metal additive manufacturing, however, users can simply export their CAD data, upload it to the printer, and with a few button pushes, their final part can be ready in just a few days. The process significantly reduces operator burden, manufacturing lead time, and part cost, all while avoiding long foundry lead times and machine shop bottlenecks, greatly accelerating manufacturing efficiency.
Master Drilling Gear
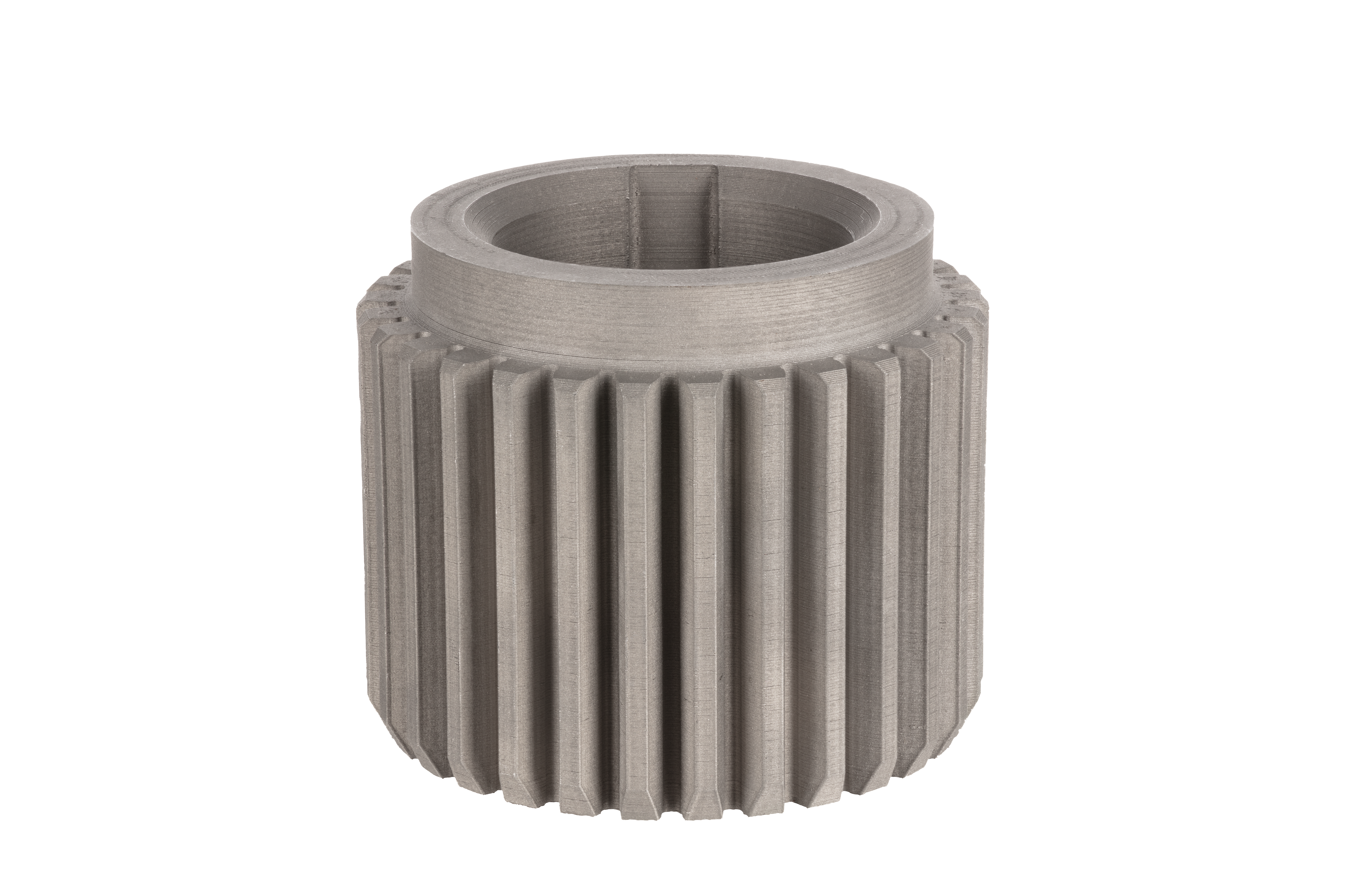
When a problem forced Master Drilling to replace the sun gear in a gear set, engineers tried to source the part from a foundry in China, and were told the job would take three months to complete - an unacceptable delay for the company, which needed the drill back up and running quickly.
With the Studio System the gear was printed, debound, sintered, post machined, and case hardened in just 3 weeks. Utilizing heat treatment of the gear they were able to raise the hardness up to 43 HRC, which was later raised to 64 HRC through plasma nitriding. Master Drilling was able to reduce the lead time from 3 months to 3 weeks, and put the drill back into service far quicker than with traditional manufacturing.
UHT Atomizer
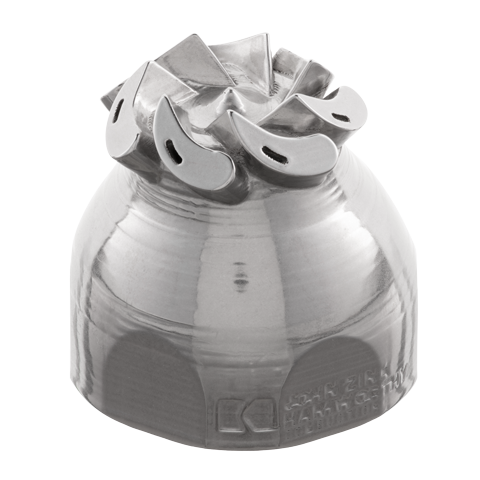
A leading vendor of emissions control and clean-air combustion systems, John Zink Hamworthy Combustion recently launched a project to redesign the UHT Atomizer for a Liquid Natural Gas (LNG) tanker.
The original, simple atomizer had a burner turndown of 15:1 during low load - like maneuvering around port or moving slowly - resulting in losses in fuel costs.
To create the new atomizers, JZHC engineers and designers immediately turned towards additive manufacturing. Using the Studio System, they were able to quickly produce functional prototypes of a new atomizer design with features - like complex channels and irregularly shaped holes - that would be impossible to produce with traditional manufacturing, yet are very easy to print.
This dramatically improved the fuel-air mixture in burners, allowing ships to reduce the amount of fuel they burned. The final result was a new atomizer that had a radically improved burner turndown of 25:1, a 67 percent improvement over the earlier design. With the new burner in service, customers could realize fuel savings of $90,000 to $160,000 annually.
Metal Additive Manufacturing allowed for multiple iterations of the UHT atomizer to be prototyped prior to selecting the final design.
Downhole Tool Slip
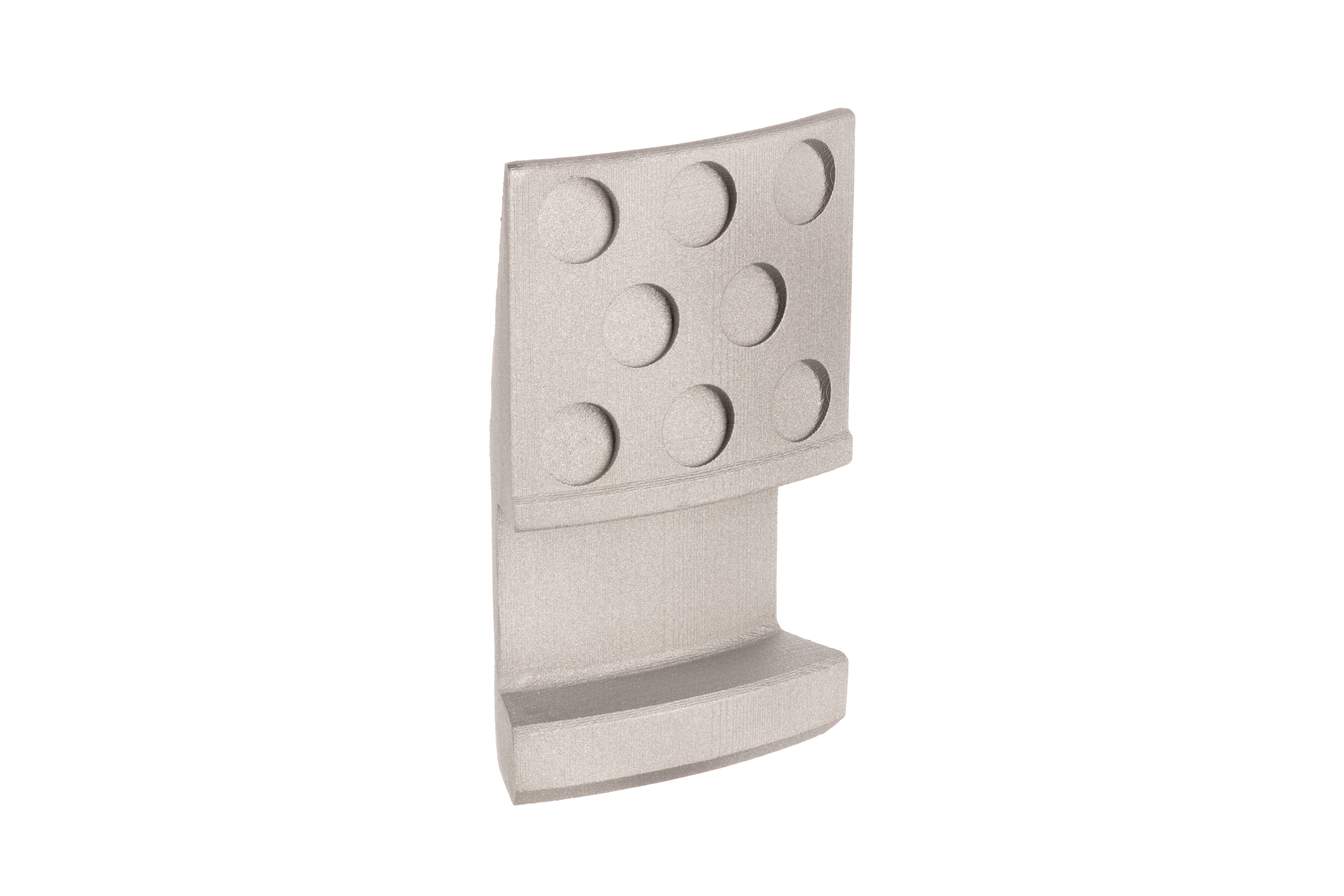
A common component in the oil and gas industries, this downhole tool slip is used for a frictional hold between a frac plug and a pre-existing pipe.
The part was prototyped on the Studio System to test different face geometries in an effort to optimize the hold for differentpumping scenarios. By printing in metal, the geometry could be functionally tested for its performance, not just its form and fit.
The part is consumable and must be milled out of the pipe after pumping is complete, so keeping the cost and lead time low is essential. Once the design was locked in, this part could be mass-produced on the Shop System, leading to a greatly reduced part cost and an accelerated manufacturing lead time.
Bulb Nozzle
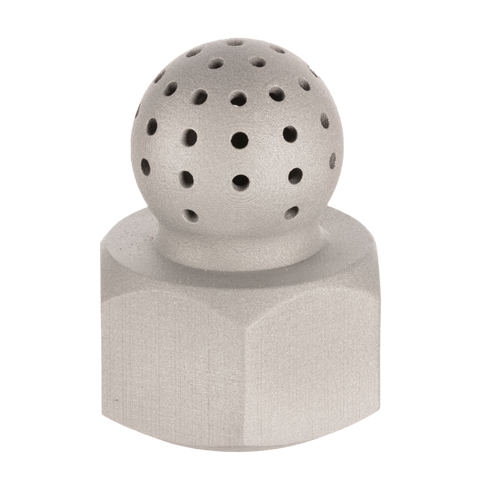
This part is a custom spray nozzle used in chemical processing.
Though normally cast, followed by extensive secondary machining operations, this part needed to be produced in quantities of approximately 300, making it an ideal fit for the Shop System™. By printing the nozzles, the entire order could be produced in less than a week and required just one secondary thread-tapping operation.
Depending on the chemical operation, different spray geometries may be required - since 3D printing eliminates the need for tooling the nozzle can be changed on demand and printed to conform to each process.
Oil Pump Sprocket
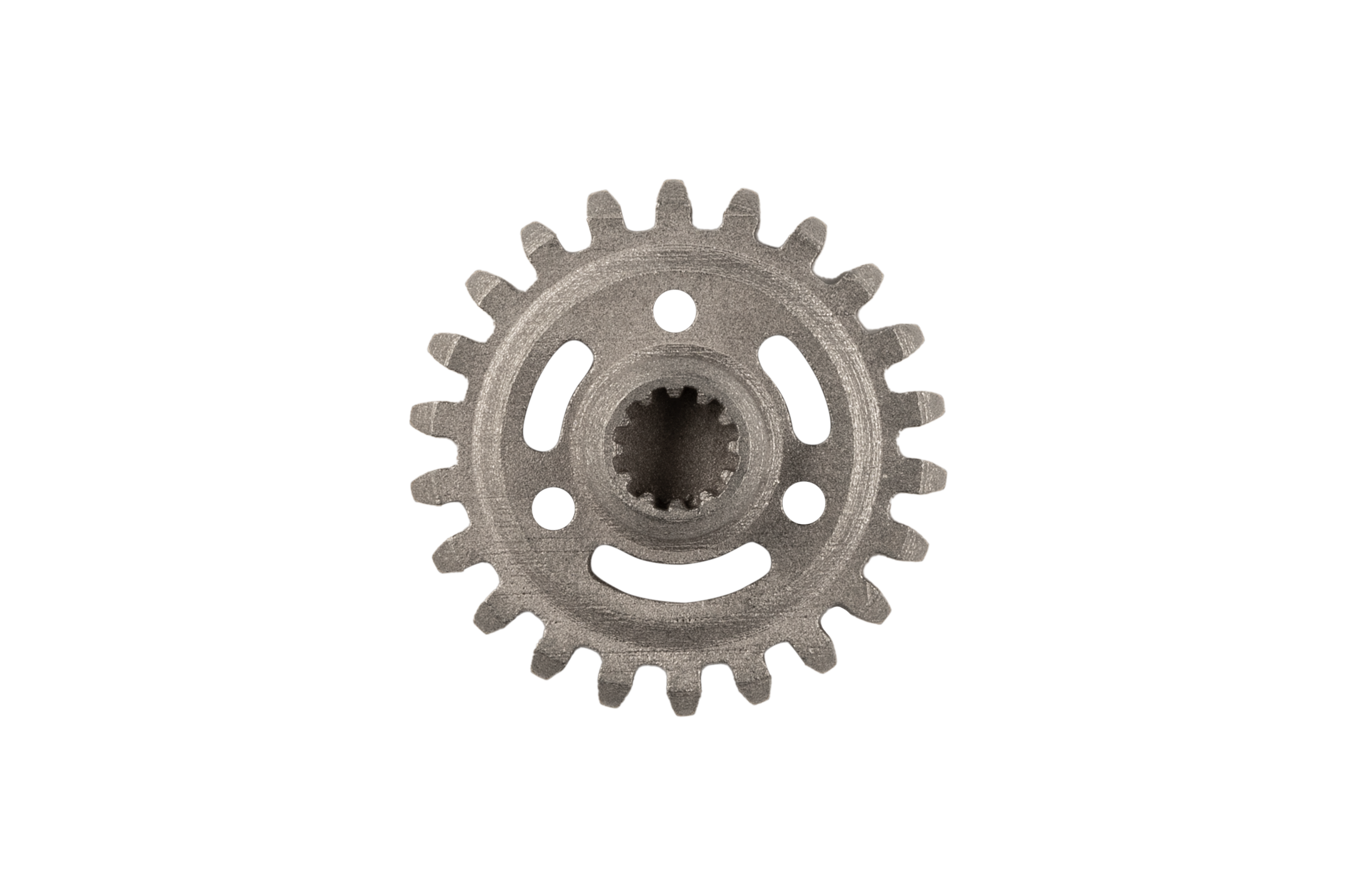
This is a sprocket used in a specially-designed pump for pumping viscous oil and gas fluids.
This part features complex geometry that would be very difficult to machine, or would require a large investment in both time and capital to produce tooling to manufacture via metal injection molding (MIM.)
With the Shop System, this sprocket can be produced on-demand without any investment in tooling, significantly reducing both part cost and manufacturing lead time. Since printingrequires no tooling, the sprocket design can be easily changed to accommodate other fluids - simply change the CAD model and send the new design to the printer.