Metal 3D Printing for Design of Complex Mechanical Assemblies
Machine Design
The design and production of complex mechanical assemblies that accomplish targeted tasks requires extensive development to ensure efficient operation that produces consistent results. Used in a variety of industries, from food processing to packaging, these system designs also require easy repairs as components wear and accessible maintenance to ensure safety standards are met.
The Challenge
For simplicity, speed, and, most importantly, cost machine designers strive to use as many off-the-shelf components as possible. However, to ensure optimal performance for the task at hand often parts must be custom-made. Yet machine designs require relatively small volumes compared to other manufacturing sectors, making tooling investments cumbersome without the high volumes to drive down per-unit costs.
Custom custom parts are typically CNC machined or cast, both processes that can be expensive and time-consuming. Limited machine shop resources and nonrecurring engineering (NRE) time to create custom workholding fixtures as well as creating a mold to machine a casting pattern lead to significant added costs and lead time. These manufacturing delays caused by traditional methods mean innovation is stifled as iterations can greatly extend product development lifecycles.
And for equipment already out in the field, spare parts on-demand are needed to keep lines running as components wear. Companies need to be able to quickly manufacture replacement parts to get machines back up and running while keeping per-part costs low and avoiding warehousing costs.
The Solution
Additive manufacturing dramatically simplifies the process of creating custom parts. Because it doesn’t rely on tooling or fixturing, 3D printing from a digital file allows users to build parts layer-by-layer with faster turnarounds and at lower costs than machining or casting. Metal 3D printing for machinery and processing equipment is an ideal solution for rapid prototyping, flexible manufacturing to meet market demands, as well as on-demand spare part production.
The technology also opens the door to parts with greater geometric complexity, such as internal cooling channels or consolidated assemblies. The design freedom of additive manufacturing enables the combining of several parts into fewer, multi-functional assemblies to simplify manufacturing and/or increase efficiency.
The tooling-less design also means these complex parts can be designed with customizations that may be better suited for specific applications. To take an example from the food processing equipment industry, custom custom brackets built at an adjusted angle better prevent clogging during the skinning operation of a specific species of fish. Such iterations or customizations often cannot be justified due to the cost of tooling needed for traditional manufacturing methods. Metal 3D printing changes the math of that equation.
Metal 3D printing also streamlines the production of replacement parts, allowing companies to print exactly the part they need, when and where they need it. Digital inventory strategies realized with on-demand metal additive manufacturing significantly reduce warehousing costs and downtime.
Key Use Cases
1. Design Freedom and Assembly Consolidation
Building parts layer-by-layer eliminates many of the manufacturing constraints of traditional production methods. This design freedom allows parts to be innovated to optimize performance or increase production efficiency. Internal channels can be incorporated for cooling fluids or parts can be organically designed to reduce weight.
To simplify the manufacturing of many machines, many assemblies are made of easy-to-manufacture parts either held together with fasteners or welded. Additive manufacturing, however, allows multiple parts to be consolidated into a single assembly and built as one part, reducing costs and increasing efficiency. The roller screw below is used in a linear actuator to open and close a pilot valve in a steam power plant. Though typically fabricated from seven parts, the Studio System makes it possible to consolidate the assembly into one component.
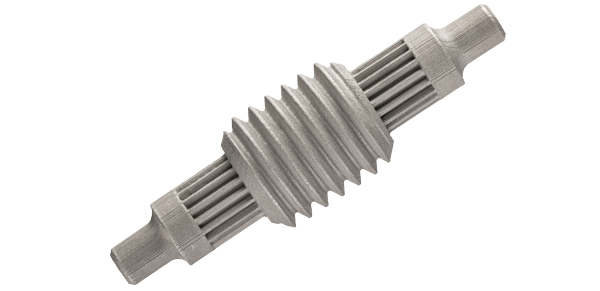
2. Functional Prototyping and Low-Volume Production
Manufacturing methods like casting, forging, and metal injection molding are ideal for mass production, but high cost and long lead times make them a poor choice for prototyping or low-volume runs. Metal 3D printed parts often achieve the same quality as those mass-production methods without the need for tooling, saving significant time and money. Since additive manufacturing eliminates the need for tooling, parts can be easily and quickly be printed, tested, and new variations printed as needed.
The front flange of a worm gear speed reducer below allows for the connection of different sized motors. When the speed reducer goes into mass production, the flange will be cast, and finished with multiple machining operations. By prototyping with metal 3D prints from the Studio System, the flange is quickly prototyped and functionally tested under high loading conditions to identify a design with optimal performance without the high investment cost of creating casting a mold and pattern for each iteration.
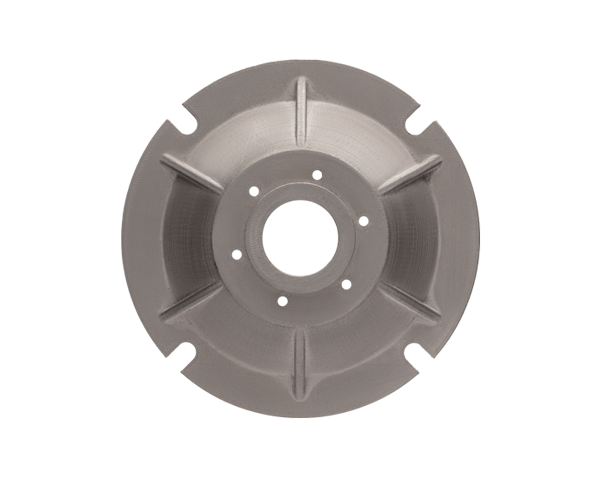
3. Reduced Development Lifecycles to Get to Market Faster
Product development costs time and money, and metal 3D printing helps designers respond quickly to market trends. 3D printing supports de-centralized manufacturing strategies by offering repeatable production closer to the end-user with a more localized supply chain. Building from a digital file without outsourcing tooling abroad or setup complex machining toolpaths means products are tested with much greater efficiency.
The custom coupling below transfers power between two rotating components. Its intricate details are difficult to machine, yet easy to produce with metal 3D printing. By printing this part, the designer was able to create multiple functional prototypes without any tooling change, allowing a variety of designs to be tested in just one week. One part with an optimum geometry was quickly selected to be adapted for mass production. The greatly accelerated development cycle and low per-per cost enabled by 3D printing iterations on the Studio System allowed the machine to get to market faster.
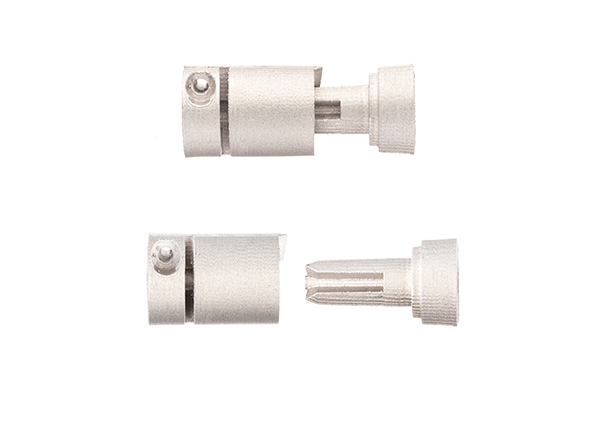
4. On-Demand Manufacturing and Spare Parts
Metal 3D printing allows for manufacturing flexibility with the on-demand production capability to produce qualified spare parts or design iterations on the same machine without tooling investments or setup time. Additive manufacturing gives designers more freedom to focus on performance, space, and material for the particular application rather than manufacturability and then store those designs in a digital inventory to produce spare parts as needed without warehouse costs.
The sensor holder shown below is used to secure multiple sensors while measurements are taken in a running machine. The intricate geometry and required volume make it an ideal candidate for metal 3D printing. The part was printed as needed on the Shop System with an extreme reduction in both manufacturing lead time and part cost and any design changes can be produced by simply uploading a new design file to print.
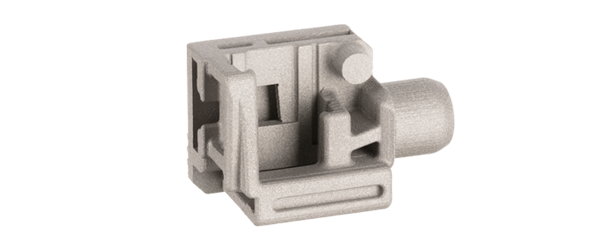