Metal 3D printing for government and defense
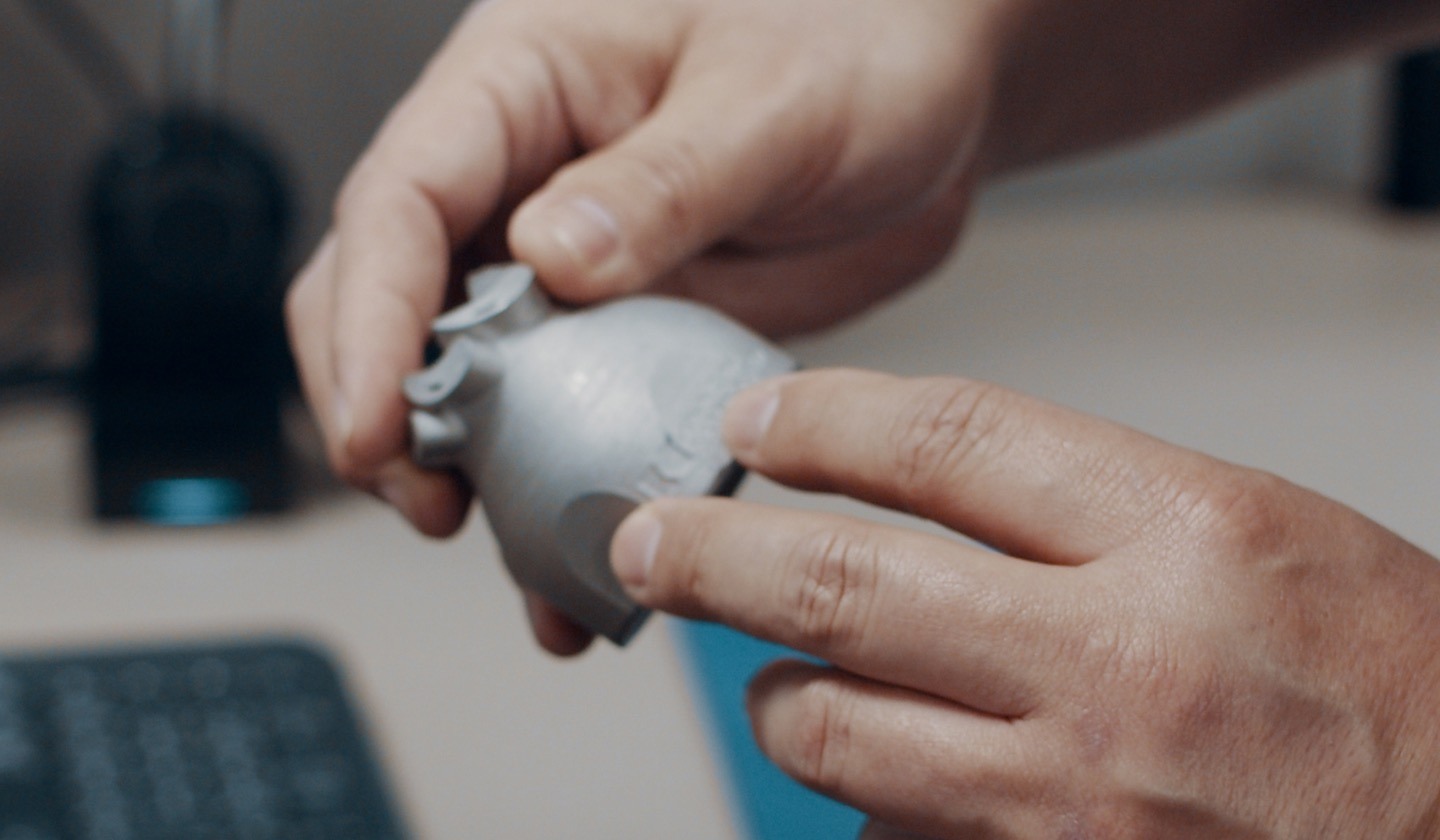
Government and Defense
Encompassing more than 100,000 companies and subcontractors around the globe, the government and defense industries produce everything from equipment for law enforcement, infrastructure and public transit to the development, design, production and maintenance of military weapons and systems, components and parts.
The Challenge
The mission-critical nature of many of their applications mean government and defense manufacturers face a number of unique challenges, starting with production volume.
From producing a handful of prototype parts for research to mass producing a part for field deployment, government and defense manufacturers must be able to quickly move between low- and high- volume production, something that can be difficult - and expensive - for traditional manufacturing processes.
To stand up to the harsh conditions they’ll face, including high stress, heat and corrosion, those parts need to be made from metal - and often alloys with specific composition or performance criteria that can make them difficult to machine.
Adding to the challenge government and defense manufacturers face is the fact that projects may last, in some cases, for 70 years or more. Maintaining or replacing parts over decades, however, can be challenging. If the original drawings or tooling is lost, they must be recreated from scratch, a process that is both time-consuming and expensive.
While all manufacturers aim to reduce delays in parts procurement, it is even more critical in the government and defense industries, where having or not having a part could literally be the difference between life and death.
Challenges for government and defense manufacturers aren’t solely related to the production and replacement of parts, but also extend to the supply chains manufacturers use to deliver them. In addition to issues related to warehousing and tracking spare parts and the logistics of ensuring parts are delivered where and when they’re needed, production lines and machine shops are often kept open year round, yet may only produce a handful of parts a year.
The Solution
Using additive manufacturing, government and defense manufacturers can answer each of those challenges.
Because it eliminates the need for tooling, additive manufacturing dramatically simplifies production, allowing manufacturers to go from printing a handful of parts to mass producing items with ease, and do it without affecting per-part costs or manufacturing lead times.
With a wide variety of common alloys available for printing, manufacturers can select materials that will withstand the conditions a part will face. When parts face particularly harsh conditions, additive manufacturing makes it easy to create parts from hard-to-machine metals like H13 tool steel or Alloy 625.
The elimination of tooling also dramatically simplifies the production of replacement parts. Rather than warehousing a large inventory of spare parts, companies can store designs in “digital warehouses” that are accessible from anywhere in the world.
Designs can then be downloaded and printed when and where they’re needed, greatly reducing both part cost and lead times. In cases where designs are unavailable or lost, parts can be scanned and the designs recreated quickly, ensuring future replacements can be rapidly produced.
Additive manufacturing’s ability to create geometries that could not be produced by any other manufacturing method is another significant benefit, particularly for defense applications, where systems need to be both high-performance and reliable to ensure mission success.
Using additive technology, manufacturers can create designs that achieve higher performance than traditionally-manufactured components. For example, heat exchangers can be designed with complex lattice structures that are more efficient at cooling mission-critical equipment, allowing systems to run for longer periods and at higher speeds. Another example might be lightweighting humvees, tanks, or warfighter equipment with lattices and generative design, allowing for them to travel farther with greater efficiency, while reducing strain on both people and mechanical systems.
Safety shut off yolk and handles
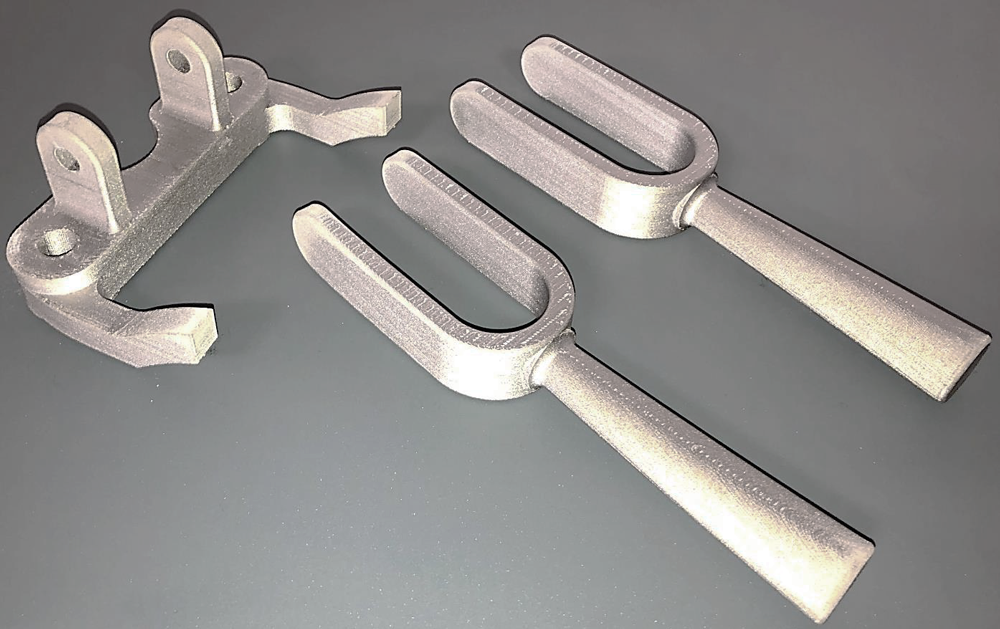
A key piece of safety equipment, this shutoff yoke and handles are installed on the USS Blue Ridge (LCC-19), which provides command, control, communications, computers, and intelligence support to the commander and staff of the United States Seventh Fleet. Originally these parts were made via casting, requiring extensive hard tooling. When they needed to be replaced this tooling no longer existed. Rather than recreate the tooling the parts were easily and affordably printed using the Studio System, and were ready in just a few days, without the need for tooling.
Helical Heat Exchanger
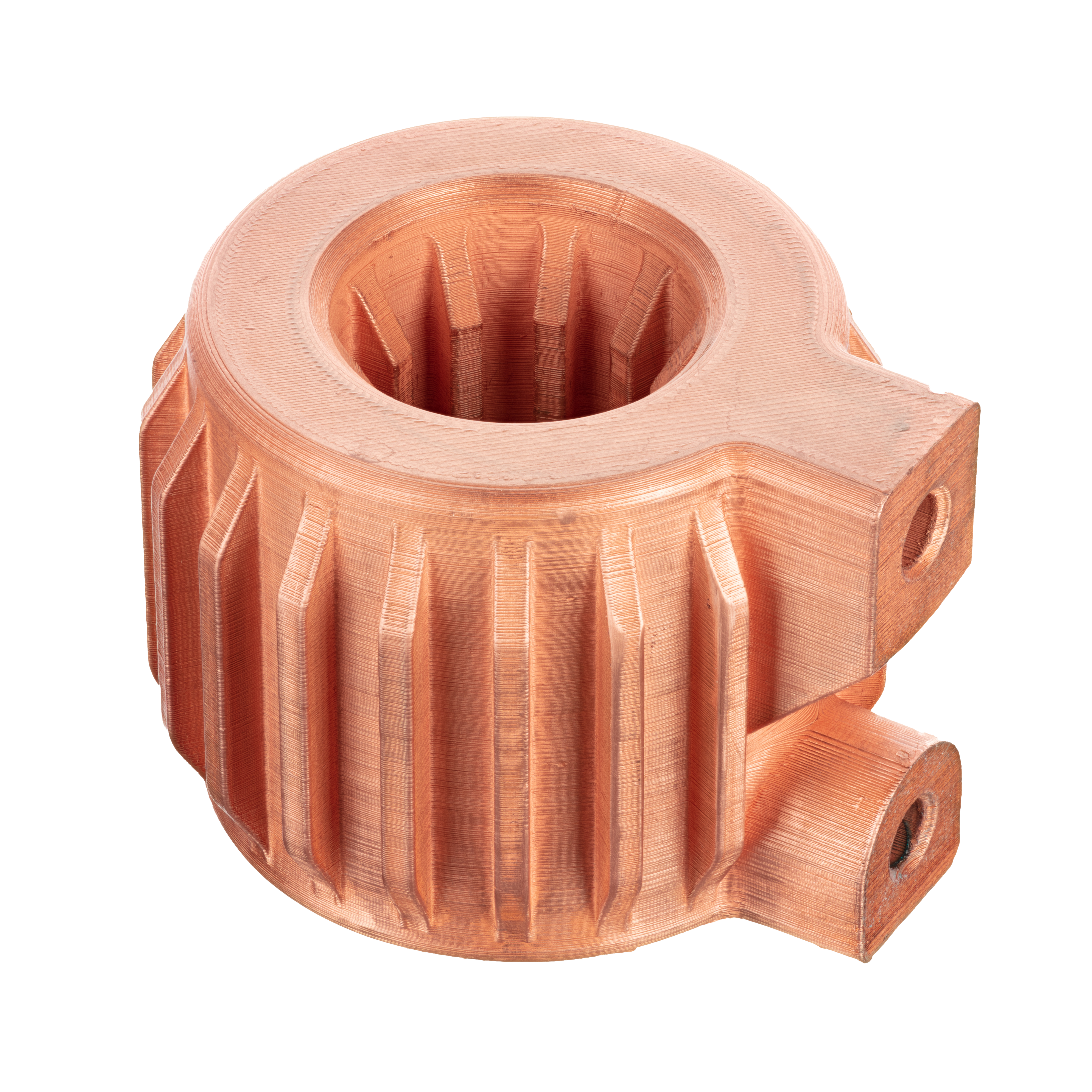
This is a heat exchanger used in chemical processing, and features a helical internal cooling channel used to cool a hot gas as it flows through a pipe.
Using the Studio System, this heat exchanger can be printed with an internal helical channel that allows cooling fluid to flow through it. The complex geometry of that channel can only be made with additive manufacturing. When combined with the external fins, this heat exchanger enables a much higher heat transfer rate than a traditional part. Since very low quantities of this part were needed, the Studio System was an ideal manufacturing choice because it is easy to use, eliminates the need for tooling and has a very low operator burden.
Ventilator Components
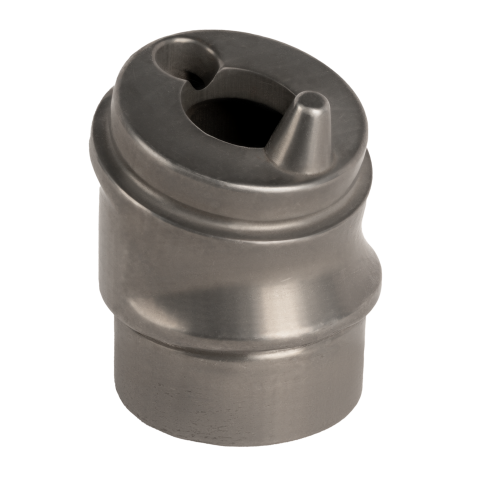
When the Covid-19 pandemic began, the world was faced with a number of significant problems, and among them was a shortage of ventilators. A team of engineers at Rise quickly began to develop an open-source, low-cost ventilator to help solve the problem.
The team needed to produce parts quickly, while maintaining the ability to iterate on those parts rapidly. The Shop System allowed the team to print hundreds of iterations in just a few weeks during the design process. This was possible thanks to the easy-to-use and high-speed nature of the Shop System - as soon as a new iteration was designed it could be sent to print, with end-use metal parts ready to test in just a few days. The team completed their ventilator design and have since open-sourced it for anyone around the world to manufacture.
Lightweight Gearing
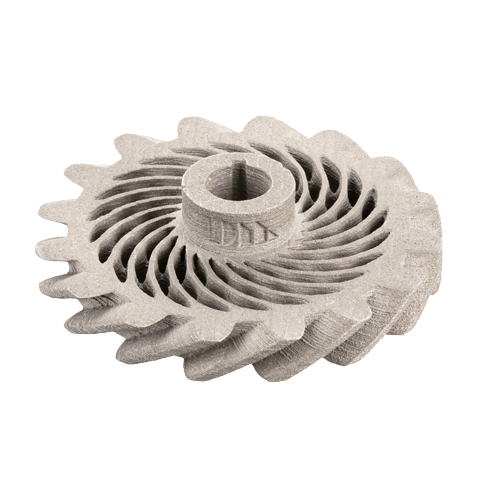
This gear features complex lattice structures that can only be created via 3D printing. Those structures drastically lightweight the component, but still provide the strength and stiffness the gear requires. With new, high-volume binder jetting systems like the Desktop Metal Shop and Production systems, it is now possible to print these complex lattices in high volumes, allowing for the parts to be used in high-volume, end-use applications.
Oil Pump Sprocket
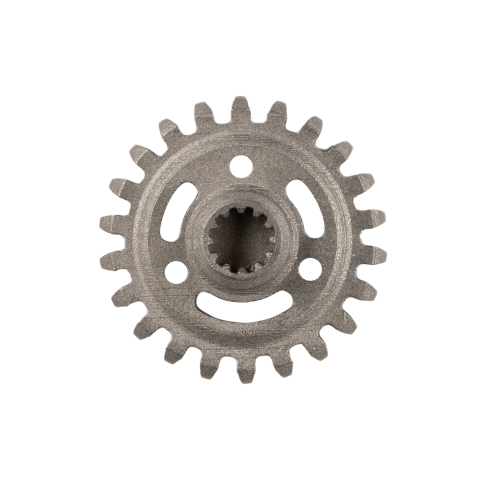
This sprocket is a key component in machinery used to pump viscous oil and gas fluids. The complex geometry of this part would be very difficult to machine, or would require significant investments, both in time and capital, to manufacture via metal injection molding (MIM.)
The Shop System allows this sprocket to be produced on-demand without any investment in tooling, significantly reducing part cost and manufacturing lead time. With no requirement for tooling, the sprocket design can be easily changed to accommodate other fluids.