Top 5 Reasons Metal 3D Printing is Spicing Up Food & Beverage Equipment
Why 3D Printing?
While mentions of 3D printing for food may bring to mind chocolate extruded into cool decorative shapes, additive manufacturing is actually transforming the industry behind the scenes – making food and beverage processing equipment safer, more productive, and delivering all-new innovations to the nearly $60 billion industry.
If you’ve ever watched an episode of “How it’s Made” on Discovery TV, you’ve seen the complexity of cleaning, cutting, mixing, swirling, layering, stretching, shaping, or molding of food or beverages in solid, semi-solid, or liquid states. And that’s all before they get packaged by complex assembly lines that often resemble a Rube Goldberg machine.
In all, the food and beverage industry is a symphony of hundreds of thousands of complex mechanical parts and assemblies that perform tasks that must also meet strict standards for quality and sanitization. Metal parts, often made of stainless steel, are an industry standard material for that safety reason.
But making and shaping all of those complex metal parts comes with challenges, and this is where 3D printing, also known as additive manufacturing, offers value-added solutions. Building parts layer-by-layer eliminates many limitations of CNC machining and other traditional metal manufacturing approaches and offers increased design flexibility as well as numerous other benefits to food and beverage processing equipment manufacturers.
Desktop Metal, a leader in accessible metal 3D printing technology working with the food and beverage industry, has compiled the top reasons we see the food and beverage industry moving to metal 3D printing:
1. Performance Improvement
The top performance criteria of any processing equipment is the quality and efficiency of the product it outputs. Fish processing equipment manufacturer Curio measured one degree of heat transfer from the knife to the fish being processed through its filleting machine. “Heat increase means degradation and a shorter shelf life,” said Elliði Hreinsson, Founder of Curio.
Using the design freedom of additive manufacturing, Hreinsson added internal passages for ice water to flow through the machine’s parts. Easily added to the design when 3D printed layer-by-layer, the cooling channels offset the heat exchange but would have been very difficult and expensive to achieve with traditional methods. “By incorporating internal cooling channels within the components, we’re able to negate [the heat transfer] and help keep the fish fresh. We have been increasing the yield and increasing the freshness,” Hreinsson said. [Read the complete case study here]
2. Streamlined Assemblies
The design freedom of 3D printing also allows manufacturers to consolidate multi-part assemblies into more simplified monolithic parts that can improve performance while also eliminating welds or joints where bacteria can accumulate.
Before metal 3D printing, for example, fluid passages in some food equipment often required plastic tubes because the designs were not easily manufacturable in metal with traditional production methods, leading to more parts and complex assemblies. With 3D printing, however, building complex parts as one metal design with the internal channels already included is easily achieved.
Additionally, consolidating designs often provides the added benefits of lightweighting, which can improve the durability of equipment, and especially in the food industry, simplicity of cleaning with fewer individual parts to sanitize.
Metal 3D printing is leading to new innovations poised to transform the food and beverage industry and deliver enhanced safety and durability of the equipment.
3. Increased Sanitization
Safety is essential in the food processing industry and 3D printing’s design freedoms can aid with hygienic design by helping product developers eliminate the joints and angles required with traditional manufacturing.
Materials compatible with food contact like stainless steel and titanium alloys are available for on-demand production on Desktop Metal 3D printers. 316L stainless steel is an important material for food processing equipment due to its durability, corrosion resistance, and non-porous, easy to clean hygienic properties.
Several food and beverage processing equipment manufacturers are using Desktop Metal 3D printers for use with food products and customers have qualified their 3D printed parts for NSF standards 51 and 61.
4. On-Demand Production
Food processing machines are highly complex mechanical assemblies that can have well over 2,000 components, many of which have to be stored in inventory and, as a result, cannot be modified easily once they are in production.
However, building directly from digital files without the cost or lead times of traditional production for all of those separate parts allows product development departments to optimize process efficiency and decrease costs. Because 3D printing doesn’t require molds or other tooling, designers are free to iterate as needed, even after a product is in production.
Integrating metal 3D printing allows manufacturers to quickly test a prototype, validate a design, and print the same part in batch production for end-use. First lot parts for assembly of a new Curio fish filleting machine previously required 54-58 weeks of lead time to make metalcasting molds. With a Desktop Metal Studio System, Curio now gets parts within weeks and can introduce new machines to the market without production delays.
The ease of customizing the design of each component allows for continuous iterations that improve the user experience of a product as it is tested and used in the production environment. If the skin of a specific species of fish gets stuck in a Curio machine, for example, the company can easily print a bracket at a slightly different angle for that species that optimizes the performance without the wait or cost of new tooling.
5. Operational Efficiencies
With thousands of parts per processing machine, production of food and beverage equipment, as well as providing replacement parts, can be cumbersome. Metal 3D printing, however, allows manufacturers to produce parts on-demand from a digital file without warehouse inventory. Elliði Hreinsson, Founder of Curio, says, “We simplify by just having 316L stainless steel to print in stock without warehousing different parts. The material goes in the printer and you get out what you ordered.”
3D printing offers innumerable benefits producing instruments that are essential for the proper operation of machinery. The design flexibility of additive manufacturing enables ergonomic tool development for human ease-of-use that also can help standardize accuracy and production quality. Additionally, with the increased use of robotic arms in processing lines, lightweight components made with the design freedom of 3D printing are essential to help maximize the capacity of product the robot can handle.
The consolidated, lightweight, and optimized parts developed with the design freedom of metal 3D printing mean food processing equipment companies can create complex parts for their machinery that serve several multiple functions. The stainless steel roller guard picture below was 3D printed at the Hudson Valley Additive Manufacturing Center (HVAMC) for JBT, a leading global technology solutions provider to high-value segments of the food processing industry. The Roller Guide Saw Nozzle Block is part of JBT’s Adaptive 3D Portioning System, a large and very sophisticated system for the rapid processing of poultry, meat and seafood.
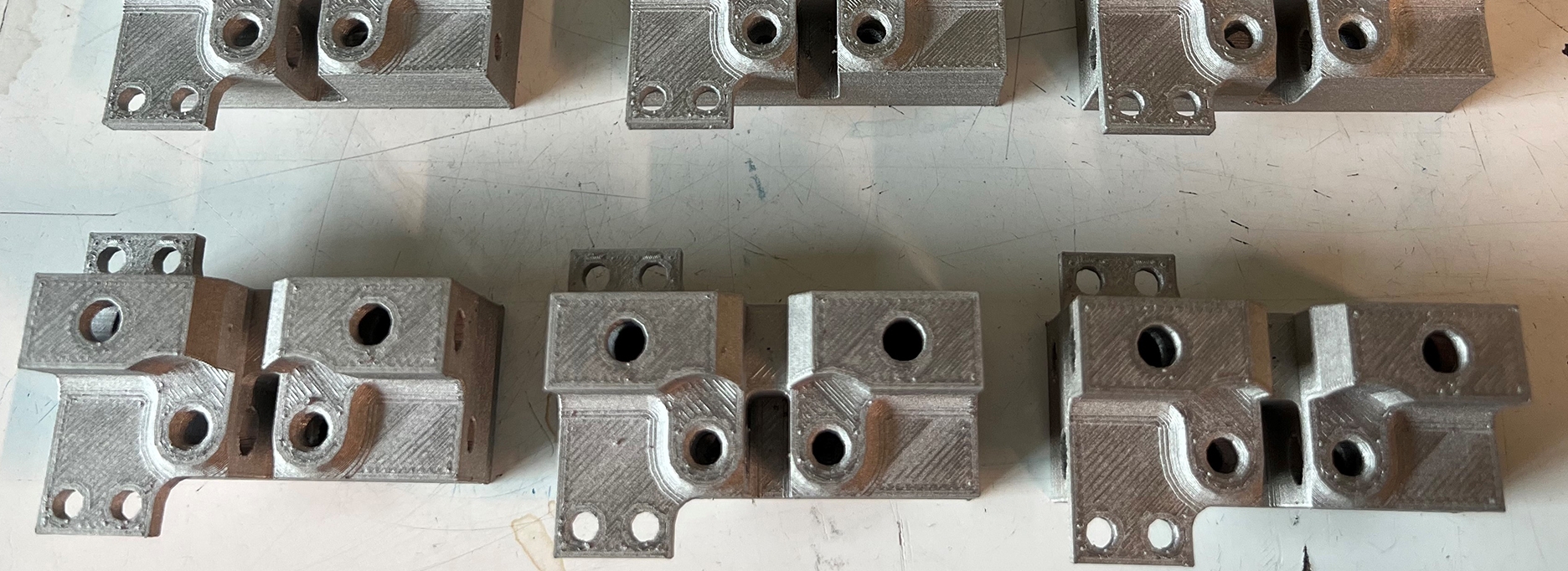
“The system simultaneously uses both water jet and mechanical cutting systems. The part is small and complex because it needed to serve several different purposes in a limited space.”
”
Dan Freedman, Dean of the School of Science and Engineering and Director of the (HVAMC). [Read more from HVAMC here]