Introducing the Studio System 2
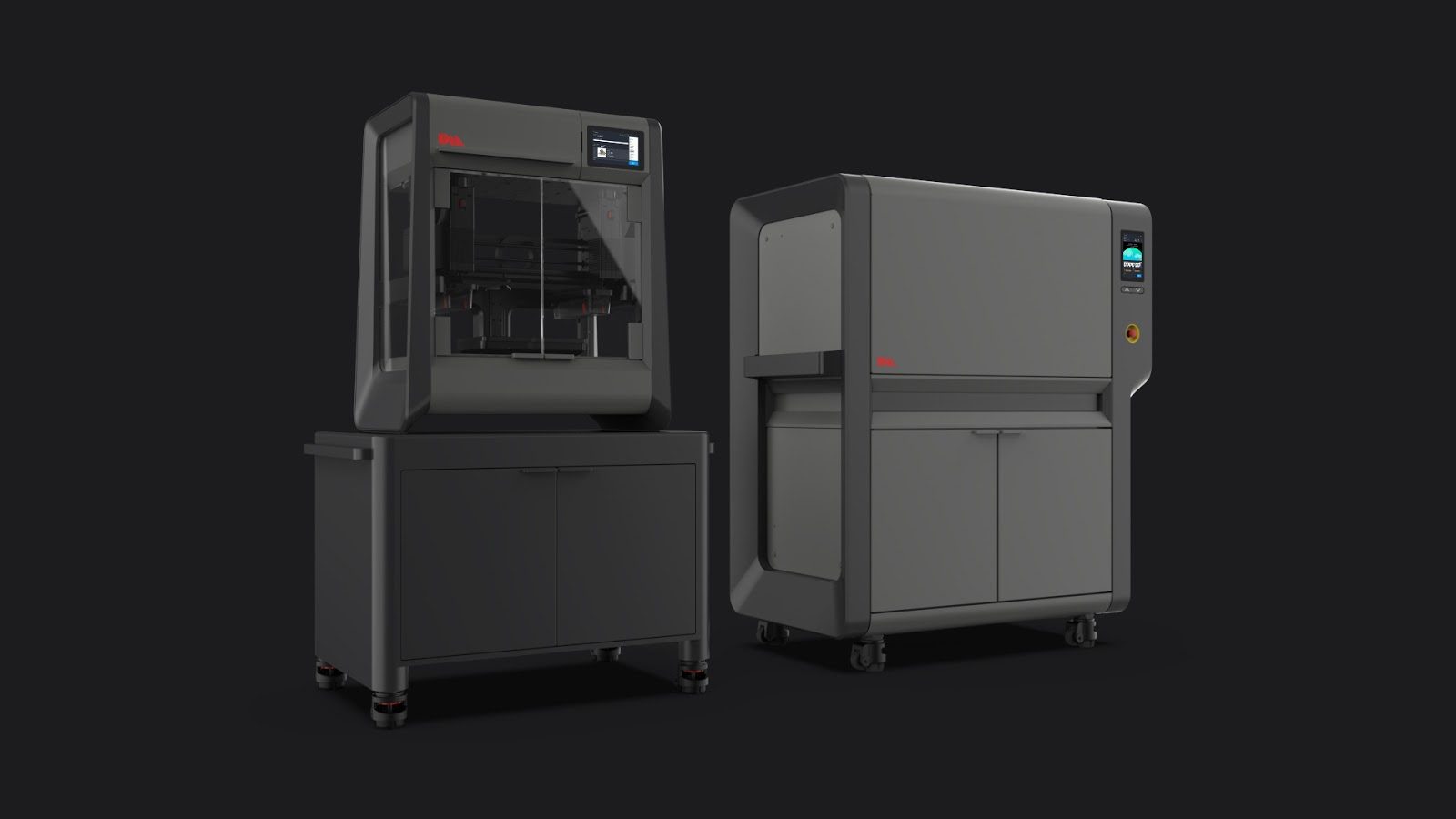
Studio System 2
With a simplified, two-step process that eliminates the need for solvent debinders, The Studio System 2 packs all the benefits of the original Studio System - no hazardous metal powders or lasers, no dedicated operators, no special facilities needs - into a package that’s more accessible than ever before and that produces even higher-quality parts.
Origins of the Studio System
When it was introduced in 2016, the Studio System brought high-quality metal 3D printing to the office environment. Where legacy powder bed fusion systems had cost upwards of a million dollars, required significant training, specialized facilities, and included safety hazards like loose metal powder and lasers, the Studio System allowed engineers, for the first time, to easily print metal parts in-house.
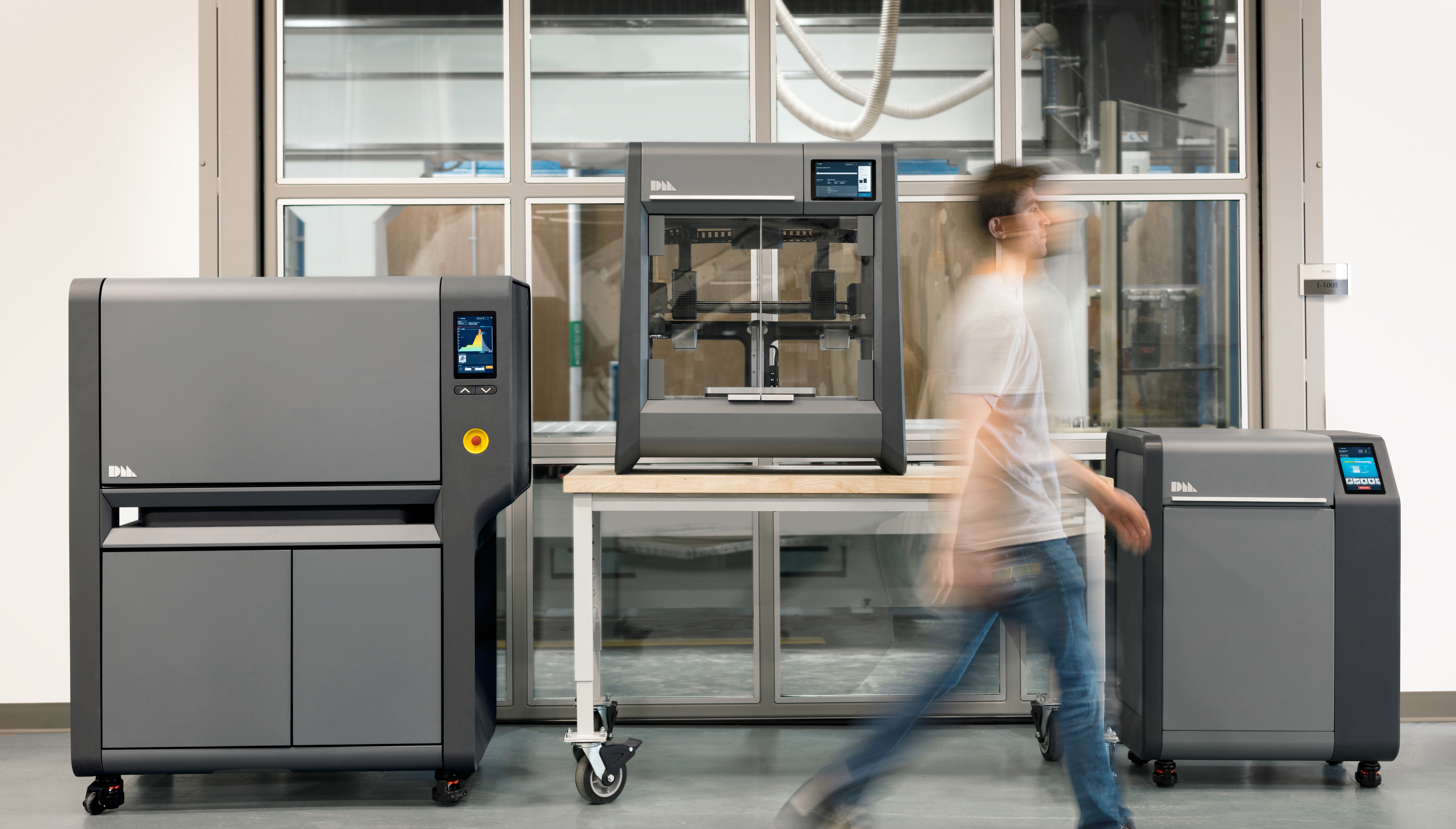
With easy access to high-quality metal 3D printing, designers and engineers were able to push the limits of design, producing everything from novelty jewelry pieces that couldn’t be made in any other way to atomizer nozzles for liquid natural gas tankers that resulted in significant increases in fuel efficiency.
Now, the next generation in office-friendly metal 3D printing has arrived.”
Studio System 2
The Studio System 2 takes ease and accessibility to the next level while delivering a wider range of possible geometries and significant improvements to part quality.
What's new?
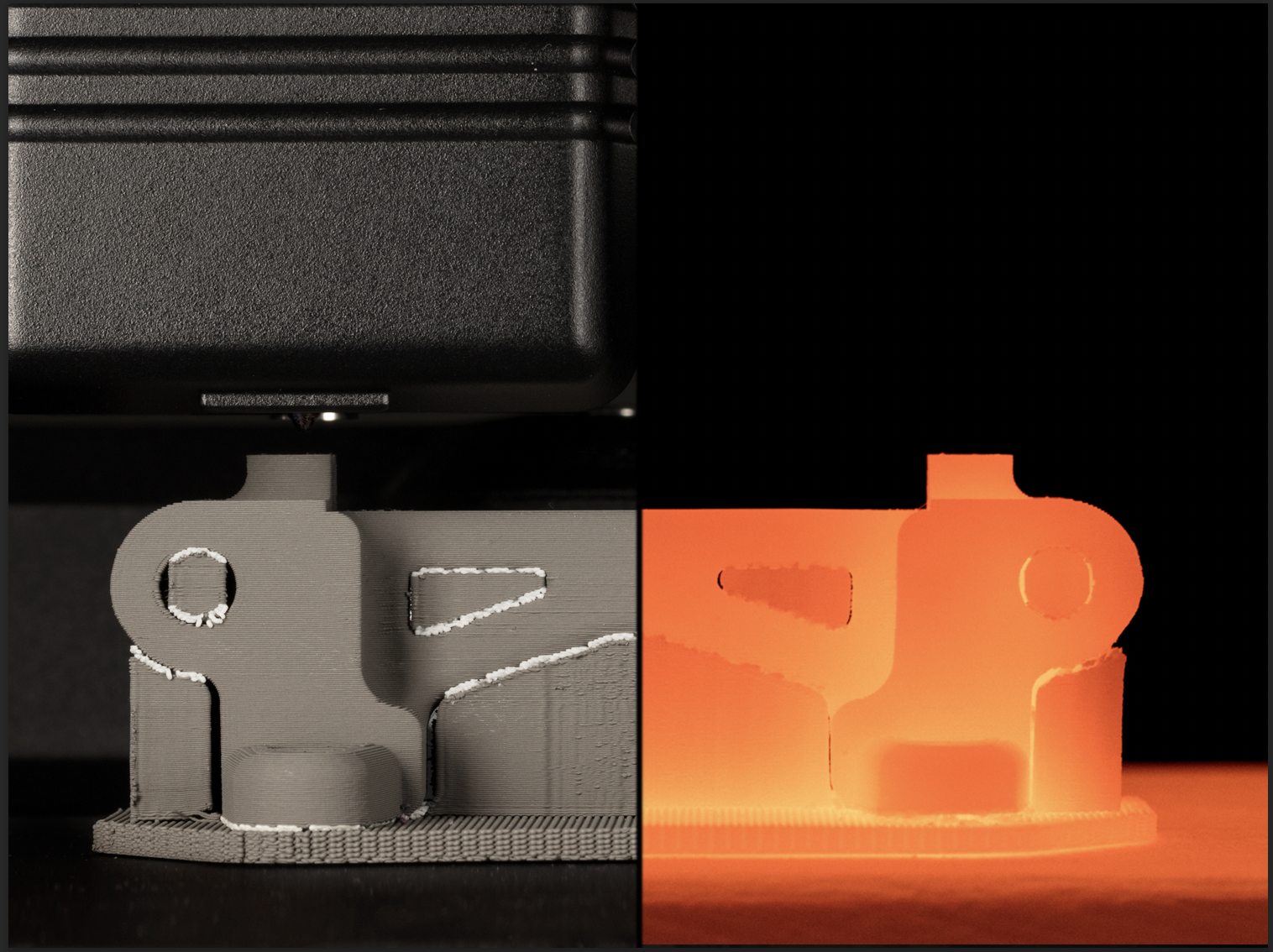
Easy Two-Step Process (No Solvents)
The original Studio System was designed from the ground up to deliver an easier and more accessible metal 3D printing solution for office environments. The Studio System 2 takes this a step further by eliminating the solvent debind phase entirely — unlocking a drastically simpler and nearly hands-off, two-step workflow. Parts no longer need to be batched before debinding, and then batched again before sintering. Instead, printed parts are placed directly into the furnace where they are debound and sintered in a single, customized sintering cycle.
With no solvent debind phase, the Studio System 2 process also eliminates odors and environmental health and safety (EHS) concerns related to solvent debinding, making it even easier for users to get up and running. Without the need for solvent debinding, users enjoy reduced part costs related to consumables, a reduced system footprint, and easier installation.
High Quality Parts
Based on data from thousands of prints, Desktop Metal’s team of engineers and material scientists have made significant advancements to Studio System 2 part quality.
The Studio System 2 features redesigned hardware, including a heated build chamber, new standard and high-resolution printheads and an improved sintering furnace, all of which add up to enhanced processing capabilities that enable the new two-step process. These hardware upgrades are combined with an all-new material system and optimized print and sinter profiles in Live Studio™, resulting in parts with significantly improved surface finish on support-facing surfaces and reduced stair stepping on side walls.
Reliability and Part Success
Designed to consistently deliver high-performance metal parts, Studio System 2 minimizes the trial and error common in alternative 3D printing processes, enabled by new print profiles and a re-engineered interface layer material for more even shrinkage during sintering and increased part success across an array of geometries.
Updated print profiles
Built in print profiles make part creation as easy as a few clicks. For users looking for greater control, the Studio System 2 also offers over 90 parameters for fine-tuning, making it easy to tailor parts to your exact needs.
The Studio System 2 features a new gyroid infill structure which offers a number of benefits to both the build process and part quality. This high-strength isotropic gyroid infill allows lightweight parts while retaining part strength
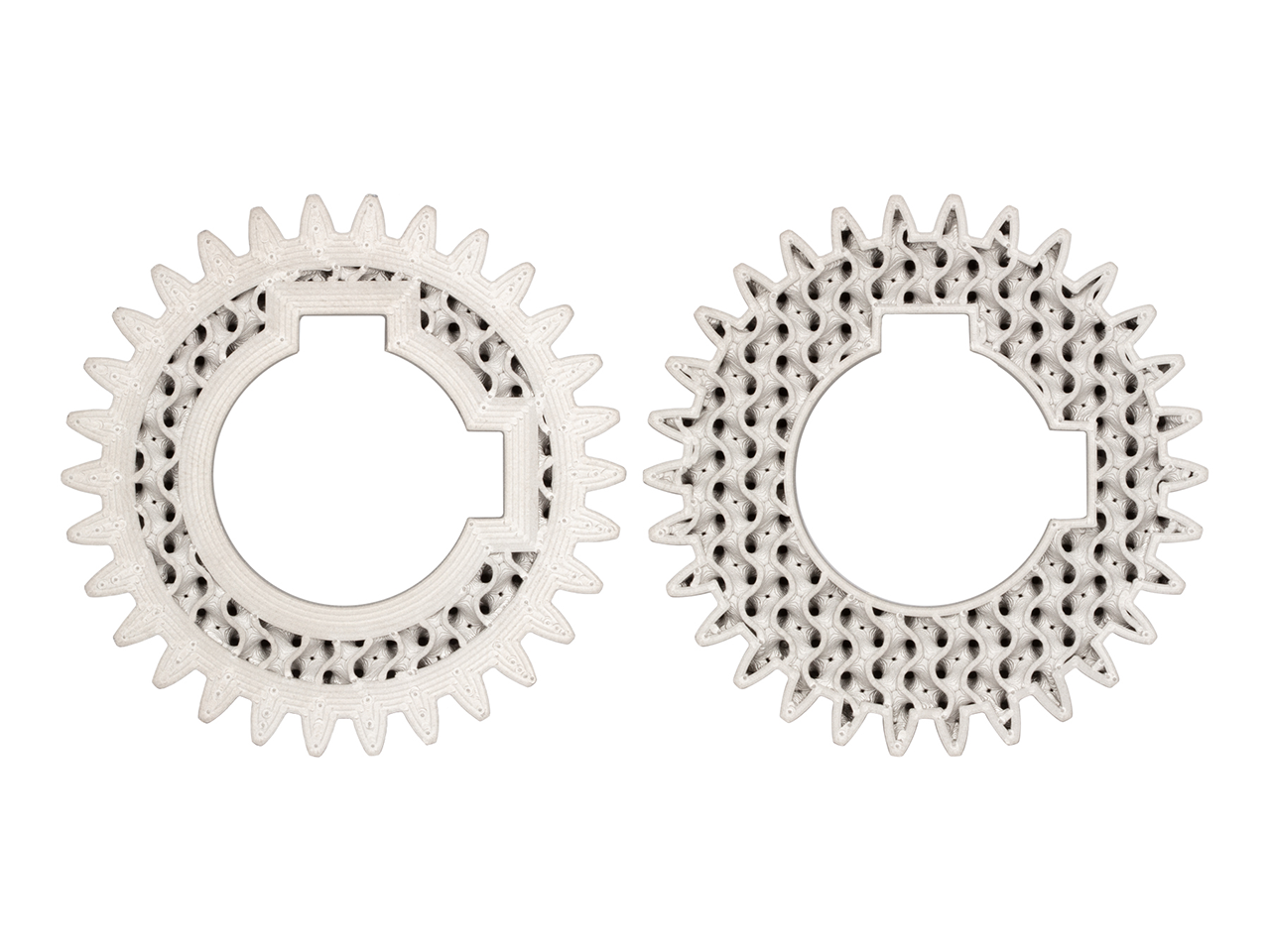
Most importantly, the gyroid structure allows for efficient thermal debinding, which is critical to the sintering success of any part and results in faster printing and faster overall processing of thicker geometries.
Processing time savings for thicker geometries:
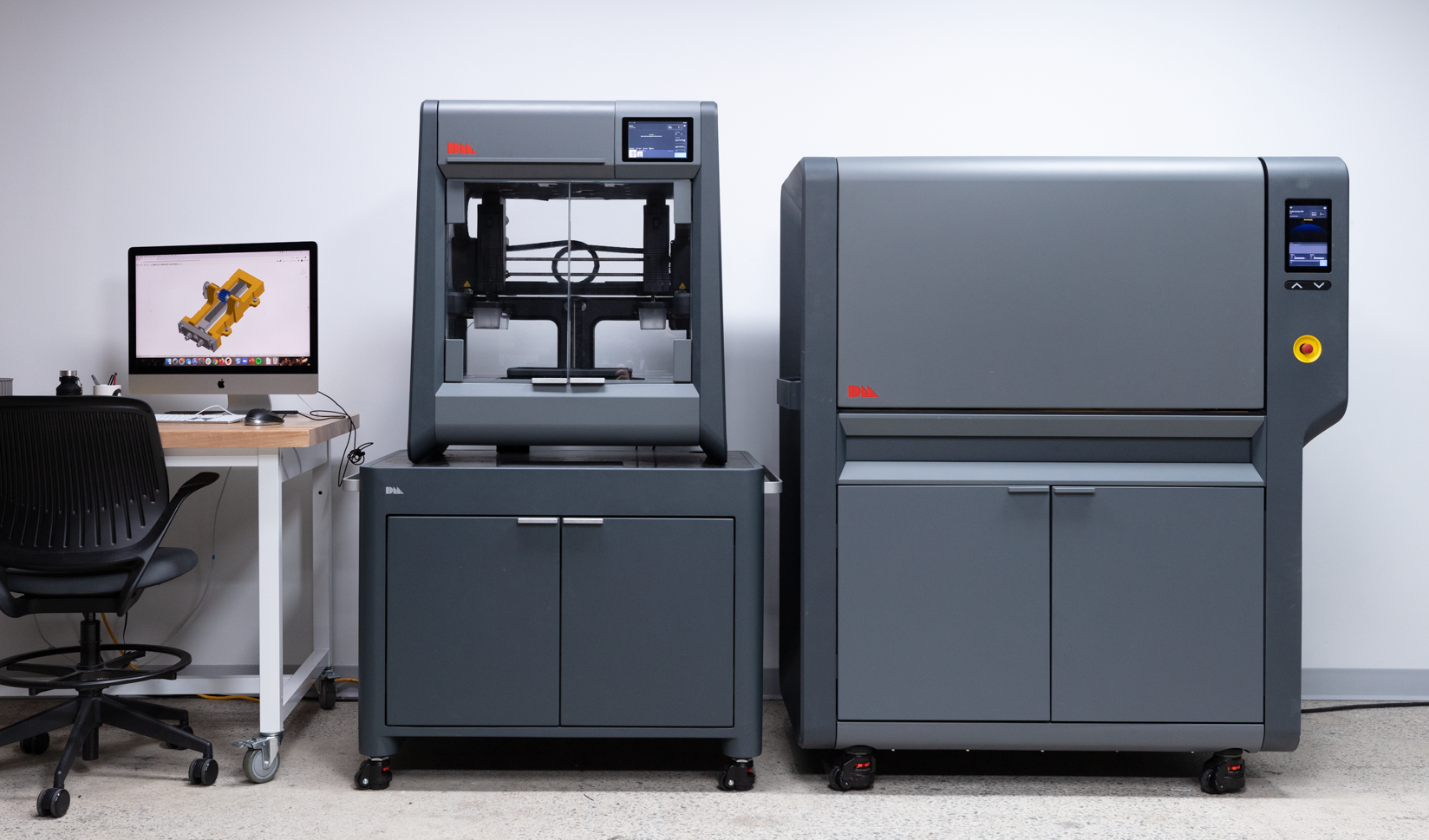
Designed for the Office
The Studio System 2 follows the same ethos of the original Studio System, prioritizing ease of use, accessibility, and office-friendly processing while maintaining excellent part quality and performance. Building on that framework, the Studio System 2 introduces additional features that make it the most office-friendly system yet from Desktop Metal.
That office-friendly design begins with the lack of solvents or loose metal powders - eliminating the need for additional ventilation or respirators. As a turnkey metal 3D printing solution, the Studio System 2 requires no third party equipment or specialized power requirements, making it incredibly easy to install. Just wheel it into your office - the system is designed to fit through an office door - and start printing.
What does this mean for your organization?
• Modernize your machine shop
• Build an efficient and accessible print farm
• Design an engineering organization of the future
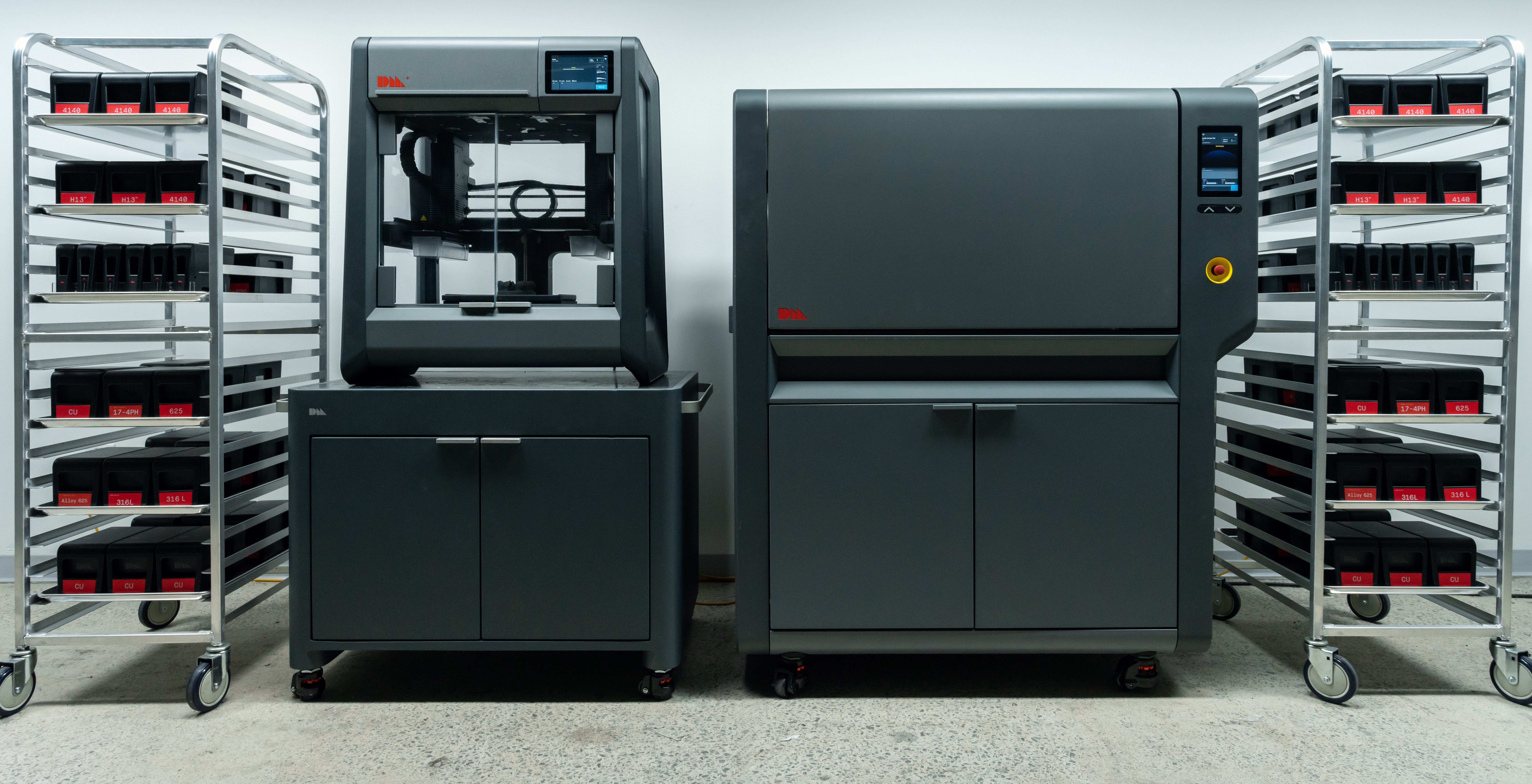
1. Modernize your machine shop
Modernize your machine shop with an agile and nearly hands-off solution. Produce jigs, fixtures, and tooling faster and more efficiently, reduce part cost and lead time, and bring new manufacturing lines up faster.
The Studio System 2 allows machine shops to produce high-performance tooling designs that complement existing manufacturing equipment, but which cannot be created (or justified) with traditional manufacturing methods—conformal cooling channels, undercuts, lightweighting features.
When low volumes of highly complex parts are needed, simply print them, without the operator burden or NRE time and costs traditionally associated with producing fixtures. Any critical dimensions or surfaces can be easily post machined on a 2.5 axis mill or lathe.
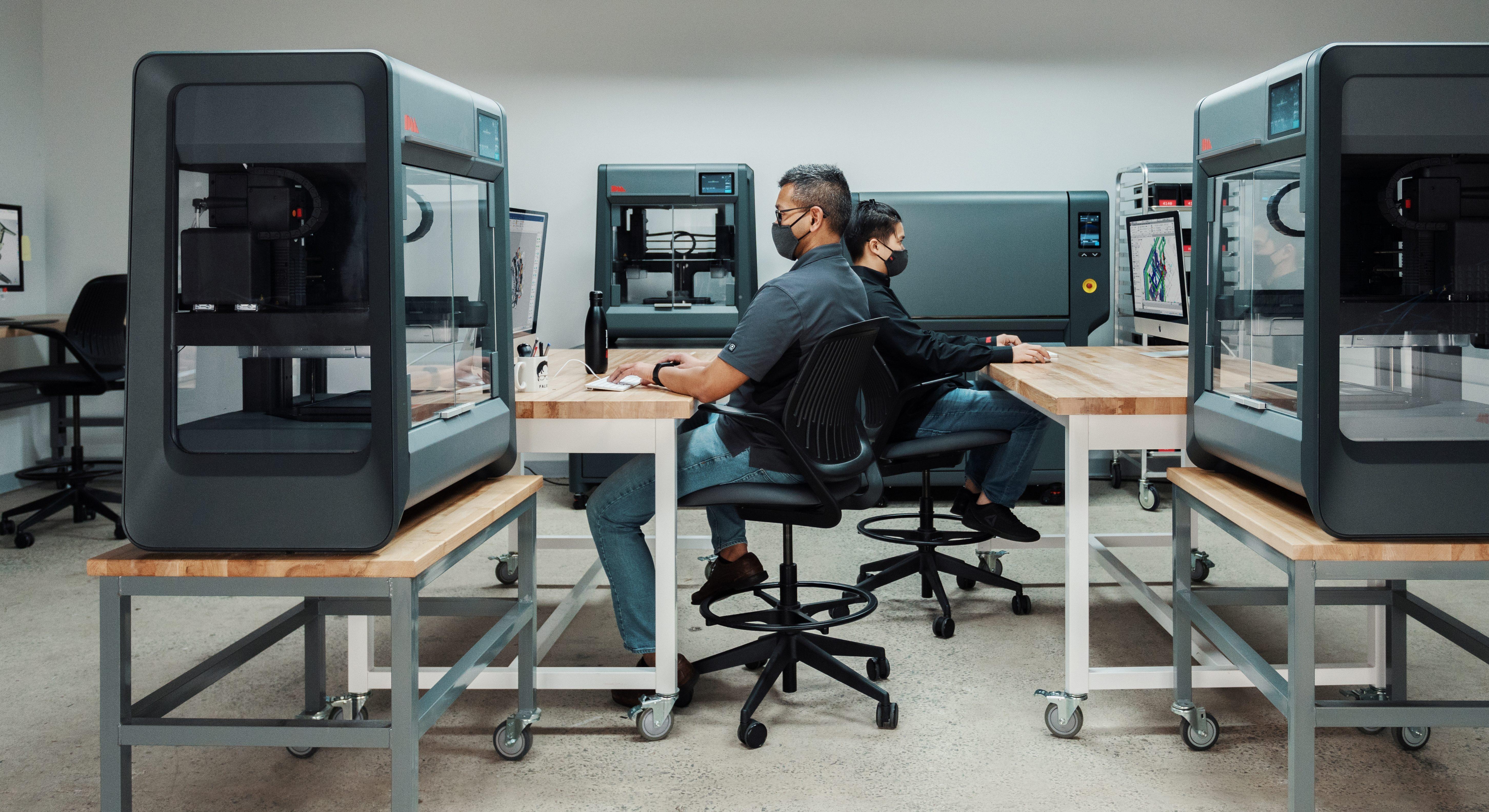
2. Build an efficient and accessible print farm
With an office-friendly design and two-step process, the Studio System 2 makes metal 3D printing more accessible than ever.
Create a print farm with multiple Studio System 2’s and allow your organization to quickly and affordably begin printing complex metal parts in-house. One furnace can support multiple printers, allowing your teams to print tens of parts per week with very little operator burden.
Produce functional prototypes, replacement parts, tooling, and one-off parts easily, simplifying manufacturing logistics and leading to better products.
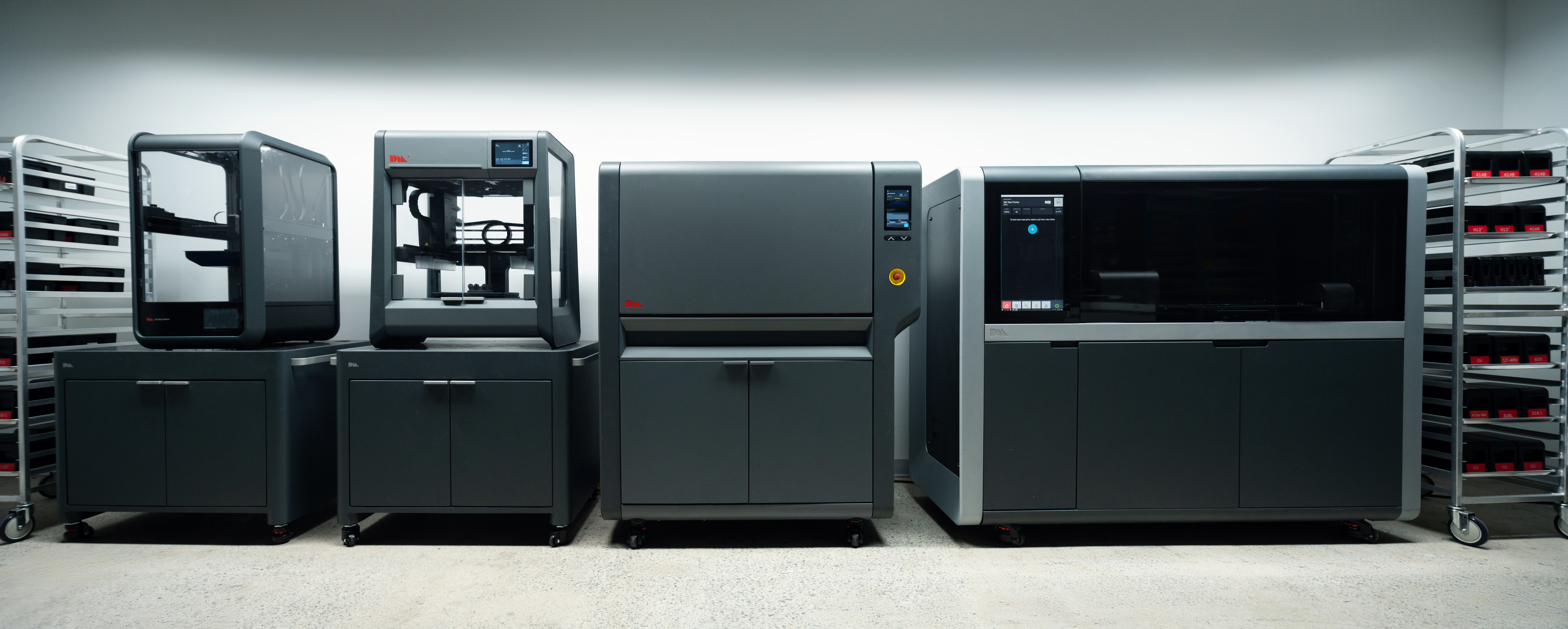
3. Design an engineering organization of the future
The engineering organization of the future likely includes a significant emphasis on 3D printing as it often allows engineers and designers to quickly and affordably create functional prototypes, real-time tooling and end-use parts more efficiently and affordably than other manufacturing methods.
Distributing printers across entire teams of engineers will allow organizations to truly unlock the full potential of additive manufacturing, including the ability to start production as soon as designs are finalized.
The agility afforded by additive manufacturing has the potential to unlock faster times to market, greater design efficiency, and lower manufacturing costs, ultimately delivering better products to customers.
- 1. Unlike comparable metal 3D printing systems, Studio System™ 2 eliminates loose metal powders and features a two-step process (no solvent debind required) and features Separable Supports technology with strategic splits for hand-removable supports, hot swappable cartridges and removable printheads to make material changes easy, and a fully software-controlled workflow.