Inkjet Technology in Desktop Metal’s Production System
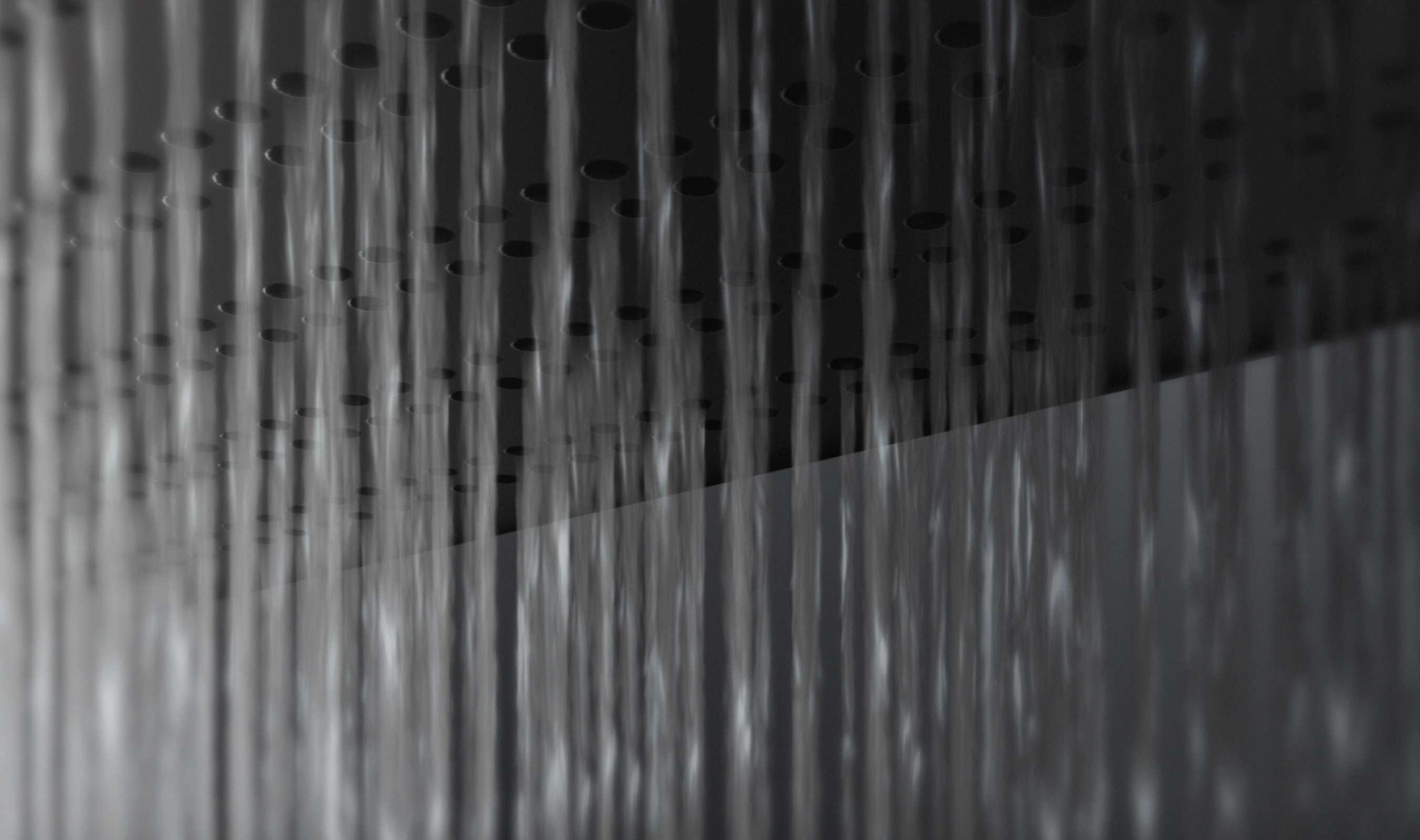
Introduction
Desktop Metal’s Production System is designed to be the world’s fastest way to additively manufacture metal parts. It leverages binder jetting, a technology created by Desktop Metal co-founder Ely Sachs in the labs of MIT. At the core of binder jet is inkjet technology, and it’s that technology that is one of the critically enabling aspects that delivers the speed of the Production System.
Binder jet consists of several processes, each performed serially. In the case of the Production System, those steps are consolidated, and performed in a single pass of the carriage using our Single Pass Jetting approach. This maximizes the efficiency of the system, eliminating any wasted motion. The steps performed to generate each layer on the Production System are:
- Powder is precisely metered across the bed (Constant Wave Spreading);
- The powder is spread and compacted by the compaction roller system;
- We apply our Anti-Ballistics technology to ensure the powder is secured in the powder bed and remains where we put it;
- Inkjet print heads are used to precisely eject drops of binder to create the part geometry for that layer.
In this article, we will focus on the fourth and final step, and explain why the choice and implementation of an inkjet system makes a significant difference in the performance and reliability of a binder jet system.
“Moore’s Law” and inkjet technology
We are all familiar with the now-famous prediction by Intel’s Gordon Moore that the number of transistors on a dense integrated chip would double every one to two years. That law has largely held true since the late 1960’s and is, of course, largely responsible for much of the technology we see around us every day.
While Moore’s Law is specific to the semiconductor industry, other industries have also benefited from miniaturization and production technology improvements to realize exponential advances in performance and cost. One of the technologies that has followed a similar trajectory to Moore’s Law is inkjet. Data from Wijshoff et al illustrate this progress:
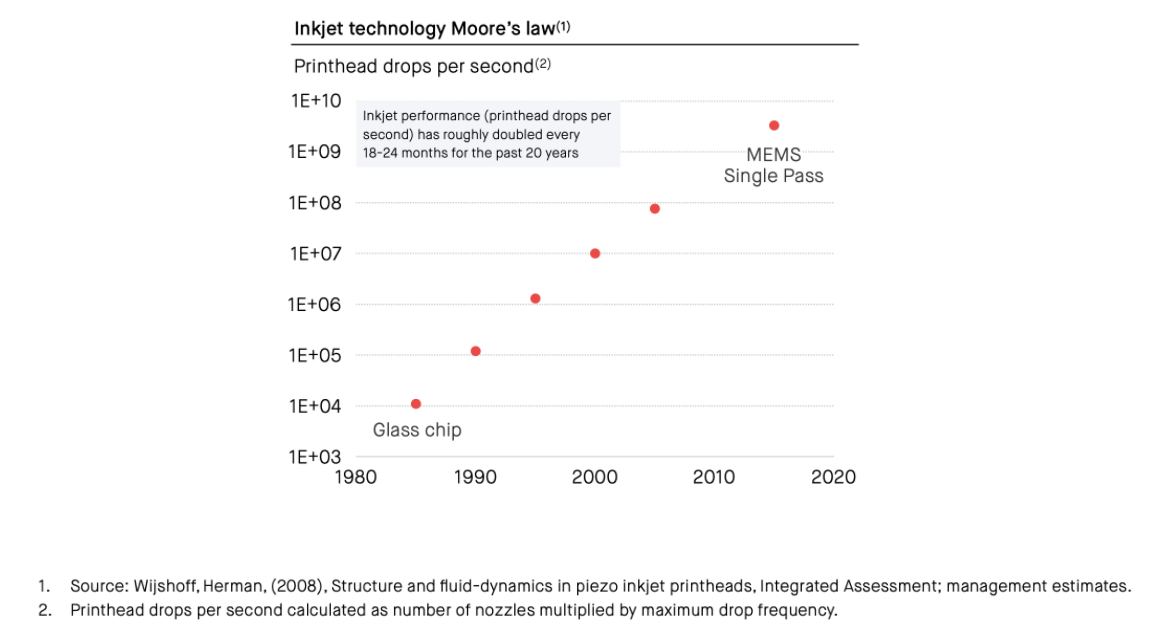
Inkjet is really the combination of several different disciplines. First, it leverages many of the capabilities of the semiconductor industry to create the driving circuits responsible for commanding the ejection of a drop. So it’s easy to understand how this aspect of inkjet technology has kept pace with Moore’s Law.
Inkjet also incorporates the field of microfluidics, the study of how fluids behave within small (micron-sized) channels and mechanical features. Naturally, an inkjet print head must deal with such flows when precisely ejecting microscopic amounts of fluid tens-of-thousands times a second. These same types of physics are found in other disciplines, like micro bioassays and biodefense. This field has advanced considerably over the past few decades through research at leading corporations and universities. Also driving microfluidics advancements are improvements in computation fluid dynamics (CFD) that are now capable of precisely modeling drop ejection physics at the sub-micron and sub-microsecond scale. An example from Flow-3D is shown below.
Another key advancement in the area of microfluidics comes through the innovation occurring in micro-electromechanical structures, or MEMS. MEMS leverages many of the same tools of the semiconductor industry (like photolithography) to create physical, mechanical structures rather than circuits. Improvements in those processes allow MEMS to produce smaller and more precise structures to control and manage fluid flow. It’s because of MEMS that we now have inkjet print heads with native resolutions of 1200dpi and higher. And because the tiny MEMS structures can respond more quickly, they are amenable to higher ejection rates, increasing the number of drops that can be fired from each nozzle every second.
Another area of advancement for inkjet is in actuator design. Actuators are the part of the inkjet print head that are responsible for giving the fluid momentum sufficient for a drop ejection. For the most part, there are two types of ejectors in widespread use today:
- Thermal inkjet uses small, resistive heaters to rapidly heat a small quantity of fluid past its boiling point, creating a small vapor bubble that pushes ink out of the nozzle to create a drop.
- Piezoelectric print heads use a piezoelectric crystal that deforms when subjected to an electric field. These deformations create pressure pulses in the fluid which ultimately eject a drop.
Both thermal and piezoelectric actuators have advanced appreciably in recent years. New materials and improved circuit designs have improved the efficiency, reliability, and longevity of resistors in thermal inkjet heads. Thin film technologies (also partially borrowed from the semiconductor industry) have reinvented the implementation of piezoelectric drivers, making them smaller and significantly faster-acting than previous designs.
Finally, inkjet depends on careful fluid design. The fluid being ejected must be designed for material compatibility of the entire system - including the print head - and deliver the desired drop ejection characteristics. In metal binder jetting, the binder is a critical piece of the entire system. Not only must the binder operate optimally in the head, it is responsible for brown part strength to facilitate depowdering and must burn off cleanly in a thermal debind cycle to produce the desired chemistry in the final part. New polymers and advancements in the chemical processing industry have broadened the pallet of options for binder formulation chemists.
Desktop Metal’s Inkjet System
Thanks to these advancements and other innovations, the Desktop Metal Production System employs one of the most advanced industrial inkjet systems in the market today, capable of delivering build rates of 12 liters/hour, with layer thicknesses of 65um. Some of the key characteristics of the drop ejection system:
- MEMS-based print head
MEMS technology enables the system to deliver 1200 dots per inch (1.44 million drops in a square inch) in a single pass. This delivers fine details and excellent surface finish in the part. It also makes the system inherently robust to any nozzles that might misfire during a print – because there are so many nozzles packed so closely together, you won’t even notice a single nozzle that is missing. - Piezoelectric actuator
The choice of a piezoelectric actuator was a conscious choice aimed at robust, long-term performance. Piezo actuators have almost no wear-out failure modes, and each nozzle is capable of ejecting hundreds of billions of drops. These heads are not “disposable,” but are built to last. - Greyscale technology
The piezoelectric design also imparts what we call “grayscale” technology. With a thermal inkjet head, you get only one drop size. Our print head can produce several different drop sizes, so rather than being “black or white”, each voxel can receive a “grayscale” value which might be black or white or somewhere in between. This provides ultimate control over binder saturation (how much binder is deposited at each voxel,) delivering the best print quality and the strongest brown part strength. - Fast frequency response
The MEMS design of the print head gives us very fast frequency response, meaning it can fire single drops at over 100,000 times a second. This lets us deliver binder faster, addressing more voxels in a smaller amount of time, and ultimately increasing the overall speed of the printer. We also take advantage of this high frequency response to offer more grayscale values to choose from when optimizing binder saturation. - Recirculating ink delivery system
This delivery system continuously feeds the heads fresh binder, making sure any contaminants are quickly filtered out, any air bubbles are instantly removed, and the binder ejected from the head is always the right chemistry. - Automated print head cleaner
The Production System contains an automated print head cleaner that periodically washes the face of the heads. Over time, powder can accumulate on the heads which, if left unchecked, can cause nozzles to clog. Our cleaner is fully automated and scheduled to ensure reliable, long-term drop ejection. Also, we’ve implemented a non-contact cleaning method that washes and vacuums the head; some powders can be abrasive, so by implementing a non-contact cleaning method we can prolong the life of the print heads. - Binder library
The binder is at the center of all binderjet systems, and this is certainly true for the Desktop Metal Production System. The binder has strict requirements that span nearly the entire process, from the printing stage right up to the start of sintering. At Desktop Metal, our team of binder chemists have decades of experience creating novel formulations and are uniquely qualified to meet these demanding requirements.
In summary, binder jetting technology has advanced by leaps and bounds in recent years. Some of this progress came from improvements in the inkjet technology that forms a central part of the binder jetting process. Desktop Metal has fully capitalized on these improvements and, by doing so, delivers a state-of-the-art metal additive system in the Production System that is capable of true production.