Optimizing Design for Additive Manufacturing: The Importance of DfAM for Binder Jet
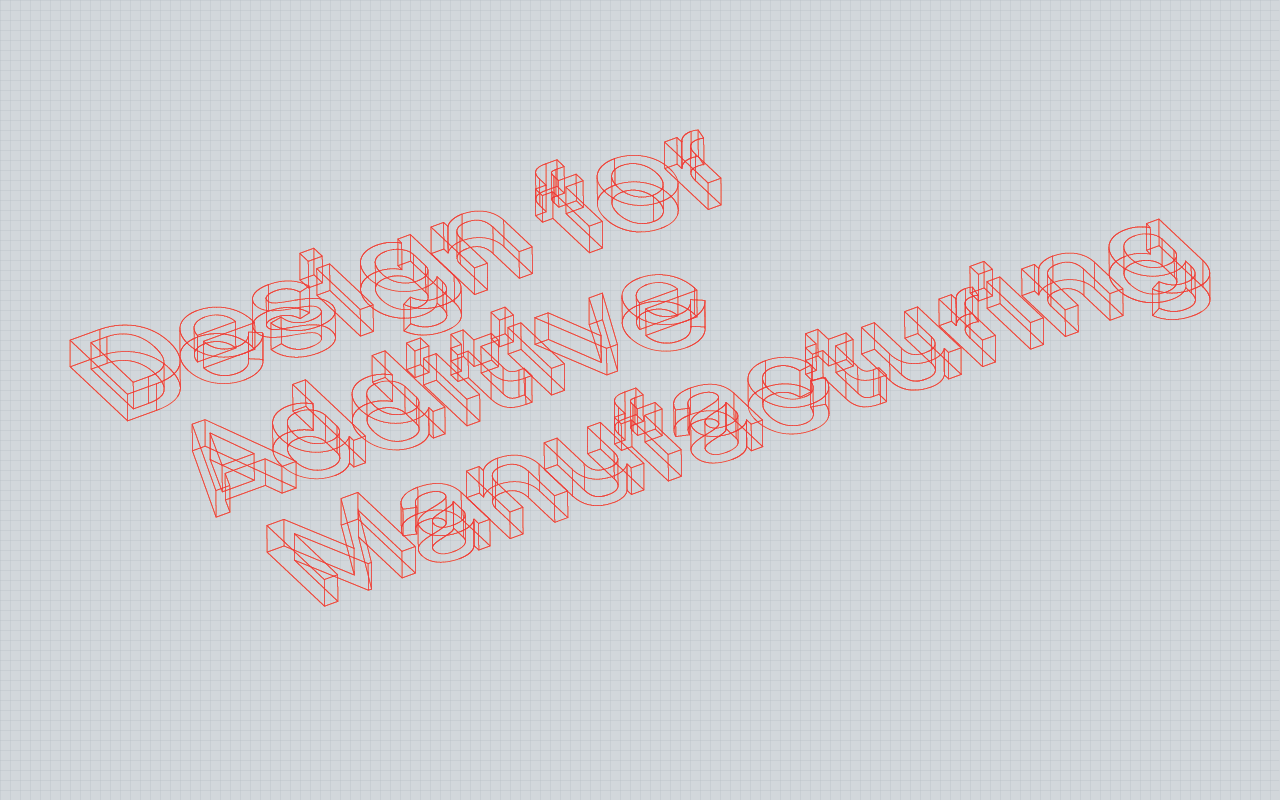
What Is Design for Additive Manufacturing (DfAM) and why does it matter?
Additive manufacturing (AM) technologies continue to revolutionize the manufacturing sector with innovative designs that can help reduce material waste and improve part performance. However, achieving optimal results from any additive process requires more than just adopting the technology itself. Design for Additive Manufacturing (DfAM) for binder jet is essential to unlock the full potential of building layer-by-layer from digital models, decreasing turnaround times and expenses by eliminating the need for hard tooling.
DfAM refers to the design principles and best practices tailored specifically for additive manufacturing technologies. Traditional manufacturing methods often face geometric restrictions that are easily overcome with additive processes like binder jetting. By producing traditional design assemblies with smaller manufactured pieces, we often compromise on the final performance of a product by adding unnecessary weight and features. With DfAM optimization, assemblies can be combined into complex, monolithic components 3D printed with ease and advanced, organic designs can be built without traditional manufacturability constraints.
DfAM for binder jetting enables the creation of intricate and customized components, all without tooling. In the binder jetting process, a printhead precisely jets binder onto a powder bed one layer at a time, building internal channels that increase performance, complex lattice structures that reduce weight, and custom variations all with ease directly from a digital file.
Five Key Principles of DfAM for Binder Jet
Binder jetting is known as one of the most versatile additive manufacturing methods because of its material and process flexibility, and effective DfAM for binder jet is key to reaping the benefits of the technology. Here is an overview of five important considerations:
Part Size
While virtually any size part can be made with binder jetting, for metal powder that requires sintering the technology has sweet spots. For its current maturity level, it tends to favor higher volume production, complexity, and parts that are fist-sized or smaller. Binder jetting can enable standard Metal Injection Molding (MIM) MIM-size parts at affordable lower volumes and also enable MIM-style parts at larger sizes, even exceeding 100 grams. Binder jetting is capable of delivering larger complex parts, often with optimization that reduces weight of the overall structure.
Compensating for Shrinkage and Warping
Metal parts produced with binder jet additive manufacturing are sintered after printing in a high-temperature furnace, where the particles fuse together into a final metal object that is dense, accurate, and can be machined. This final sintering step is nothing new in the world of metal manufacturing. In fact, it’s nearly identical to how metal parts have been made with metal powder and binder in the Metal Injection Molding (MIM) or press-and-sinter (PM) markets for more than four decades. Powdered metal parts shrink during the sintering process due to the consolidation of metal particles. Predictive algorithms in Desktop Metal software solutions automatically calculate shrinkage to provide scale up and design adjustments that compensate for sintering.
Learn more about our software solutions, including Live Sinter
Supports
Laser powder bed fusion metal 3D printing technologies require that both thermal and structural supports be designed and fabricated with a build. While support structures are not necessary for shape retention during the binder jet printing process, they may be needed during sintering when the material approaches its melting point and susceptible to deformations from gravity, friction, shrinkage, and other forces. Certain bridges and overhangs may require the use of sintering supports, designed together with the part to control sagging or other deformations. Alternatively, Desktop Metal Live Sinter software was developed as a tool to for engineers to simulate the sintering process and produce counter-warped “offset geometry” geometries that can dramatically reduce or eliminate the cost of printing supports.
Wall Thickness
Wall thickness is one of the most important design considerations for optimizing printing with binder jet. The upper limit of the wall thickness is determined by the ability of the binder to diffuse through the wall during the debinding process, while sections that are too thin can result in insufficient strength in the green part. Heavy parts with thick sections can benefit from lightweighting design strategies through the use of lattice structures while preserving other characteristics, such as load handling. Wall sections too thin, however, may be susceptible to breakage during depowdering and large variations in mass between thick and thin sections that will shrink at different rates and can lead to cracking.
Aspect Ratios
Aspect ratios drive allowable feature size, specifically, the size or width of the feature limits the maximum achievable wall height, slot depth, and hole depth. Tall thin features are at risk of toppling or warping during sintering while sharp turns within internal channels may hinder depowdering without the use of custom attachments.
Download the Design Guide Now
Design for Additive Manufacturing requires a thoughtful approach that bridges the gap between creativity and the technical realities of 3D printing, ensuring designs are not only manufacturable but also optimized for performance.
DfAM for binder jet is accelerating adoption of lighter, stronger components in industries such as aerospace, automotive, and medical devices. By leveraging advanced simulation tools, material science, and data-driven design techniques, manufacturers can push the boundaries of what’s possible with binder jetting.
Download our Binder Jetting Design Guide to learn more tips about DfAM for binder jet