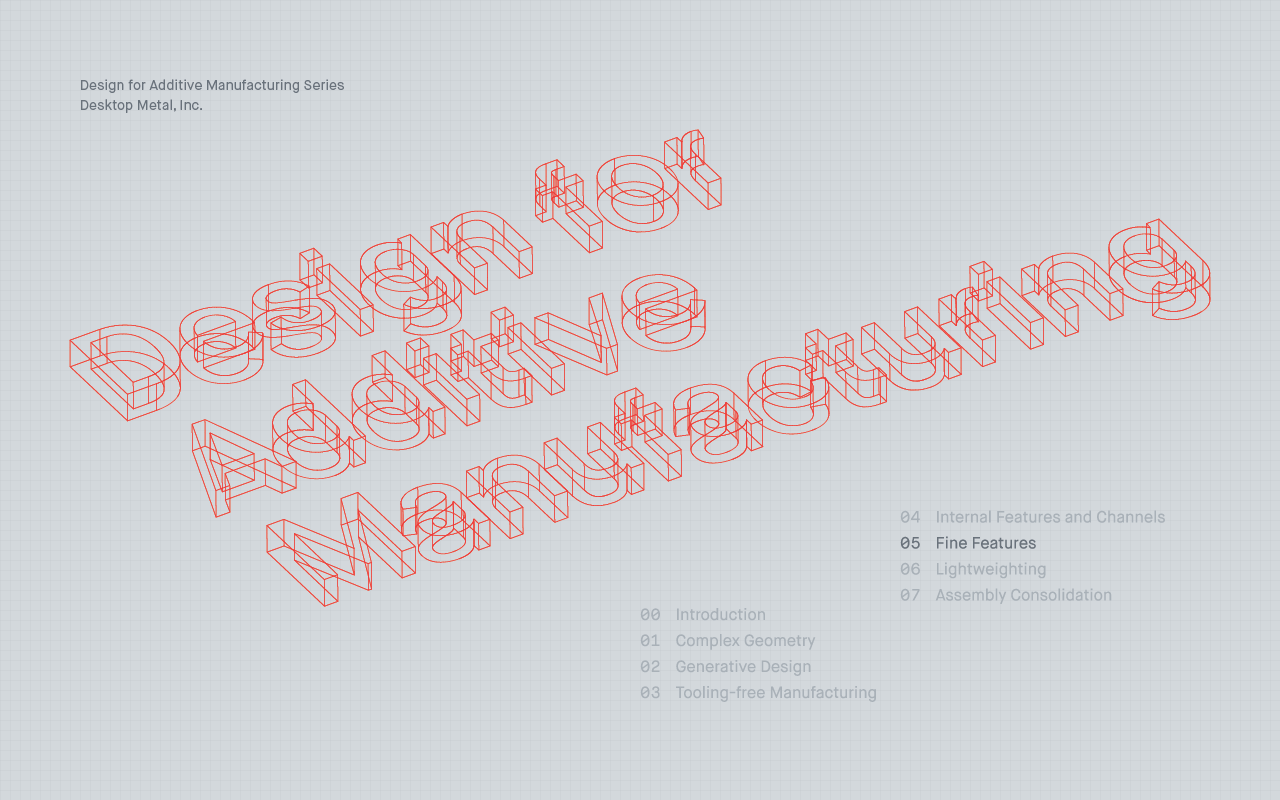
Design for Additive Manufacturing: Lightweighting
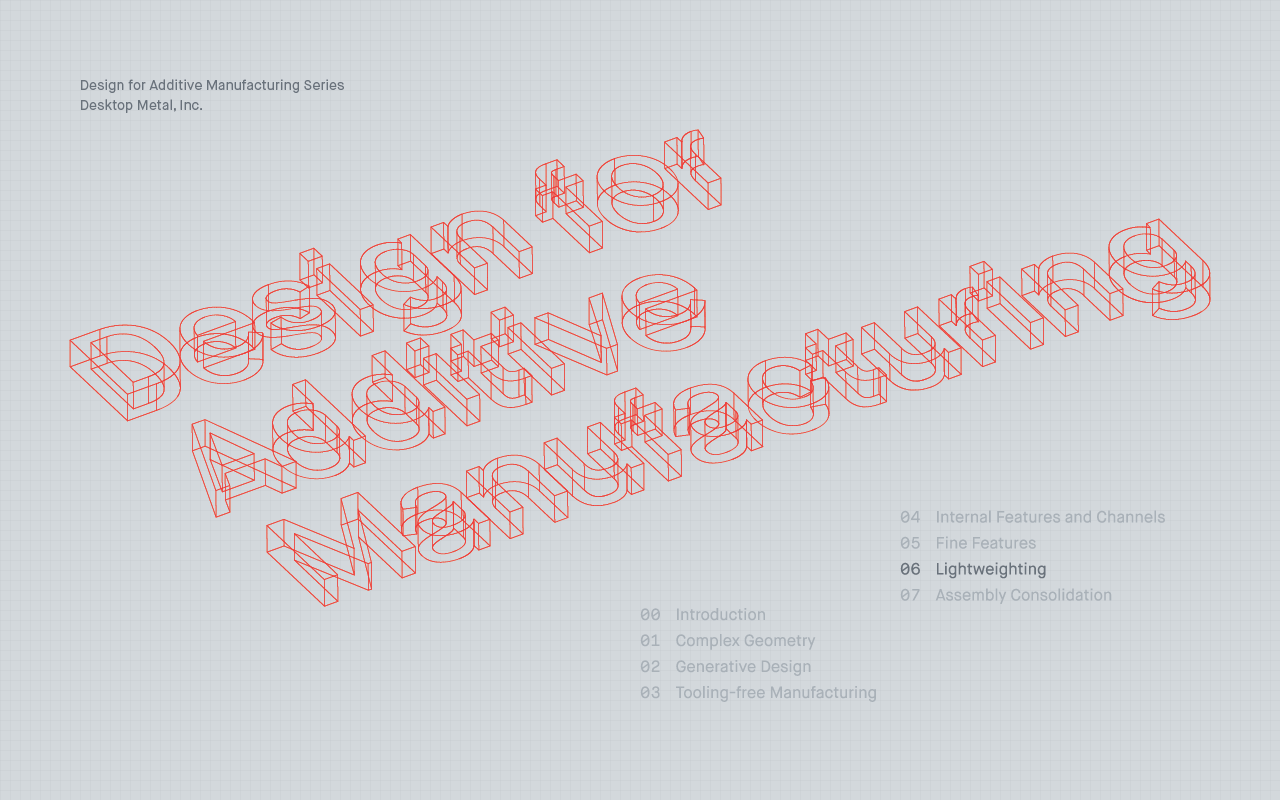
Introduction
Additive manufacturing’s ability to create complex geometry also opens the door to lightweighting parts through the use of lattice-like designs, closed-cell infill and lightweighting features that normally couldn’t be justified with traditional manufacturing.
For most traditional manufacturing processes, lightweighting equals increased cost, lead time and waste, but the additive nature of 3D-printed parts means lightweighting actually reduces waste, leading to shorter processing times and lower part costs.
On the manufacturing floor, meanwhile, lightweight manufacturing aids like end-of-arm tooling equals less wear-and-tear on machinery motors and bearing, and less downtime for production lines.
Infill density and wall thickness can also be tuned to optimize part performance by adding increased part strength or to provide additional material to allow a part to be machined to critical tolerances.
Internal Features and Channels
In addition to new features, additive manufacturing’s ability to create complex geometry opens the door to lightweighting parts through the use of lattice-like designs and closed-cell infill and lightweighting features that normally couldn’t be justified with traditional manufacturing.
While it means increased cost, lead time and waste for most manufacturing processes, the additive nature of 3D-printed parts means lightweighting reduces waste, leading to shorter processing times and lower part costs.
On the manufacturing floor, meanwhile, lightweight manufacturing aids like end-of-arm tooling equals less wear-and-tear on machinery motors, bearings, etc and less downtime for production lines.
Infill density and wall thickness can also be tuned to optimize part performance by adding increased part strength or to provide additional material to allow a part to be machined to critical tolerances.
Part Examples
APG End of Arm Tool
This end of arm tooling is used to hold a camshaft during an induction heat treatment process.
The original part was machined from steel, but was so heavy it caused excessive wear on the motors of the robotic arms holding them. To ensure they could replace the end effectors quickly and keep manufacturing lines up and running, APG turned to the Studio System™ to add coring to the part, dramatically reducing its weight.
Machining those coring features would add significantly increase both cost and manufacturing lead time - more cuts equal more material removal and longer machining time.
With 3D printing, those features actually reduce part cost and manufacturing lead time. Parts that are lightweight print and debind faster, and use less material resulting in a less expensive part. Printing end of arm tools allows APG to significantly reduce part cost, manufacturing lead time, and incorporate light weighting features.
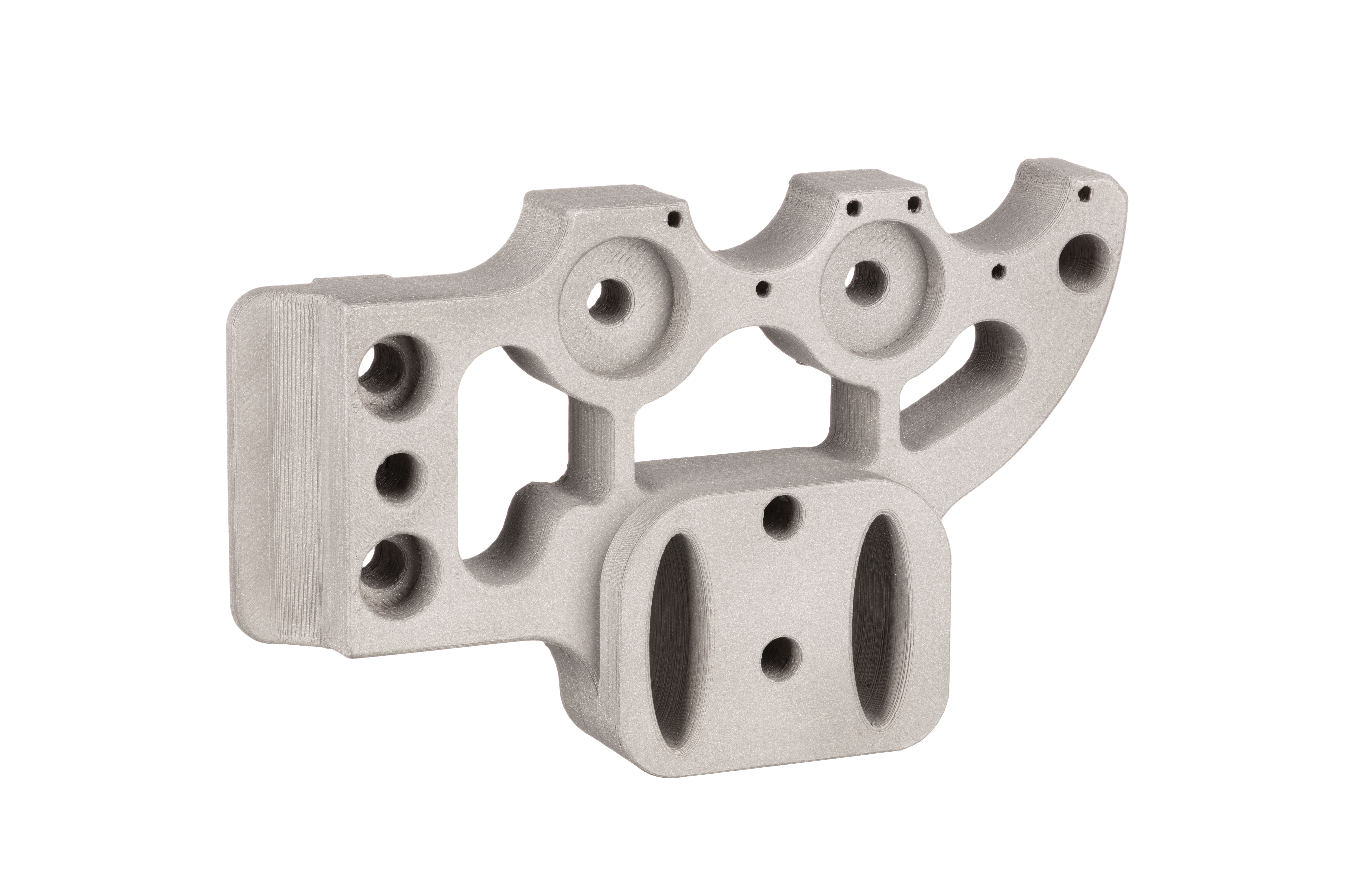
Support Plate
When off-the-shelf spacer options proved inadequate, the designer of this support plate looked to utilize the Shop System™ for its speed and low per-part cost.
Since weight is a critical factor in the design, printing this support plate allowed designers to remove most of the weight from this part while still leveraging the strength of steel to provide the needed part strength.
By adding lightweighting features like the cutouts in this part, 3D printing can lower part costs by reducing material usage.
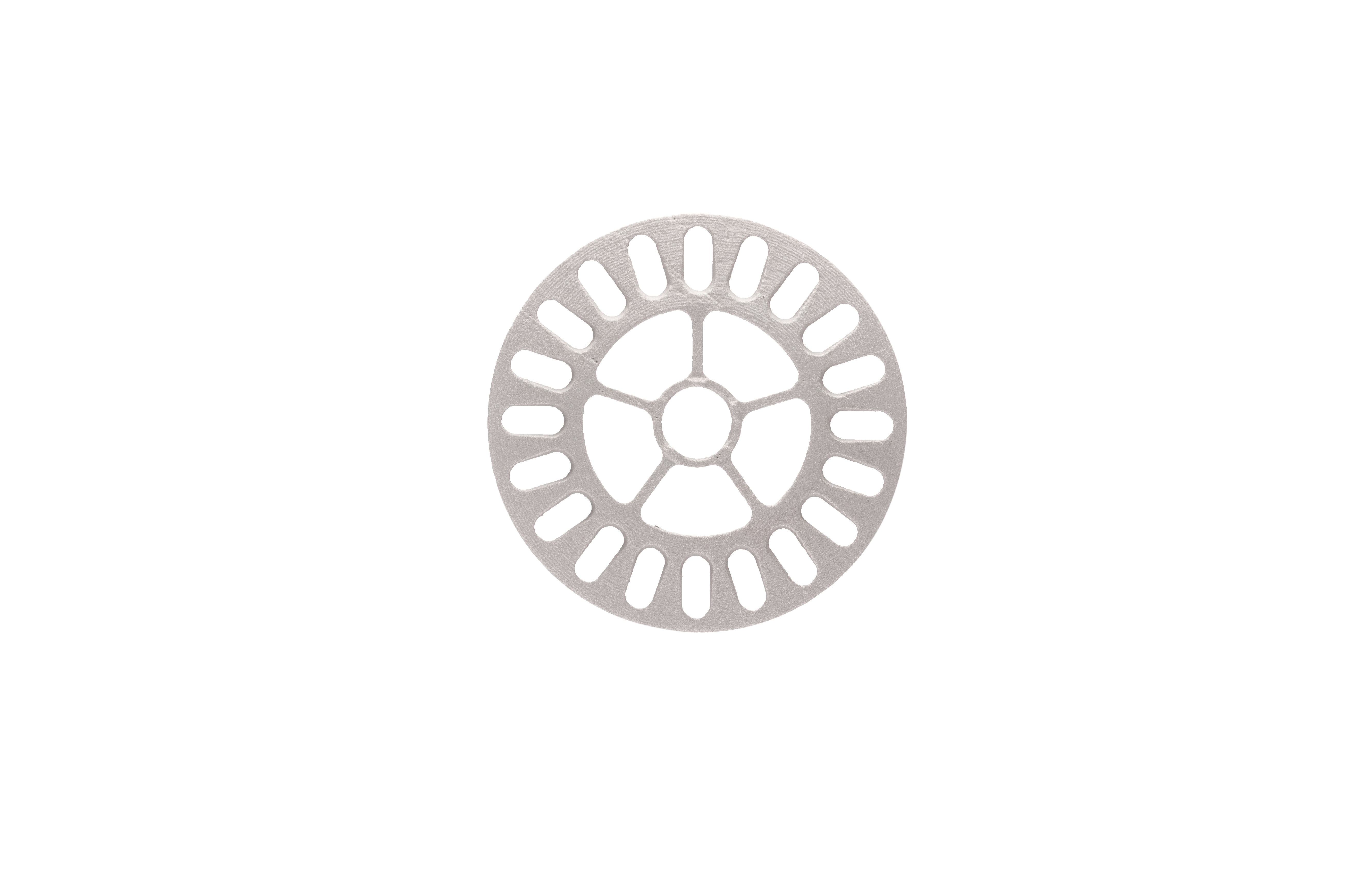
Egar timing belt pulley
This timing belt pulley attaches to a servo motor, and is a key part of the manufacturing environment at Egar Tool and Die.
The design of this part is based on an assembly built from an aluminum extrusion, two screwed-on end plates and a clamp collar. The extruded part also requires extensive machining after extrusion.
By redesigning the part, Egar engineers were able to consolidate the entire assembly into just one piece. This also significantly reduced the weight of the part, allowing the servo motors to run faster, leading to an improved manufacturing environment.
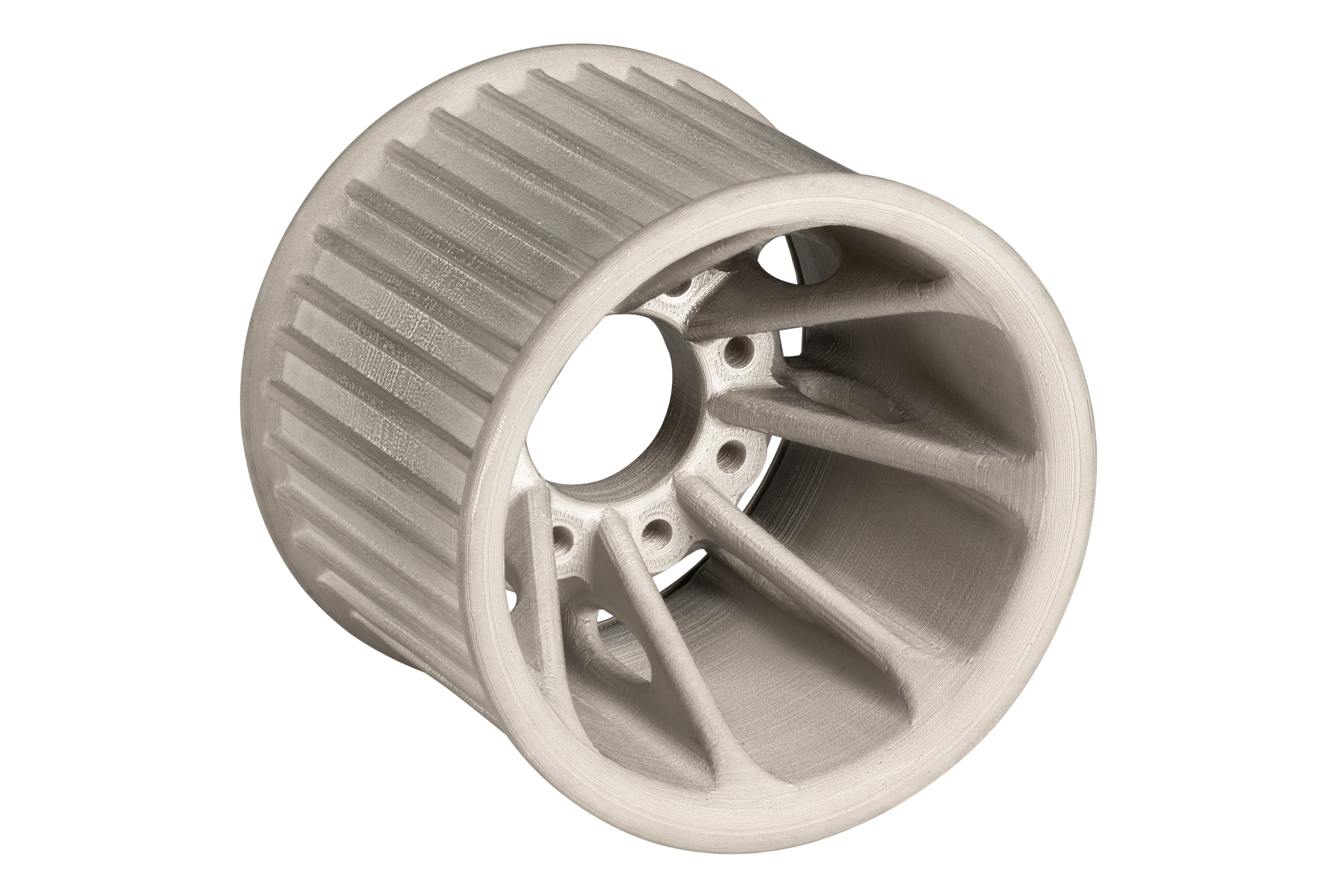