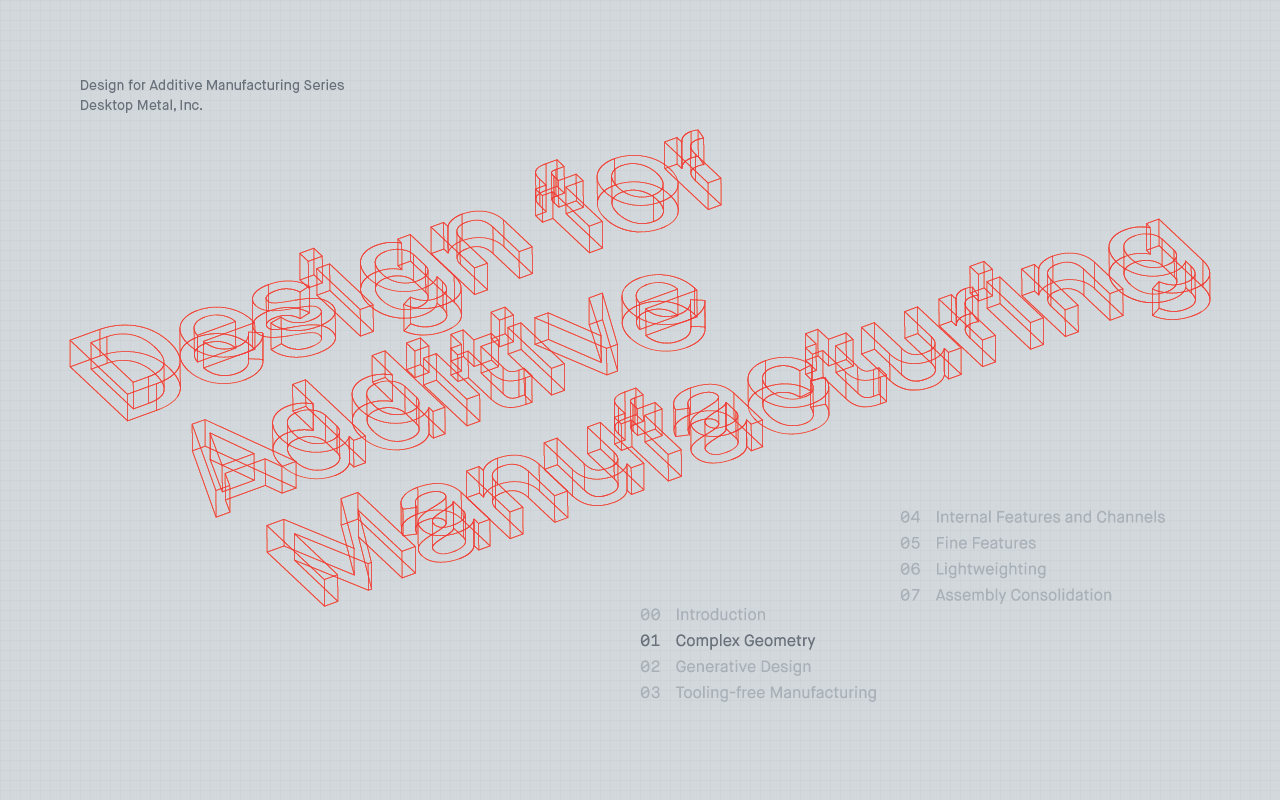
Design for Additive Manufacturing: Generative Design
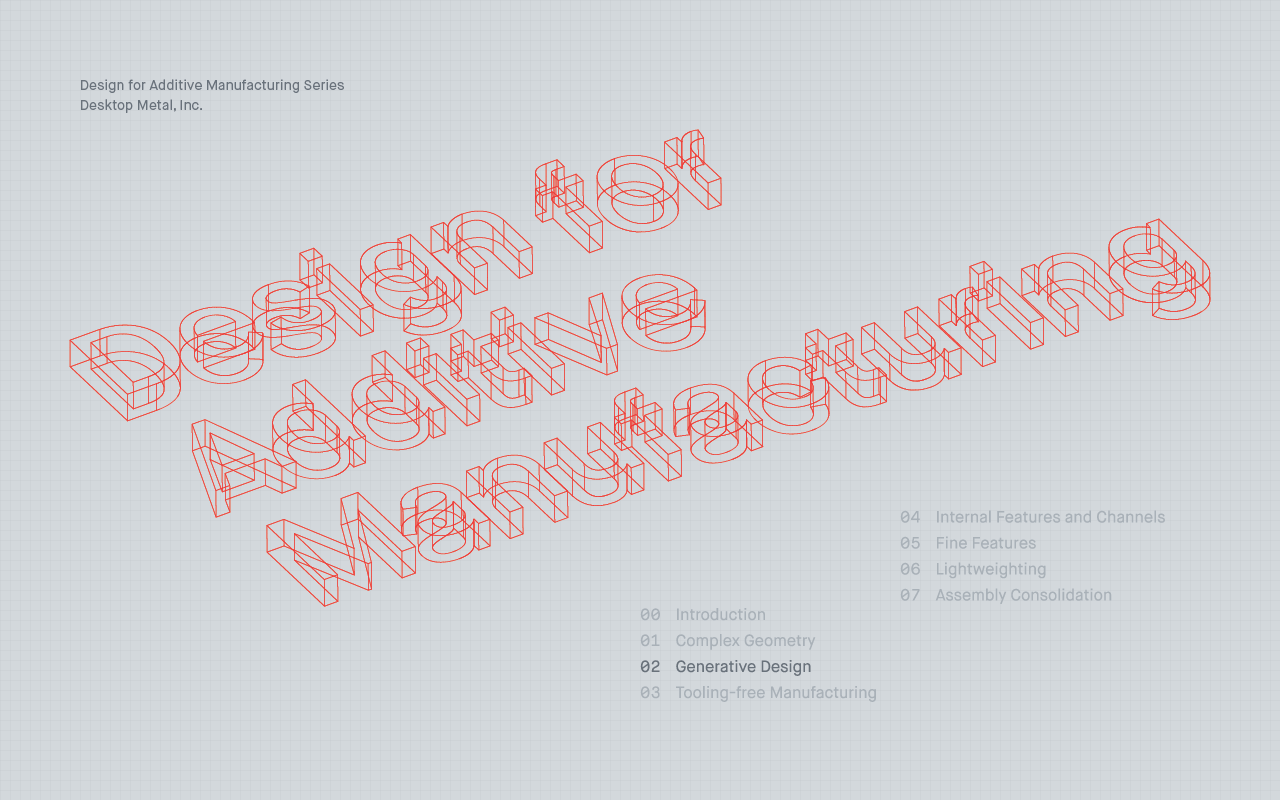
Introduction
Additive manufacturing is rapidly rewriting the rules of how metal parts are made, and it’s doing it with the help of a new design language - Design for Additive Manufacturing (DfAM).
Developed to take advantage of the enormous design freedom that comes with 3D printing, DfAM allows manufacturers unlock a host of benefits - from highly complex geometry to assembly consolidation to the use of generative design tools - and create parts that would otherwise be too difficult or costly to justify with traditional manufacturing methods.
Generative Design
Arguably the most extreme example of the geometric complexity made possible with 3D printing, generative design uses software tools to create highly-optimized parts backed by complex computational simulations.
Built to withstand specific loads and designed according to user-defined constraints, generative parts only put material where it’s needed, resulting in parts that are as much as 50 percent lighter - yet equally strong - than conventional designs.
Creating the complex geometry of generative parts via traditional methods would not only be difficult - if not impossible - but would also be wildly expensive and time-consuming, making additive technology the only way to access this new design space.
Part Examples
Cifarelli Shaker Hook
Located in Milan, Italy, EWOL is a leading vendor of high-tech marine propellers for sailing yachts.
A leading vendor of agriculture and gardening equipment, Cifarelli is located in Voghera, Italy.
Shaker hooks are used in many parts of the world to vibrate tree limbs, causing nuts, fruits, and vegetables to fall so they can be harvested. This specific shaker hook is best for olives, harvesting over 2,000 kg of olives per day, and can remove 95% of the fruit without damaging the tree or its buds.
Though generally produced in lots of approximately 1,000 via aluminum chill casting, Cifarelli does have the need for low-volume production of shaker hooks for specific customers, fruits, and regions. Due to the cost of investing in tooling, however, custom shaker hooks cannot economically be produced in low volumes.
Seeking a more economical production method for low-volume, custom shaker hooks, Cifarelli turned to the Desktop Metal Studio System™. Since the part would be printed in steel, Cifarelli redesigned it to ensure it was no heavier than the original aluminum component, as low weight is essential to reducing strain on the motor.
Created using generative design tools, the final design of the shaker hook would be incredibly difficult, if not impossible, to manufacture, but the additive nature of the Studio System™ made printing the part easy for Cifafelli. The end result is a redesigned shaker hook which, while weighing the same as aluminum shaker hooks, is far more durable and optimized for its application.
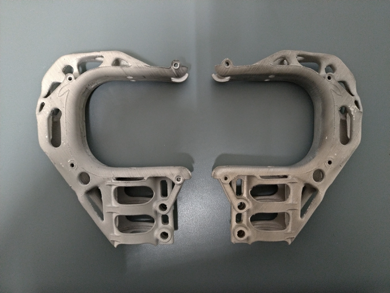
Turner Motorsports Engine Mount
Turner Motorsport is a BMW race team and auto shop for ultra high-performance BMW cars.
Among the custom jobs Turner has taken on was an effort to marry a modern V8 engine with a 2001 BMW M3 which is often cited as one of the best handling sports cars of all time.
Many of the parts needed to combine the two, however, were not compatible, forcing Turner engineers to create custom workarounds to get the engine into the car. Among the components that had to be replaced were the original motor mounts, which hold the engine in the car’s frame.
To create custom mounts, Turner engineers first scanned the original mounts, then loaded the scans into Live Parts™, a generative design software package designed by Desktop Metal.
Live Parts™ allows users to specify “keep out” zones, or areas where the part geometry cannot go. In this situation the keep out zones were essential to ensuring the new engine mounts didn’t interfere with the mechanics of the rest of the car.
Turner engineers then applied loading scenarios to the model, and the part “grew” into an optimized engine mount that mimics organic shapes found in nature. The end result is an optimized, lightweight part that fits the space perfectly, and could be produced in months less time than traditional manufacturing methods like casting or machining.
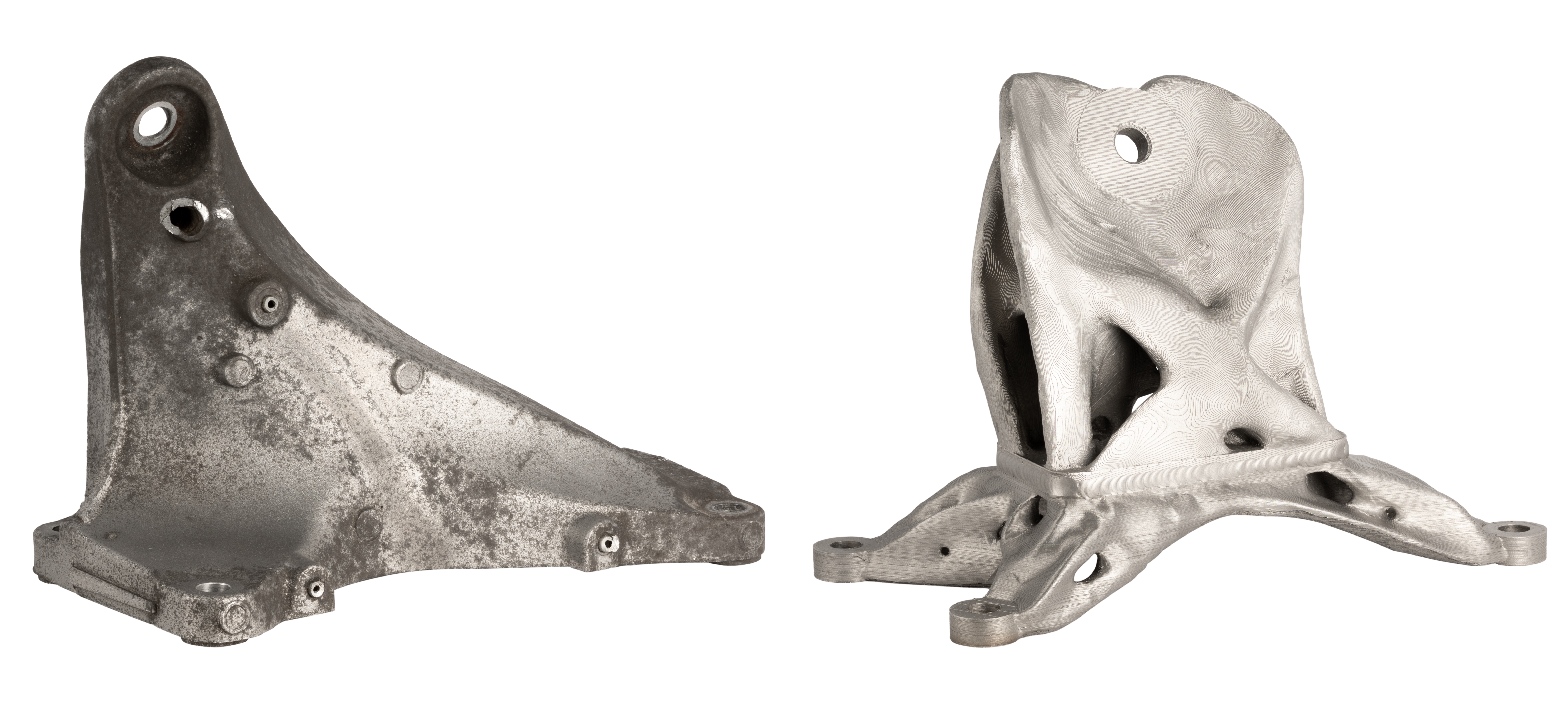
Skateboard Truck
This skateboard truck was redesigned from the original cast component to be printed on the Desktop Metal Shop System. Generative design allowed for the part to be significantly lightweighted while actually adding part strength, since the material changed from Aluminum to Steel.
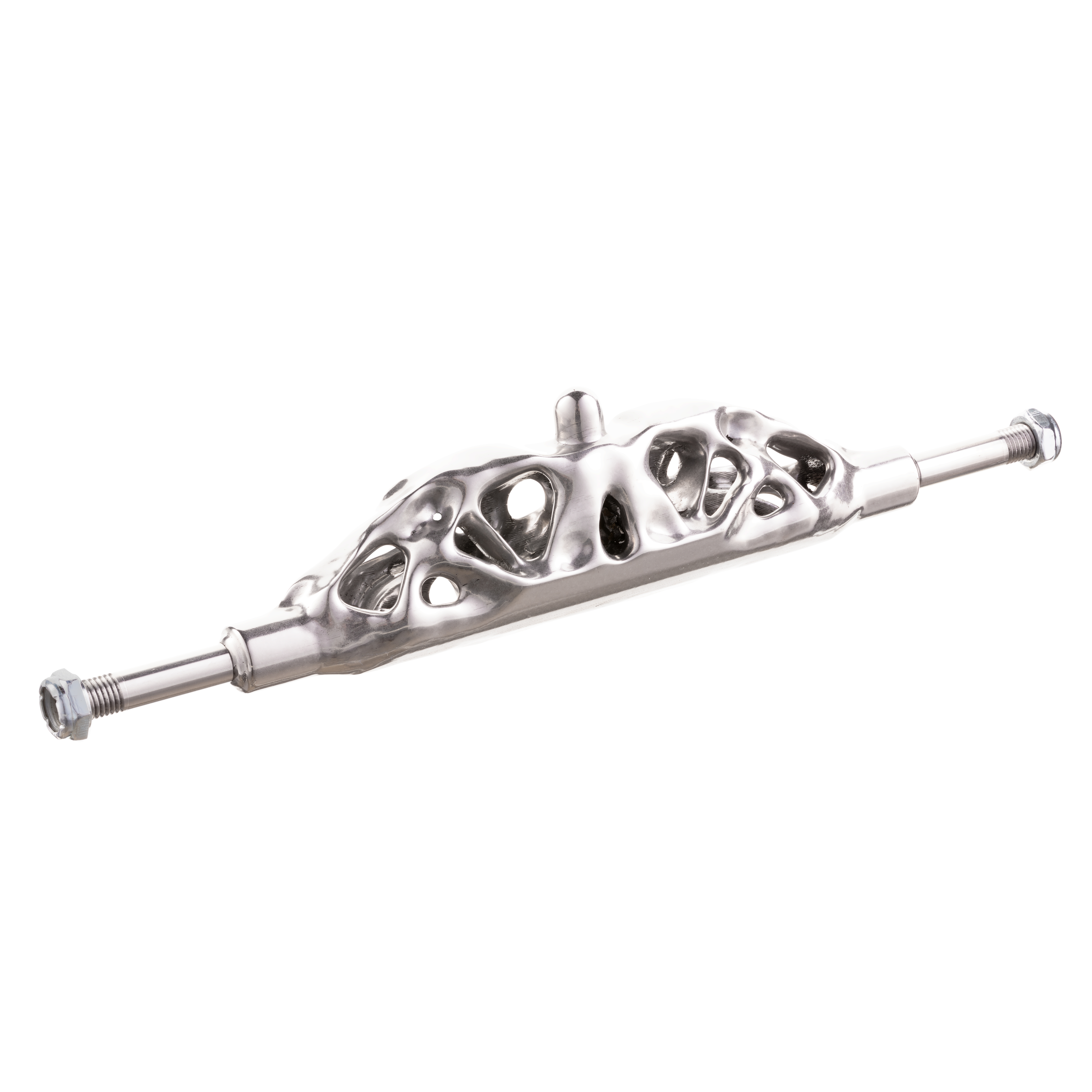