Unlocking 3D Printing Research Potential at Universities
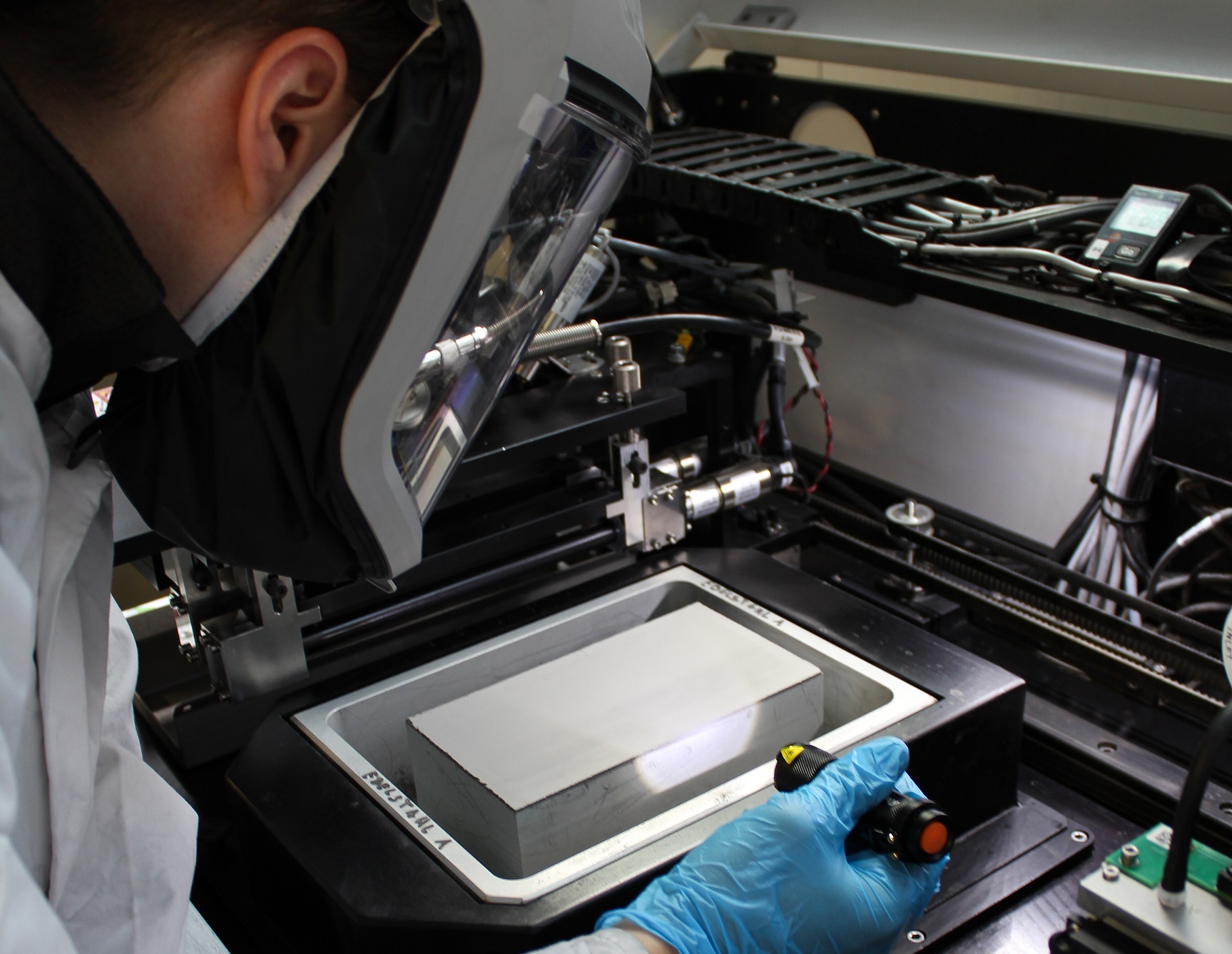
Universities integrating metal 3D printing research drive significant advancements in the understanding and application of additive manufacturing technology. Operating in labs for nearly a decade, the InnoventX is the best binder jet metal 3D printer for research as it produces complex, high-density parts in a range of materials without the need for high-energy laser sources, setting it apart from other AM processes like laser powder bed fusion (L-PBF).
Binder jet technology inkjets a binder into a bed of powder particles such as metal, sand, or ceramic to create a solid part, one thin layer at a time. Because the process is carried out at low temperatures, an array of materials can be 3D printed and post-processed in a variety of ways, from sintering to infiltration. Binder jet technology relies on the physical characteristics of the powder, essentially agnostic to the chemical and phase structure of the material.
The InnoventX is the most-researched binder jetting platform in the world, known for its easy operation and open architecture that make it perfect for all sorts of of investigative purposes, from mechanical processing to new material development. Its compact footprint provides ergonomic operation and the small build box is suitable for environments with quick material changeover and without a large investment in powder.
How is the InnoventX used in the field? These recent studies highlight just a few examples from teams around the world who rely on the best binder jet metal 3D printer for universities to conduct impactful research.
Binder jetting and melt infiltration for ceramic-metal fuel fabrication
Researchers at Yonsei University and the Korea Atomic Energy Research Institute investigated binder jetting to fabricate CERMET preforms on the InnoventX with precise control over the particle distribution, addressing the challenges associated with particle agglomeration and ensuring preform shape integrity. The study emphasized the significance of controlling wettability and surface energies for subsequent melt infiltration, focusing on the interfacial reactions between Zr2Cu and ZrO2. The results indicate that binder jetting can significantly enhance the thermal and irradiation performance of CERMET fuels.
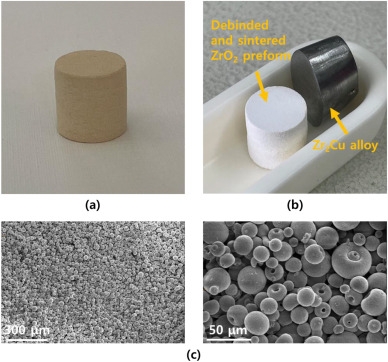
Impact of part thickness and drying conditions on saturation limits in binder jet additive manufacturing
Growth in binder jetting applications is driven by the use of finer powders and improved post-processing methods that can produce dense, homogenous final parts. However, understanding of the basic droplet/powder interaction is relatively limited.
The CREATE Lab and Brigham Young University considered the impact of in-process drying, part geometry, and droplet size on a key printing parameter of binder jet additive manufacturing: binder saturation. Using the InnoventX, parts of varying thicknesses were printed with a range of saturation levels under various heating conditions. The observations lead to a simple method for determining an appropriate print saturation parameter for a powder/binder combination in thick parts.
3D printing of potassium sodium niobate by binder jetting: Printing parameters optimisation and correlation to final porosity
Binder jetting technology allows the creation of complex parts with a high degree of precision and tailoring of piezoelectric properties, thus amplifying, suppressing, or reversing the device's response. Politecnico di Milano researchers used the InnoventX to investigate the main printing parameters correlated to the binder distribution and infiltration – binder saturation, binder set time, drying time, and target bed temperature. The results indicate that binder jetting can be used to fabricate high-precision KNN components with good piezoelectric properties.
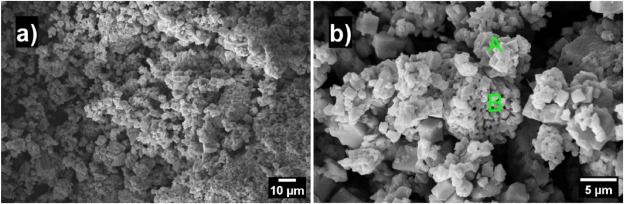
Evaluating the sintering behaviors of ceramic oxide powders processed via binder jet additive manufacturing
Researchers with Carnegie Mellon University and Benemérita Universidad Autónoma de Puebla used the InnoventX binder jetting system, known for processing a range of materials including ceramic oxides, to investigate the production of oxide ceramic parts with desirable densities by sintering 3D printed preforms of three powders with distinct morphologies: ball‐milled alumina, gas‐atomized silica, and sintered‐agglomerated zirconia. The team concluded that regardless of powder morphologies, binder jetting met expectations for production, leading to increased robustness of the supply chain.
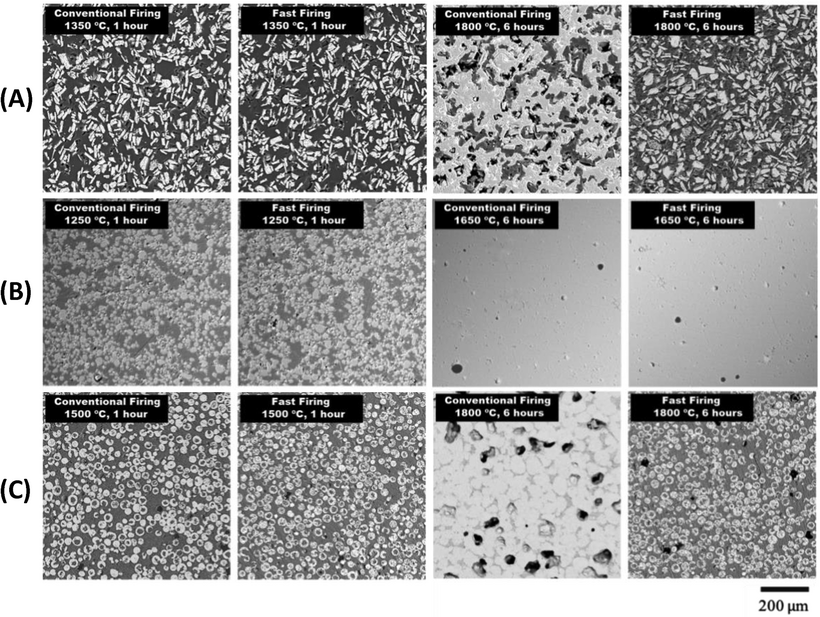
Role of powder morphology in liquid phase sintering of binder jet additively fabricated WC–Co composite
The Center for Agile and Adaptive Additive Manufacturing at the University of North Texas uses the Innovent to research binder jetting technology. A recent study aimed to develop an integrated computational approach to understand the evolution of capillary force and subsequent capillary pressure when particle morphology gradually transitions from sphere to cube during liquid phase sintering of WC–10Co. Printing both spherical and non-spherical particle morphologies on the InnoventX, researchers verified and correlated the computational model-based predictions.
InnoventX - The Best Metal 3D Printer for University Research
What could you study with the compact footprint and open material platform of the InnoventX, the best metal 3D printer for university research?